Les types de maintenance
Les principaux types de maintenance reconnus sont :
- Maintenance Corrective
- Maintenance Curative
- Maintenance Palliative
- Maintenance Préventive
- Maintenance Prédictive
- Maintenance Systématique (ou Maintenance Périodique)
- Maintenance Conditionnelle (ou Condition-based Maintenance)
- Maintenance Programmée (ou Time-based Maintenance)
- Maintenance Améliorative
- Maintenance Évolutive
Qu’est-ce que la maintenance et pourquoi est-elle importante?
- prévenir les pannes
- améliorer l’efficacité et la fiabilité
- réduire les coûts
- garantir la sécurité des installations
- assurer la continuité des opérations
- améliorer la qualité du produit final
- prolonger le cycle de vie des actifs
Contenu de l'article
- Maintenance Corrective
- Maintenance Curative
- Maintenance Palliative
- Maintenance Préventive
- Maintenance Prédictive
- Maintenance Systématique (ou Maintenance Périodique)
- Maintenance Conditionnelle (ou Condition-based Maintenance)
- Maintenance Programmée (ou Time-based Maintenance)
- Maintenance Améliorative
- Maintenance Évolutive
Découvrez la GMAO mainsim en direct.
Réservez une démonstration pour découvrir comment fonctionne la GMAO grâce à une démonstration personnalisée.
Les différents types de maintenance
Maintenance Ordinaire
- Rétablir le fonctionnement d’un bien
- Réparer les pannes ou incidents accidentels
- Assurer la durée de vie utile d’un actif
- Maintenir l’intégrité initiale de l’actif
- Restaurer l’efficacité du système
- Limiter la dégradation normale de l’actif
- Garantir la durée de vie utile du bien
- Remettre en état le système après une panne
Maintenance Extraordinaire
Les objectifs de la maintenance extraordinaire sont :
- Prévenir l’apparition de pannes
- Augmenter la disponibilité et la durée de vie utile d’un actif
- Rationaliser les coûts et réduire les temps de maintenance
- Les interventions sur la structure du système
- Les grands travaux qui introduisent des innovations technologiques ou des améliorations importantes aux installations existantes
Maintenance Corrective
- Maintenance adaptative : ajustements et modifications pour répondre à de nouvelles exigences.
- Maintenance évolutive : mises à jour et améliorations pour augmenter les performances.
- Maintenance non planifiée : interventions imprévues à la suite de pannes soudaines.
- Coûts initiaux réduits
- Simplicité de gestion
- Temps d’arrêt imprévus
- Coûts de réparation élevés
Maintenance Curative
La maintenance curative se focalise sur la réparation des actifs après la survenue d’une panne. Elle est réactive par nature, nécessitant des interventions rapides pour restaurer la fonctionnalité des machines et minimiser les interruptions de production. Contrairement à la maintenance palliative, qui vise à fournir une solution temporaire pour permettre la poursuite des opérations, la maintenance curative aborde le problème de manière plus définitive. Ce type d’intervention peut impliquer le remplacement de composants défectueux par des neufs, assurant ainsi la restauration complète des fonctionnalités de l’équipement. Par exemple, remplacer une ampoule grillée par une neuve relève de ce type de maintenance. Cette approche, bien que souvent coûteuse en termes de temps d’arrêt imprévus, est essentielle pour garantir le retour rapide à un état opérationnel.
Avantages de la maintenance curative
- Réparation définitive
- Réduction des temps d’arrêt
- Impossibilité de planification
- Coûts plus élevés à long terme
Maintenance Palliative
La maintenance palliative fait partie de la catégorie de la maintenance corrective. Ce type de maintenance consiste à appliquer des solutions temporaires pour maintenir en fonctionnement les équipements jusqu’à ce qu’une réparation permanente soit possible. L’objectif est de stabiliser la situation et d‘éviter une détérioration supplémentaire, offrant ainsi une période de répit nécessaire pour planifier et effectuer des réparations complètes sans hâte. C’est le type de maintenance qui, comme nous l’avons vu, est effectué en réponse à une panne, généralement sur des équipements coûteux ou critiques, permettant à l’équipe d’organiser une réparation plus approfondie et durable, éventuellement planifiée ultérieurement, pour éviter un arrêt de production coûteux en termes de temps. Cette forme de maintenance est cruciale pour éviter une interruption totale de la production tout en permettant un fonctionnement réduit.
