PDCA
Le PDCA, qui signifie Plan-Do-Check-Act, (en français Planifier, Faire, Contrôler, Agir) est l’une des méthodes les plus efficaces pour l’amélioration continue des processus, en particulier dans le domaine de la maintenance industrielle.
Également connue sous le nom de cycle de Deming ou de roue de Deming, cette approche systématique a été mise au point par Walter A. Shewhart, puis popularisée par W. Edwards Deming.
Mais qu’est-ce que la méthode PDCA et pourquoi est-elle si importante pour la maintenance industrielle ? Dans cet article, nous allons explorer en profondeur la méthode PDCA, ses étapes, ses applications pratiques et les avantages qu’elle offre aux organisations, ainsi que la manière de la mettre en œuvre dans le domaine de la maintenance.
Qu’est-ce que le cycle PDCA ?
Le cycle PDCA, également connu sous le nom de roue de Deming, est une méthode de gestion de la qualité composée de quatre phases interconnectées :
- Planifier (Plan) : Identifier un problème ou une opportunité d’amélioration, définir des objectifs clairs et mesurables, et planifier les actions nécessaires pour atteindre ces objectifs.
- Faire (Do) : Mettre en œuvre le plan à petite échelle, collecter des données et contrôler les résultats.
- Vérifier (Check) : Analyser les données collectées, comparer les résultats avec les objectifs fixés et identifier les écarts éventuels.
- Agir (Act) : Si les résultats sont satisfaisants, normaliser le processus amélioré. Dans le cas contraire, apporter les modifications nécessaires et répéter le cycle.
Ce cycle vertueux est répété en permanence, ce qui permet aux entreprises d’affiner constamment leurs processus et d’atteindre des niveaux d’efficacité toujours plus élevés.
PDCA : définition et origines
Le PDCA est un modèle itératif qui favorise l’amélioration continue grâce à ses quatre phases principales : Planification (Plan), Exécution (Do), Vérification (Check) et Action (Act). Ce cycle, souvent représenté sous la forme d’une roue de Deming, a été introduit par Shewhart dans les années 1920, puis adopté par Deming, qui en a fait un élément central de la philosophie de gestion de la qualité. Mais quelle est la différence entre le PDCA et la roue de Deming ? En fait, les deux termes sont souvent utilisés comme synonymes, car ils désignent tous deux le même processus cyclique.
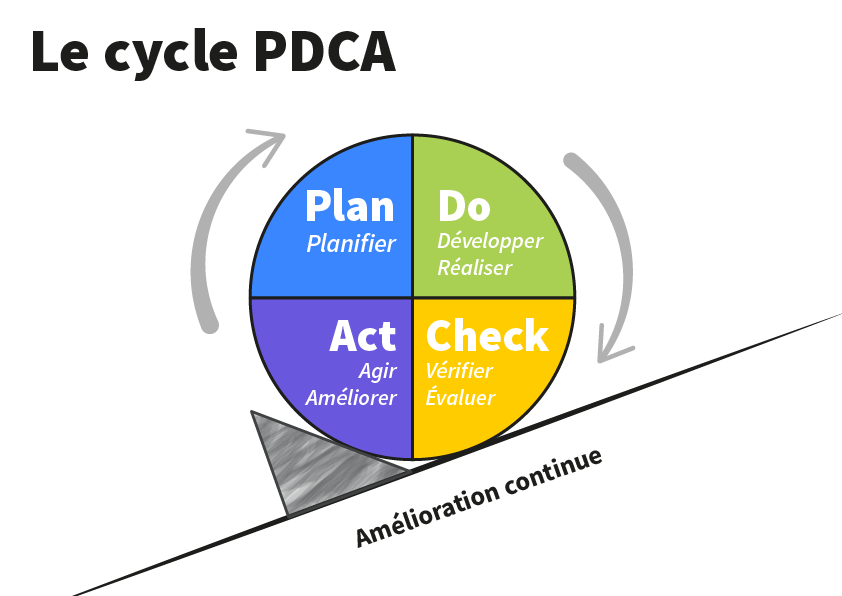
Différences entre DMAIC et PDCA
Le DMAIC (Définir, Mesurer, Analyser, Améliorer, Contrôler) et le PDCA sont tous deux des méthodologies d’amélioration continue, mais ils présentent quelques différences essentielles. La méthode DMAIC est généralement utilisée pour des projets d’amélioration plus complexes et structurés, tandis que la méthode PDCA convient mieux à des projets d’amélioration plus simples et itératifs.