Avantages de la maintenance Palliative
- Rapidité d’intervention
- Coûts initiaux réduits
- Solutions temporaires
- Risque de pannes récurrentes
Maintenance Préventive
La maintenance préventive englobe plusieurs catégories, toutes visant à optimiser la capacité de production en termes de coûts et de délais.
Les stratégies de maintenance préventive incluent une série d’actions conçues pour ralentir le processus de dégradation d’un bien, d’une machine ou d’une installation. En termes simples, la maintenance préventive consiste en un ensemble d’activités programmées à intervalles réguliers, définies dans un plan de maintenance souvent élaboré pour des actifs coûteux et critiques ou pour maximiser la productivité.
Les interventions de maintenance préventive sont planifiées et réalisées avant qu’une panne ne survienne, avec pour objectif de réduire le nombre de pannes soudaines et les temps d’arrêt imprévus en prenant des mesures proactives. Par conséquent, la maintenance préventive est souvent synonyme de maintenance planifiée.
Pour tirer pleinement parti de la maintenance préventive, il est essentiel de trouver un équilibre entre ce type de maintenance et d’autres approches qui attendent passivement l’apparition d’une défaillance. Ce juste équilibre permet de maximiser l’efficacité des opérations tout en minimisant les coûts et les interruptions.
Avantages de la maintenance Préventive
- Réduction des pannes: Diminue la probabilité des pannes soudaines grâce à une planification proactive.
- Amélioration de la durée de vie des équipements: Les interventions régulières prolongent la durée de vie des machines.
Désavantage de la maintenance Préventive
- Coût des interventions: Les interventions fréquentes peuvent entraîner des coûts élevés, même en l’absence de défaillance.
- Surmaintenance: Risque de remplacer des pièces qui pourraient encore fonctionner correctement, entraînant des dépenses inutiles.
Comment automatiser la Maintenance Préventive
Automatiser la maintenance préventive offre de nombreux avantages : de la réduction des temps d’arrêt à la conformité réglementaire, de la planification optimisée au support pratique pour les techniciens. L’intelligence artificielle (IA) et les logiciels de gestion de la maintenance (GMAO) sont des outils essentiels pour atteindre cet objectif, permettant de planifier, de surveiller et d’optimiser les activités de maintenance de manière précise et automatique.
Un premier pas vers l’automatisation est la génération automatique des ordres de travail répétitifs. Cela permet de définir le nombre de cycles et la fréquence des maintenances programmées, en les configurant une fois pour toutes ou en fonction des conditions spécifiques des équipements, passant ainsi à une maintenance conditionnelle. Grâce à la GMAO, il est possible de planifier les interventions de maintenance en utilisant un calendrier de maintenance. Cet outil permet de partager les ordres de travail avec les techniciens et les fournisseurs, d’assigner des tâches aux différentes personnes impliquées et de surveiller le backlog de maintenance.
Automatiser la maintenance préventive facilite également le suivi des échéances réglementaires, garantissant la conformité grâce à un échéancier qui envoie et reçoit des alertes automatiques chaque fois qu’une échéance approche. Les listes de contrôle interactives, accessibles via l’application mobile de la GMAO, offrent une aide concrète aux techniciens sur le terrain. Ils peuvent suivre les activités planifiées de manière plus rapide et sécurisée, en cochant les tâches complétées directement à partir de l’ordre de travail programmé. Cette approche garantit que toutes les opérations sont exécutées correctement et que les données sont disponibles dans le rapport de fin de travail.
L’introduction de l’intelligence artificielle dans la GMAO permet de générer des plans de maintenance complets, basés sur les normes et réglementations du système QHSE en vigueur au niveau mondial. L’IA permet de définir la fréquence des activités et de créer des listes de contrôle pour les inspections et les maintenances, garantissant des interventions rapides et sécurisées. De plus, l’IA fonctionne comme un assistant numérique, en analysant les données et les tendances enregistrées sur la plateforme. Cela permet de recevoir des conseils et des suggestions instantanés sur les activités et les ordres de travail, y compris des propositions d’affectation au personnel et aux fournisseurs, pour une planification plus efficace. Le Smart Assistant permet également de surveiller la performance des équipements et des équipes, envoyant des alertes en cas de déviations par rapport aux performances attendues.
Maintenance prédictive
La maintenance prédictive représente une approche avancée de la gestion des équipements, basée sur l’utilisation de données avancées et de technologies innovantes pour surveiller les conditions des équipements et prédire les pannes imminentes. Cette méthode se distingue des formes traditionnelles de maintenance par sa capacité à anticiper les problèmes avant que des pannes critiques ne surviennent, réduisant ainsi au minimum les temps d’arrêt non planifiés et optimisant l’efficacité opérationnelle
Pour mettre en œuvre la maintenance prédictive, l’utilisation de capteurs et de dispositifs IoT est fondamentale pour recueillir en temps réel des données sur les vibrations, la température, la pression, la consommation d’énergie et d’autres paramètres critiques. Ces données sont ensuite analysées à l’aide de logiciels avancés qui appliquent des modèles statistiques et des techniques d’intelligence artificielle pour identifier les schémas et les anomalies dans les performances des équipements. Sur la base de ces analyses, des modèles prédictifs sont développés pour prévoir quand des pannes pourraient survenir ou quand des interventions de maintenance seront nécessaires.
Bien que la maintenance prédictive implique des coûts élevés de mise en œuvre et nécessite du personnel qualifié, les avantages qu’elle peut apporter aux entreprises sont nombreux : réduction des coûts de maintenance et de remplacement, amélioration de la productivité grâce à une planification plus précise et réduction des interruptions de production, amélioration de la sécurité sur le lieu de travail et réduction des pannes soudaines des équipements. Cela la rend particulièrement adaptée aux équipements critiques et complexes où les coûts élevés de temps d’arrêt doivent être minimisés. Pour les équipements moins critiques ou plus simples, d’autres formes de maintenance préventive peuvent être plus économiques et suffisantes.
Comparée à d’autres formes de maintenance telles que la maintenance préventive basée sur des calendriers ou la maintenance conditionnelle basée sur des paramètres mesurables, la maintenance prédictive se distingue par sa capacité à anticiper les pannes en se basant sur les données réelles de fonctionnement des équipements plutôt que sur des intervalles de temps ou des signaux de déviation.
Avantages de la maintenance Prédictive
- Optimisation des interventions: Interventions basées sur des données précises, réduisant les coûts et maximisant l’efficacité.
- Prévention des pannes majeures: Surveillance continue permet de détecter les signes précurseurs de défaillance, évitant les pannes graves.
Désavantages de la maintenance Prédictive
- Investissement initial élevé: Mise en place de capteurs et de systèmes d’analyse de données peut être coûteuse.
- Complexité de gestion: Nécessite des compétences spécialisées pour l’analyse des données et l’interprétation des résultats.
Maintenance Systématique (ou Périodique)
La maintenance systématique (ou Périodique) fait partie de la famille de la maintenance programmée ou planifiée car elle est effectuée à intervalles réguliers, également appelée maintenance périodique. Les activités de maintenance sont effectuées régulièrement en fonction de calendriers spécifiques, d’heures de fonctionnement des équipements, de cycles de production ou d’autres paramètres temporels définis.
Cette approche vise à prévenir les pannes imprévues et à maintenir l’équipement dans un état optimal en effectuant régulièrement des contrôles, des lubrifications, des ajustements et le remplacement des pièces d’usure.
La maintenance systématique est essentielle pour assurer la continuité opérationnelle et la sécurité sur le lieu de travail, tout en réduisant les risques associés aux arrêts imprévus et aux coûts de réparation élevée. Cette approche planifiée assure la fiabilité et la durabilité des actifs, en prévenant les défaillances potentielles grâce à des interventions régulières et structurées.
Avantages de la maintenance Systématique
- Facilité de planification: Les intervalles de maintenance fixes permettent une gestion facile et prévisible des ressources.
- Réduction des risques de panne: Programme de maintenance régulier réduit les risques de défaillance inattendue.
Désavantages de la maintenance Systématique
- Coûts élevés: Peut entraîner des coûts élevés si les interventions sont trop fréquentes par rapport aux besoins réels.
- Surmaintenance: Interventions planifiées peuvent conduire à remplacer des pièces encore en bon état, gaspillant ainsi des ressources.