- DMAIC : approche plus structurée, idéale pour les projets complexes aux objectifs bien définis.
- PDCA : approche plus souple et itérative, adaptée aux projets d’amélioration continue et à la résolution de problèmes spécifiques.
Le choix entre DMAIC et PDCA dépend de la nature du problème à traiter et des ressources disponibles. Dans de nombreux cas, les entreprises utilisent les deux approches dans différents domaines de l’organisation.
L’importance du PDCA dans la maintenance
La maintenance est un domaine critique pour les entreprises de tous les secteurs, mais surtout pour l’industrie manufacturière.
Une gestion attentive de la maintenance permet non seulement de prolonger la durée de vie des équipements, mais aussi de réduire les temps d’arrêt, d’améliorer la sécurité sur le lieu de travail et d’optimiser la qualité des produits. Le cycle PDCA s’avère être un outil précieux pour relever les défis de la maintenance industrielle, car il offre une approche systématique pour
- Identifier les causes profondes des problèmes : analyser les données relatives aux défaillances des équipements, aux temps de réparation et aux coûts de maintenance afin d’identifier les domaines critiques nécessitant des interventions ciblées.
- Élaborer des solutions efficaces : concevoir des interventions de maintenance préventive, améliorer les procédures d’exploitation et former le personnel pour minimiser les pannes et maximiser l’efficacité.
- Contrôler les résultats : Évaluer l’efficacité des interventions mises en œuvre en mesurant les temps d’arrêt, les coûts de maintenance et la satisfaction du personnel.
- Normaliser les meilleures pratiques : définir des procédures opérationnelles normalisées sur la base des résultats obtenus, en veillant à ce que les améliorations soient durables dans le temps.
Les étapes du cycle PDCA
1.Planification (Plan)
La phase de planification est le fondement d’un cycle PDCA efficace. Dans cette phase, il est essentiel de définir clairement les objectifs à atteindre et d’élaborer un plan détaillé pour y parvenir :
- Analyse des données existantes : Recueillir et analyser les données relatives aux défaillances des équipements, aux délais de réparation, aux coûts de maintenance et à la fréquence des interventions.
- Identification des problèmes : identifier les domaines critiques qui nécessitent une action ciblée, tels que les équipements obsolètes, les procédures opérationnelles inefficaces ou le manque de formation du personnel.
- Fixation des objectifs : Fixer des objectifs clairs, mesurables, réalisables, pertinents et définis dans le temps (SMART).
- Élaboration du plan d’action : définir les actions spécifiques qui seront entreprises pour atteindre les objectifs fixés, comme la mise en œuvre d’un programme de maintenance préventive, la formation du personnel ou l’achat de nouveaux équipements.
- Définition des indicateurs clés de performance (KPI) : identifier les KPI qui seront utilisés pour suivre les progrès et évaluer l’efficacité des actions mises en œuvre.
2. Réalisation (Do)
La phase d’exécution est celle où le plan d’action est mis en pratique, généralement à petite échelle ou dans un environnement contrôlé. Cette approche permet de tester les solutions proposées et d’apporter des changements avec souplesse, sans compromettre l’ensemble de l’opération :
- Mise en œuvre du plan : mise en pratique des actions définies lors de la phase de planification, telles que la réalisation d’une maintenance préventive ou la mise en œuvre de nouvelles procédures d’exploitation.
- Collecte de données : Recueillir des données sur le temps nécessaire à la réalisation des interventions, les coûts encourus, la fréquence des pannes et la satisfaction du personnel.
- Suivi des progrès : vérifier que les actions sont menées conformément au calendrier prévu et que les résultats sont conformes aux objectifs.