Maintenance Conditionnelle (ou Condition-based Maintenance)
La maintenance conditionnelle est une stratégie de maintenance préventive basée sur la surveillance continue ou périodique de l’état des équipements. Elle n’est effectuée que lorsque les données de surveillance indiquent qu’une intervention est nécessaire, ce qui permet d’optimiser les ressources et les interventions.
Pour mettre en œuvre la maintenance conditionnelle, des capteurs doivent être installés sur l’équipement à surveiller. Ces capteurs émettent un signal lorsque des paramètres définis (une condition spécifique, en fait) tels que la température, les vibrations et l’usure des composants sont atteints. Les données enregistrées et envoyées en temps réel sont ensuite analysées par la GMAO, qui est alors en mesure de signaler la nécessité d’une intervention, en générant une alarme ou en créant un ordre de travail, par exemple, pour automatiser la maintenance.
La mise en œuvre d’une stratégie de maintenance conditionnelle permet des interventions précises et nécessaires, prolongeant ainsi la durée de vie des équipements et réduisant les coûts de maintenance. Elle minimise également les temps d’arrêt imprévus, améliorant ainsi l’efficacité opérationnelle.
La maintenance conditionnelle peut ne pas être rentable pour les équipements moins critiques, pour lesquels le coût des capteurs et des systèmes de surveillance est supérieur aux avantages. En outre, sa mise en œuvre nécessite une infrastructure sophistiquée de surveillance et d’analyse des données, qui peut être complexe et coûteuse à installer et à gérer.
Avantages de la maintenance Conditionnelle
- Optimisation des opérations
- Prolongation de la durée de vie des composants
Désavantages de la maintenance Conditionnelle
- Coût initial élevé
- Complexité de la gestion
Maintenance Programmée (ou Planifiée)
La maintenance programmée se concentre sur la planification des activités de maintenance en fonction de prévisions temporelles, de cycles de maintenance prédéfinis ou d’indicateurs d’usure. Ce type de maintenance implique la réalisation périodique d’interventions préventives telles que des contrôles réguliers, des inspections détaillées et le remplacement préventif de composants critiques. L’objectif est de maintenir les équipements dans des conditions de fonctionnement optimales afin de prolonger leur durée de vie et d’éviter des pannes coûteuses. La maintenance Programmée, ou Maintenance Planifiée, s’appuie sur les expériences passées, les recommandations du fabricant et les meilleures pratiques industrielles pour déterminer la fréquence et le type d’interventions de maintenance nécessaires.
Pour mettre en œuvre la maintenance programmée, il est essentiel d’élaborer un plan de maintenance définissant les actions à entreprendre, telles que l’inspection, la lubrification, le remplacement des pièces usées et d’autres activités préventives. Ces interventions sont programmées avant que les équipements ne montrent des signes de défaillance, ce qui réduit au minimum les pannes soudaines et les temps d’arrêt non planifiés.
Pour cela, des outils de surveillance de base sont nécessaires, tels que des programmes de maintenance, des listes de contrôle et des instruments de mesure pour surveiller des paramètres critiques tels que la pression, la température et les niveaux de fluides.
La maintenance prédictive peut ne pas être nécessaire pour les équipements non critiques ou essentiels à la production, lorsque les coûts associés à la mise en œuvre d’un plan de maintenance régulier dépassent les bénéfices potentiels. Par exemple, pour les équipements de faible valeur ou à durée de vie courte, d’autres stratégies de maintenance moins intensives peuvent être plus appropriées.
Avantages de la maintenance Programmée
- Réduction des pannes
- Optimisation des coûts
Désavantages de la maintenance Programmée
- Coûts initiaux et organisationnels élevés
- Risque de surmaintenance
Différences avec les types de maintenance préventive
La maintenance prédictive se distingue des autres formes de maintenance préventive principalement par son approche basée sur les données et sa capacité à prédire les pannes futures plutôt que de se fier à des programmes temporels ou à des cycles prédéfinis.
Voici les principales différences :
- Maintenance Prévisionnelle
Elle est basée sur des calendriers ou des comptages d’heures de fonctionnement pour effectuer des interventions de maintenance préventive, indépendamment des conditions réelles des équipements. - Maintenance Conditionnelle
Elle utilise des paramètres mesurables (comme les vibrations, la température, la pression) pour décider de l’intervention de maintenance uniquement lorsque ces paramètres atteignent ou dépassent les limites critiques ou montrent des écarts significatifs.
Maintenance Améliorative
La maintenance améliorative, également connue sous le nom de maintenance proactive, se distingue par son intention d’améliorer les conditions de fonctionnement des actifs sans attendre l’apparition de pannes ou de dysfonctionnements. Contrairement à la maintenance corrective, qui réagit à une panne déjà survenue, la maintenance améliorative prévoit des interventions visant à optimiser et à mettre à jour les capacités et les performances des installations. Cette stratégie vise non seulement à éviter les arrêts coûteux, mais aspire également à renforcer l’efficacité opérationnelle et la sécurité.
Avantages de la maintenance Améliorative
- Amélioration continue des performances et de la sécurité des installations.
- Réduction du risque de pannes imprévues et d’arrêts, améliorant ainsi la productivité globale.
Désavantages de la maintenance Améliorative
- Coûts initiaux élevés pour les investissements dans les mises à jour et les technologies avancées.
- Besoin d’une planification détaillée et de compétences spécialisées pour une mise en œuvre efficace des changements.
Maintenance Évolutive
La maintenance évolutive est une approche proactive qui vise à adapter continuellement les équipements et systèmes aux nouvelles exigences technologiques et opérationnelles. Contrairement à la maintenance corrective, axée sur la réparation des pannes, et à la maintenance préventive, visant à éviter les défaillances, la maintenance évolutive se concentre sur l’amélioration et la modernisation des actifs pour répondre aux besoins changeants de l’entreprise. Cela peut inclure l’ajout de nouvelles fonctionnalités, l’optimisation des performances, et la mise à jour des systèmes pour rester conformes aux normes réglementaires et aux attentes du marché.
Grâce à la maintenance évolutive, les entreprises peuvent prolonger la durée de vie de leurs actifs, améliorer leur efficacité opérationnelle et maintenir leur compétitivité face aux avancées technologiques rapides. En investissant dans cette forme de maintenance, les entreprises s’assurent que leurs systèmes et équipements restent alignés avec leurs objectifs stratégiques et peuvent s’adapter rapidement aux nouvelles opportunités et défis du marché.
Avantages de la Maintenance Évolutive
- Adaptation continue : Les systèmes et équipements sont constamment mis à jour pour répondre aux nouvelles exigences.