3. Vérification (Check)
La phase de vérification est cruciale pour évaluer l’efficacité des actions entreprises et identifier tout écart par rapport aux objectifs fixés. Au cours de cette phase, les données collectées sont analysées et comparées aux objectifs afin de déterminer si le plan d’action a produit les résultats escomptés :
- L’analyse des données : Analyse des données collectées au cours de la phase « Faire » afin d’identifier les tendances, les anomalies ou les domaines à améliorer.
- Comparaison avec les objectifs : Comparer les résultats obtenus avec les objectifs fixés lors de la phase de planification afin de déterminer s’ils ont été atteints.
- Identification des écarts : Identifier les écarts éventuels entre les résultats obtenus et les objectifs préétablis et analyser les causes de ces écarts.
4. Agir (Act)
La phase « Agir » est celle où les décisions sont prises sur la base des résultats de la phase « Vérification ». Si les résultats sont satisfaisants, le processus amélioré est normalisé et mis en œuvre à grande échelle. Dans le cas contraire, les modifications nécessaires sont apportées au plan d’action et le cycle PDCA est répété :
- Normalisation du processus : définir des procédures opérationnelles normalisées sur la base des résultats obtenus, en veillant à ce que les améliorations soient durables dans le temps.
- Mise en œuvre à grande échelle : mettre en œuvre le processus normalisé dans tous les domaines concernés de l’entreprise.
- Amélioration continue : continuer à surveiller les résultats et apporter des modifications au processus normalisé sur la base de nouvelles informations et de l’évolution des besoins de l’entreprise.
Outils pour l’élaboration d’un plan PDCA
Le cycle PDCA offre un cadre structuré pour identifier les problèmes, trouver des solutions et les mettre en œuvre efficacement, tout en minimisant le risque d’erreurs grâce à l’expérimentation. Pour maximiser les chances de réussite de vos projets de maintenance, il est essentiel de suivre attentivement les quatre phases du cycle :
1. Planifier (Plan) :
Commencez par identifier et définir précisément le problème ou l’opportunité d’amélioration. Pour vous aider dans cette phase, vous pouvez utiliser des outils tels que :
- Brainstorming : pour générer des idées et des solutions créatives.
- CATWOE : pour analyser le problème sous différents angles (clients, acteurs, transformation, vision du monde, propriétaire, contraintes).
- Analyse 80/20 (ou 20/80) : identifier les causes profondes du problème (20 % des causes générant 80 % des effets).
Une fois le problème défini, il est nécessaire d’identifier ses causes profondes.
Pour ce faire, vous pouvez utiliser des outils tels que :
- Le diagramme d’Ishikawa (ou diagramme en arête de poisson, fishbone diagram en anglais) : pour identifier les causes possibles du problème, en les regroupant par catégories (main-d’œuvre, matériaux, méthodes, machines, mesures, environnement).
- Les 5 raisons : Pour creuser en profondeur et identifier la cause première du problème, en posant plusieurs fois la question du « pourquoi ».
Enfin, il est nécessaire de faire l’inventaire des solutions possibles et de décider laquelle mettre en œuvre. Les outils utiles à cette phase sont les suivants
- Arbre de décision : pour évaluer les différentes options et choisir la plus appropriée.
- Matrice de décision : pour comparer les différentes options en fonction de critères spécifiques et choisir celle qui répond le mieux aux besoins.
Avant de passer à l’étape suivante, il est essentiel de préparer un plan détaillé pour la mise en œuvre de la solution. Ce plan doit comprendre un cahier des charges clair, une estimation des coûts, un calendrier précis et la définition d’indicateurs clés de succès (épi) pour mesurer l’efficacité de la solution.
2. Faire (Do) :
Maintenant que vous avez choisi une solution et préparé un plan détaillé, il est temps de passer à la phase d’essai.
Il est important de choisir un périmètre suffisamment large pour valider vos hypothèses, mais suffisamment restreint pour ne pas compromettre l’ensemble de l’opération. Suivez attentivement les étapes définies dans votre plan et contrôlez les résultats.