- Amélioration des performances : Optimisation des actifs pour une meilleure efficacité opérationnelle.
Désavantages de la Maintenance Évolutive
- Coûts initiaux élevés : Les mises à jour et améliorations peuvent nécessiter des investissements significatifs.
- Complexité de gestion : Nécessite une planification et une coordination minutieuses pour minimiser les interruptions.
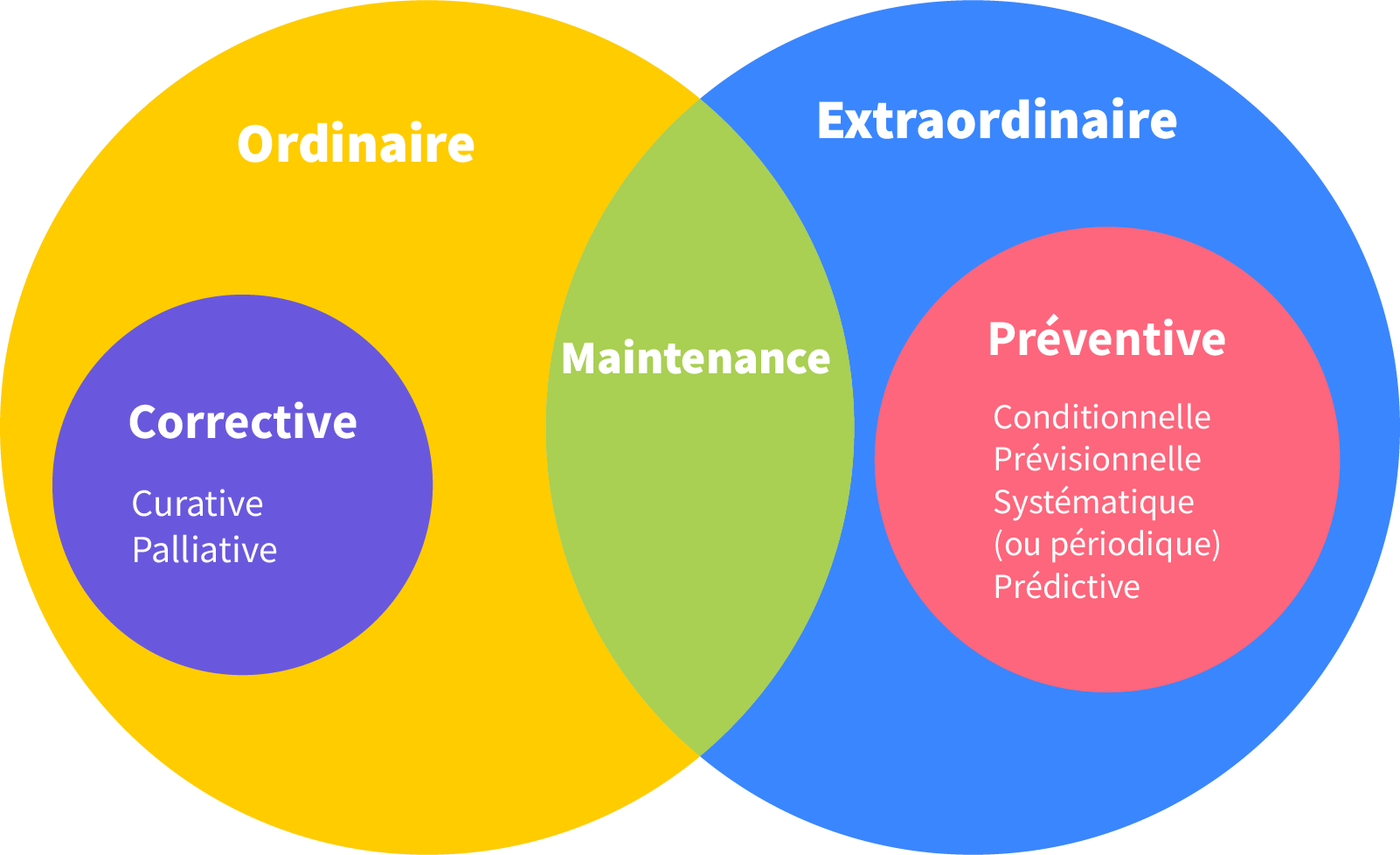
Les différences entre les principaux types de maintenance :
- La maintenance préventive se concentre sur l’exécution d’interventions programmées pour prévenir les pannes futures et maintenir les équipements en conditions optimales.
- Elle est basée sur des contrôles réguliers, le remplacement préventif de composants et des interventions planifiées en fonction de critères tels que les heures de fonctionnement, les calendriers ou les recommandations du fabricant.
- Son objectif est de réduire le risque de pannes soudaines et de minimiser les temps d’arrêt non planifiés.
- La maintenance curative intervient uniquement après qu’une panne ou un dysfonctionnement des équipements s’est produit.
- Ce type de maintenance est réactif et est déclenché lorsque les équipements ne fonctionnent pas correctement ou sont complètement arrêtés.
- Son objectif est de rétablir rapidement les équipements à pleine capacité pour reprendre la production ou les opérations.
- La maintenance systématique repose sur des plans et des procédures préétablis pour effectuer la maintenance à des intervalles réguliers.
- Ce type de maintenance est planifié en fonction de calendriers, d’heures de fonctionnement, de cycles de production ou d’autres métriques préétablies.
- Son objectif est de prévenir les pannes imprévues en maintenant les équipements dans des conditions optimales grâce à des contrôles réguliers et des interventions préventives.
- La maintenance prédictive utilise des technologies avancées comme des capteurs, le suivi continu des conditions et l’analyse des données pour prédire les pannes imminentes.
- Elle se concentre sur l’identification d’anomalies et de signes précoces de détérioration à travers l’analyse des données historiques et l’application de techniques d’intelligence artificielle.
- Son objectif est d’intervenir avant qu’une panne ne survienne, minimisant ainsi les temps d’arrêt non planifiés et optimisant l’efficacité des équipements.