3. Vérifier (Check) :
Dans cette phase, vous devez étudier attentivement les résultats des tests pour déterminer si la solution est efficace et si elle peut être généralisée à l’ensemble du champ d’application défini. Les résultats atteignent-ils leurs objectifs ?
Si l’expérience n’est pas satisfaisante, il est important de tirer les leçons de l’expérience et d’identifier les points à améliorer.
4. Agir (Act) :
Sur la base des résultats de la phase de vérification, il est décidé de normaliser les améliorations apportées ou de répéter le cycle avec de nouvelles modifications.
Cette phase clôt le cycle mais ouvre la voie à une nouvelle amélioration. Par exemple, une entreprise peut décider de mettre en œuvre une nouvelle procédure opérationnelle standard (POS) sur la base des résultats obtenus, y compris des activités telles que :
- la budgétisation
- l’organisation des processus
- Organisation des services
- Rédaction de procédures
- la formation du personnel
- Gestion du changement
- Sélection et mise en place d’indicateurs de maintenance (KPI)
Souvent, la phase « Acting » est un projet en soi, où les trois premières phases servent à qualifier une réponse à un problème spécifique.
Fonctionnement du cycle PDCA
Lorsque l’on aborde le cycle PDCA, il est important de noter qu’il existe deux interprétations complémentaires, chacune avec un objectif légèrement différent mais avec le même but d’amélioration continue.
D’une part, nous avons une approche plus générale, qui considère le PDCA comme un ensemble de principes directeurs pour l’amélioration continue. Dans ce modèle, la phase « Faire » se traduit par la mise en œuvre directe de la solution identifiée comme la plus appropriée.
D’autre part, il existe une approche plus expérimentale, qui souligne l’importance de tester et d’analyser la solution sur un échantillon limité avant de procéder à une mise en œuvre à grande échelle. Cette approche réduit les risques et permet d’apporter des changements et des améliorations de manière plus agile et plus souple.
Dans la pratique, le choix entre ces deux approches dépend du contexte et de la nature du problème à résoudre.
Par exemple, s’il s’agit de mettre en œuvre une nouvelle procédure de maintenance sur toutes les lignes de production, il peut être judicieux de commencer par un test sur une seule ligne afin d’évaluer son efficacité et d’identifier les problèmes éventuels.
À l’inverse, s’il s’agit de résoudre un problème spécifique sur un équipement, il peut être plus approprié d’appliquer directement une solution basée sur l’analyse des données et l’expérience du personnel.
Quelle que soit l’approche choisie, il est essentiel de se rappeler que le cycle PDCA est un processus itératif et continu. Il ne s’agit pas simplement d’une série d’étapes à suivre une fois, mais d’un cycle qui est constamment répété pour s’assurer que les processus de maintenance sont toujours efficients, efficaces et alignés sur les besoins de l’entreprise.
Il est intéressant de noter que la représentation graphique du cycle PDCA comprend souvent un coin, qui symbolise la direction sans ambiguïté du processus. Ce coin nous rappelle que le cycle PDCA est un processus d’amélioration continue, et non un processus réversible.
Une fois qu’une action a été entreprise, il est important d’évaluer les résultats et d’apporter les changements nécessaires pour améliorer le processus à l’avenir.
En intégrant ces concepts dans votre approche de la maintenance industrielle, vous pouvez utiliser pleinement la puissance du cycle PDCA pour optimiser vos processus, réduire les coûts et améliorer la qualité de vos produits et services.
Exemple de PDCA
Imaginons un responsable de la maintenance dans une entreprise manufacturière qui souhaite optimiser le programme de maintenance préventive afin de réduire les temps d’arrêt des machines et les coûts de réparation. Voyons comment appliquer le cycle PDCA à ce problème :
- Planifier :
- Identifier le problème : temps d’arrêt excessif des machines et coûts de réparation élevés.
- Analyser les causes : utiliser le diagramme d’Ishikawa pour identifier les causes potentielles (par exemple, une maintenance inadéquate, une lubrification insuffisante, une formation insuffisante du personnel, etc.)