La maintenance prévisionnelle utilise des prévisions basées sur des modèles historiques, des analyses de données et des tendances pour anticiper le moment où une intervention sera nécessaire. Elle se situe à mi-chemin entre la maintenance préventive (basée sur des calendriers fixes ou des cycles prédéterminés) et la maintenance prédictive, car elle intègre l’analyse des données, sans nécessairement s’appuyer sur des données en temps réel, mais en utilisant tout de même des capteurs avancés.
La maintenance prévisionnelle peut donc être définie comme une sorte d’évolution de la maintenance prédictive, c’est-à-dire une approche qui combine des modèles de prédiction et de planification pour éviter les pannes et optimiser les ressources, en utilisant également les outils avancés de la maintenance prédictive pour effectuer ses analyses.
- La maintenance conditionnelle repose sur l’utilisation de paramètres mesurables comme les vibrations, la température, la pression, l’électricité, etc., pour décider de la nécessité d’effectuer la maintenance.
- Elle utilise les signaux provenant des équipements pour déterminer leur état de santé et décider de l’intervention de maintenance en fonction des limites critiques ou des écarts par rapport aux conditions normales.
- Cette approche permet d’effectuer la maintenance uniquement lorsque nécessaire, améliorant ainsi l’efficacité et réduisant les coûts par rapport à la maintenance préventive basée sur un calendrier.
- La maintenance améliorative se concentre sur l’amélioration des performances, de l’efficacité ou de la durabilité des équipements au-delà des niveaux de base.
- Ce type de maintenance peut inclure des mises à niveau technologiques, des modifications de conception ou des optimisations pour obtenir de meilleurs résultats opérationnels ou économiques.
- Son objectif est d’accroître la productivité, de réduire les coûts opérationnels ou d’améliorer la sécurité et la fiabilité des équipements.
GMAO, l’outil qui vous aide à choisir le type de maintenance à adopter
En analysant les différents types de maintenance, nous avons compris que chaque stratégie a ses avantages et ses inconvénients, et qu’il n’existe pas de stratégie de maintenance universellement meilleure que les autres. Le choix du type de stratégie de maintenance à adopter dépend de nombreux facteurs, tels que la typologie des actifs, leur coût, les coûts de maintenance et de pièces de rechange, les objectifs de l’entreprise, la disponibilité des ressources et bien d’autres encore. Alors, comment choisir le type de maintenance le plus adapté à notre entreprise ?
Pour savoir si la voie que nous empruntons est la bonne et conforme aux objectifs que nous nous sommes fixés, la première chose à faire est de surveiller et d’analyser les données et les résultats obtenus grâce à la stratégie que nous utilisons. Pour ce faire, et pour éviter la confusion, il est bon de s’appuyer sur les systèmes de gestion de la maintenance assistée par ordinateur (GMAO ou CMMS) pour soutenir ces décisions.
Les entreprises se tournent vers les systèmes de Gestion de la Maintenance Assistée par Ordinateur (GMAO), connus également sous le nom de Computerized Maintenance Management Systems (CMMS) en anglais. La GMAO permet de planifier, suivre et optimiser toutes les activités de maintenance avec une précision et une efficacité accrue. En automatisant la planification des maintenances préventives et prédictives, en suivant l’historique des interventions pour chaque équipement, en optimisant l’utilisation des ressources et des pièces de rechange, et en analysant les données pour améliorer les processus de maintenance, les entreprises peuvent non seulement améliorer leur fiabilité opérationnelle mais aussi renforcer leur sécurité industrielle.
Comment choisir le type de maintenance à adopter
Le choix de la stratégie de maintenance dépend de nombreux facteurs, tels que la typologie des actifs, leur coût, les coûts de maintenance et de pièces de rechange, les objectifs de l’entreprise et la disponibilité des ressources. Une analyse précise des actifs est la première étape pour identifier l’importance, le coût et le cycle de vie de chaque composant. Il est essentiel de recueillir et d’analyser les données historiques des pannes et des maintenances pour identifier les tendances et les points critiques, ce qui permet de prendre des décisions éclairées sur les stratégies à adopter.