- Définir la solution : mettre en œuvre un programme de maintenance préventive optimisé sur la base de l’analyse des données historiques de défaillance et des recommandations des fabricants de machines.
- Définir les indicateurs de réussite : réduction de 15 % des temps d’arrêt et de 10 % des coûts de réparation dans les six mois.
- Planifier la mise en œuvre :
- Sélectionner une ligne de production pilote pour tester le programme de maintenance optimisé.
- Définir des procédures de maintenance préventive spécifiques aux machines.
- Former le personnel à l’exécution correcte des procédures.
- Mettre en place un système de suivi des temps d’arrêt et des coûts de réparation.
- Faire :
- Mettre en œuvre le programme de maintenance préventive optimisé sur la ligne de production pilote.
- Exécuter les procédures de maintenance préventive conformément au calendrier établi.
- Recueillir des données sur les temps d’arrêt, les coûts de réparation et la satisfaction du personnel.
- Vérifier :
- Analyser les données collectées pour comparer les résultats aux objectifs fixés.
- Évaluer si le programme de maintenance optimisé a permis de réduire les temps d’arrêt et les coûts de réparation.
- Identifier les éventuels problèmes ou domaines d’amélioration du programme.
- Agir:
- Si les résultats sont positifs :
- Standardisez le programme de maintenance préventive optimisé et mettez-le en œuvre sur toutes les lignes de production.
- Documenter les procédures de maintenance préventive et les rendre accessibles à l’ensemble du personnel.
- Contrôler en permanence les temps d’arrêt et les coûts de réparation pour s’assurer que les améliorations sont maintenues dans le temps.
- Si les résultats ne sont pas satisfaisants :
- Analyser les causes des écarts par rapport aux objectifs.
- Apporter les modifications nécessaires au programme de maintenance préventive.
- Répéter le cycle PDCA jusqu’à ce que les résultats souhaités soient atteints.
Cet exemple montre comment le cycle PDCA peut être utilisé pour optimiser le programme de maintenance préventive et améliorer l’efficacité et la fiabilité des machines dans un environnement industriel.
- Si les résultats sont positifs :
Avantages et inconvénients du PDCA
La mise en œuvre du cycle PDCA dans la maintenance industrielle présente de nombreux avantages :
- Amélioration continue : le cycle PDCA favorise une culture d’amélioration continue, encourageant les entreprises à rechercher en permanence des moyens d’optimiser leurs processus.
- Réduction des coûts : L’optimisation des processus de maintenance peut entraîner une réduction significative des coûts grâce à la diminution des temps d’arrêt et des pannes et à l’allongement de la durée de vie des équipements.
- Efficacité accrue : le cycle PDCA aide les entreprises à identifier et à éliminer les gaspillages, améliorant ainsi l’efficacité des processus de maintenance.
- Amélioration de la qualité : une maintenance efficace contribue à améliorer la qualité des produits, en réduisant le risque de défauts et de défaillances.
- Amélioration de la sécurité : le cycle PDCA favorise la sécurité au travail, en réduisant le risque d’accidents et de blessures.
On peut donc dire que la méthode PDCA se caractérise par sa polyvalence et que ses principes généraux la rendent adaptable à différents domaines et facile à appliquer. Grâce à sa simplicité, elle constitue un outil efficace pour optimiser les processus, réduire les gaspillages et promouvoir l’amélioration continue.
L’un de ses principaux atouts est la possibilité de tester les changements à petite échelle avant de les mettre en œuvre à grande échelle, ce qui garantit une approche structurée de l’optimisation. Toutefois, c’est précisément cette caractéristique qui peut rendre l’adoption de la méthode plus lente et moins adaptée aux situations nécessitant une action immédiate.
Pour obtenir des résultats durables, l’implication active de toutes les parties prenantes, en particulier de la direction, est cruciale. Sans un engagement commun, la méthode risque de ne pas produire les bénéfices escomptés.
Outils et techniques pour développer le PDCA
Organigrammes
Les organigrammes sont un outil utile pour visualiser et améliorer les processus au cours du cycle PDCA. Par exemple, une organisation peut utiliser un organigramme pour cartographier les étapes d’un processus et identifier les domaines à améliorer.
Diagrammes de Pareto
Les diagrammes de Pareto sont utiles pour identifier les questions les plus importantes sur lesquelles se concentrer pendant la phase de planification. Par exemple, une entreprise peut utiliser un diagramme de Pareto pour identifier les causes les plus fréquentes de défaillance d’une machine.
Les 5 raisons
La technique des 5 raisons est un outil efficace pour identifier les causes profondes des problèmes au cours du cycle PDCA. Par exemple, une équipe peut utiliser cette technique pour analyser un problème récurrent et élaborer des solutions efficaces.
Comment mettre en œuvre la méthode PDCA
Pour mettre en œuvre avec succès le cycle PDCA dans la maintenance industrielle, il est essentiel de suivre quelques étapes clés :
- Obtenir le soutien de la direction : le succès du cycle PDCA dépend du soutien total de la direction, qui doit fournir les ressources nécessaires et promouvoir une culture d’amélioration continue.
- Former le personnel : il est essentiel de former le personnel aux principes du cycle PDCA et aux techniques d’amélioration continue.
- Définir des objectifs clairs : les objectifs doivent être SMART (spécifiques, mesurables, réalisables, pertinents et limités dans le temps).
- Collecter des données précises : la collecte de données précises est essentielle pour évaluer l’efficacité des interventions mises en œuvre.
- Analyser les données de manière critique : les données doivent être analysées de manière critique afin d’identifier les causes profondes des problèmes et d’évaluer l’efficacité des solutions proposées.
- Normaliser les processus améliorés : les processus améliorés doivent être normalisés pour garantir que les améliorations sont durables dans le temps.
- Contrôler les résultats : il est important de contrôler les résultats au fil du temps pour vérifier que les améliorations sont durables et pour identifier de nouvelles possibilités d’optimisation.
Comment numériser le cycle PDCA
À l’ère de la numérisation, le cycle PDCA peut être amélioré grâce à l’utilisation de logiciels de gestion de la maintenance assistée par ordinateur (GMAO) et d’autres technologies innovantes.
Ces outils permettent de :
- Collecter des données en temps réel : les capteurs IoT (Internet des objets) et autres technologies de surveillance permettent de collecter des données en temps réel sur l’état et les performances des équipements, ainsi que sur l’environnement d’exploitation.
- Analyser les données plus efficacement : des logiciels d’analyse de données et des algorithmes d’intelligence artificielle peuvent être utilisés pour analyser les données collectées et identifier les tendances, les anomalies et les domaines à améliorer.
- Automatiser les processus : les logiciels de GMAO et d’autres technologies d’automatisation peuvent être utilisés pour automatiser les processus de maintenance, tels que la planification des interventions, la gestion des ordres de travail et le suivi des stocks.
- Améliorer la communication et la collaboration : les plateformes de communication et de collaboration en ligne permettent au personnel de maintenance de partager des informations, de coordonner des activités et de résoudre des problèmes plus efficacement.
Contenu de l'article
- Qu’est-ce que le cycle PDCA ?
- PDCA : définition et origines
- Différences entre DMAIC et PDCA
- L’importance du PDCA dans la maintenance
- Les étapes du cycle PDCA
- Outils pour l’élaboration d’un plan PDCA
- Fonctionnement du cycle PDCA
- Exemple de PDCA
- Avantages et inconvénients du PDCA dans la maintenance
- Outils et techniques pour développer le PDCA
– Diagrammes de flux
– Diagrammes de Pareto
– 5 Pourquoi - Comment mettre en œuvre la méthode PDCA
- Comment numériser le cycle PDCA
Découvrez la GMAO mainsim en direct.
Réservez une démonstration pour découvrir comment fonctionne la GMAO grâce à une démonstration personnalisée.
Rejoindre les experts
Ou découvrez le mainim GMAO avec la playlist vidéo.