La disponibilité des ressources, qu’elles soient humaines ou financières, joue un rôle crucial dans le choix de la maintenance. Les ressources limitées peuvent orienter vers des stratégies moins intensives en ressources, comme la maintenance conditionnelle. Les objectifs de l’entreprise en termes de fiabilité et de disponibilité influencent fortement le choix de la stratégie, en poussant vers la maintenance préventive et prédictive dans les secteurs où l’interruption de service a des impacts significatifs. De plus, il est fondamental d’évaluer les technologies de surveillance et d’analyse disponibles et comment elles peuvent être intégrées dans les processus de maintenance pour optimiser l’efficacité.
- Évaluation des Actifs : Analyser l’importance, le coût et le cycle de vie des actifs.
- Analyse des Données : Utiliser les données historiques des pannes et des maintenances pour identifier les tendances et les points critiques.
- Ressources Disponibles : Prendre en compte les ressources humaines et financières disponibles pour la maintenance.
- Objectifs de Fiabilité : Définir les objectifs de fiabilité et de disponibilité requis par l’entreprise.
- Technologies Disponibles : Évaluer les technologies de surveillance et d’analyse disponibles et leur intégration dans les processus de maintenance.
Rôle du GMAO
Un CMMS (Computerized Maintenance Management System) ou GMAO (Gestion de la Maintenance Assistée par Ordinateur) est un outil essentiel pour gérer et optimiser les activités de maintenance. Voici comment un CMMS, grâce à ses fonctionnalités, peut soutenir le choix et l’implémentation des stratégies de maintenance :
- Gestion des Actifs : Suivre l’historique des actifs, surveiller les conditions et planifier les interventions.
- Planification et Programmation : Automatiser la planification de la maintenance préventive et systématique.
- Analyse des Données : Fournir des analyses détaillées et des rapports pour soutenir des décisions basées sur les données.
- Surveillance en Temps Réel : Intégrer des capteurs et des technologies IoT pour la surveillance des conditions et la maintenance prédictive.
- Optimisation des Ressources : Gérer efficacement le personnel, les pièces de rechange et les ressources financières.
Types de maintenance par secteur
Comme nous l’avons mentionné au début, un type de maintenance n’est pas meilleur qu’un autre si l’on ne prend pas en compte le contexte et les résultats obtenus. Cependant, nous pouvons décrire une tendance des principaux secteurs à utiliser des stratégies de maintenance spécifiques, car elles sont plus alignées avec leurs objectifs et donc plus facilement applicables. Voici quelques exemples :
Gestion de Flotte : Privilégie la maintenance conditionnelle pour surveiller l’état des véhicules et intervenir en fonction des données collectées (par exemple, niveaux d’huile, pression des pneus, kilométrage, etc.). Dans ce secteur où la disponibilité des actifs (les véhicules) est d’une importance fondamentale et où il est facile de collecter des données (par exemple, le kilométrage parcouru ou les niveaux d’huile) grâce à l’utilisation de capteurs de base, la maintenance basée sur les conditions est celle qui donne les meilleurs résultats.
Industrie/Manufacture : Utilise principalement la maintenance préventive et prédictive pour garantir la continuité opérationnelle et réduire les temps d’arrêt imprévus. Dans l’industrie de la production, il est en effet courant de trouver des dispositifs interconnectés, par exemple avec des systèmes MES, SCADA ou IoT, qui assurent une efficacité opérationnelle maximale. Ceci est également dû à l’avènement de l’industrie 4.0 où les capteurs et les dispositifs IoT sont largement utilisés, surtout sur les installations de production de dernière génération.
Gestion des Installations : S’oriente vers la maintenance programmée ou à la demande, gérant des interventions régulières pour les bâtiments et les infrastructures, et des réparations réactives pour les pannes imprévues. Par exemple, dans une chaîne de magasins où sont présents des systèmes anti-incendie, des systèmes HVAC ou des installations de sécurité qui nécessitent des mises à jour, des inspections et des contrôles récurrents, il est facile de comprendre pourquoi la maintenance programmée est le type de maintenance le plus utilisé. De même, la maintenance à la demande pour les actifs moins critiques (par exemple, les ampoules) peut être une stratégie ayant un impact moindre en termes de temps et de coûts pour le personnel de maintenance, si elle est gérée, par exemple, grâce à la signalisation par ticketing directement par le personnel présent dans le bâtiment.
Rejoindre les experts
Ou découvrez le mainim GMAO avec la playlist vidéo.