Maintenance Préventive
Dans le domaine de la maintenance, les activités peuvent être regroupées en deux grandes catégories : d’une part, nous avons les activités de maintenance réactive, qui ne sont effectuées qu’après une panne avérée, entraînant un arrêt inévitable de la machine ou de la production ; d’autre part, il existe des types d’activités de maintenance planifiées et programmées, qui suivent des cycles temporels spécifiques ou l’état des actifs.
Dans cet article, nous allons donner une définition de la maintenance préventive et des types de maintenance qui en font partie, définir comment établir un plan de maintenance préventive, et découvrir pourquoi la maintenance préventive est l’un des types de maintenance les plus utiles et utilisés dans le domaine industriel.
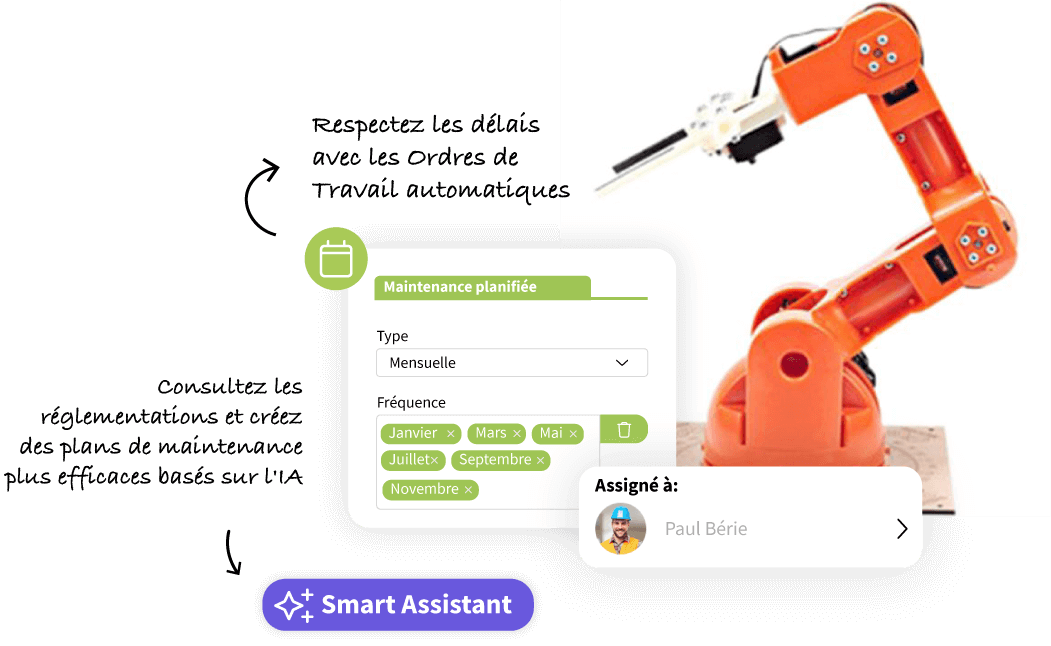
Qu’est-ce que la maintenance préventive ?
Lorsqu’on parle de maintenance préventive, on pense souvent à tort qu’il s’agit d’un seul type de maintenance, mais ce n’est pas le cas.
La maintenance préventive, contrairement à la maintenance corrective, est le type de maintenance qui, dans certains cas, ne dépend pas de l’état de l’actif et qui est décidée par l’homme.
Elle englobe un large éventail d’activités et de stratégies de maintenance visant à ne pas attendre qu’une panne se produise, mais à la prévoir et à l’éviter grâce à des interventions régulières ou à des critères prédéfinis.
Cela permet de réduire le risque de dysfonctionnement et d’interruption imprévue de la production, limitant ainsi le nombre et la fréquence des pannes et des interventions.
La maintenance préventive repose non seulement sur l’exécution de tâches planifiées pour éviter des pannes, mais également sur le suivi constant des performances des équipements. En effet, l’efficacité de cette stratégie est directement liée à l’utilisation d’indicateurs de maintenance qui permettent d’évaluer l’état des actifs et d’ajuster les interventions en conséquence. Grâce à une analyse précise de ces indicateurs, il est possible d’optimiser les opérations de maintenance tout en réduisant les temps d’arrêt et les coûts inutiles.
Dans cet article, nous examinerons en détail tous les aspects de la maintenance préventive. Si vous souhaitez un résumé rapide de l’article, vous pouvez regarder la vidéo ci-dessous, dans laquelle nous avons résumé les principaux points pour une vue d’ensemble complète de la maintenance préventive, ou lisez la suite !
Définition de la maintenance préventive
La définition de la maintenance en général indique que, par maintenance, on entend la combinaison de toutes les actions techniques et administratives ainsi que la mise en œuvre de méthodes et de ressources spécifiques, visant à maintenir en état de fonctionnement les installations et les machines afin de garantir, dans le temps, des processus de production en quantité, qualité, fiabilité et sécurité.
Il n’est donc pas surprenant que la maintenance préventive soit l’un des types de maintenance les plus importants et les plus utilisés, surtout dans le domaine industriel.
Objectifs de la maintenance préventive
Le but principal de la maintenance préventive est d’étendre le cycle de vie des actifs et de limiter les arrêts de machines ou, plus généralement, les autres actions de maintenance corrective, afin de prévenir une dégradation excessive de la production, tant en termes de qualité que de quantité.
Cet objectif est atteint grâce à des inspections périodiques ou basées sur des métriques spécifiques choisies par le mainteneur, de sorte que des interventions de prévention nécessaires mais non encore apparentes puissent être effectuées avant que l’usure excessive ou la panne ne soit constatée.
Ce type de maintenance comprend des opérations telles que le nettoyage, la lubrification et le remplacement de composants d’une installation ou d’un actif.
On peut donc résumer ainsi les buts de la maintenance préventive :
- Réduire la fréquence des interruptions de la production ;
- Réduire les temps d’arrêt des machines pour les réparations ;
- Augmenter la durée de vie des machines et des équipements ;
- Planifier les interventions de maintenance corrective pour les exécuter dans les meilleures conditions ;
- Mieux gérer les stocks de pièces de rechange ;
- Réduire le budget de maintenance ;
- Améliorer les conditions de travail du personnel ;
- Limiter ou même éliminer les causes des accidents graves.
Types de maintenance préventive
Les types les plus courants de maintenance préventive sont les suivants :
- Maintenance préventive conditionnelle : Maintenance préventive basée sur les conditions, effectuée en fonction d’un indicateur d’utilisation spécifique ou d’un seuil d’utilisation activant une demande de maintenance.
- Maintenance préventive systematique: Maintenance préventive basée sur le temps, effectuée selon un calendrier spécifique.
- Maintenance préventive prédictive : Une méthode plus avancée de maintenance qui utilise les lectures des compteurs et les données d’utilisation pour prédire quand les équipements ou les biens nécessiteront une maintenance.
- Maintenance Prévisionnelle: Un type de maintenance préventive plus avancé technologiquement qui s’appuie sur des données historiques pour identifier les schémas d’usure et de défaillance.
- Maintenance axée sur la fiabilité : Un processus de maintenance axé sur la planification pour assurer que les activités de maintenance sont efficaces, sûres et fiables.
Maintenance Préventive Conditionnelle ou Condition-based Maintenance
La maintenance préventive conditionnelle, également connue sous sa variante anglaise « Condition-based maintenance », est un type de maintenance qui est effectuée lorsque l’état d’un actif atteint des conditions spécifiques prédéfinies. L’actif est surveillé à l’aide de compteurs et de capteurs qui enregistrent en temps réel les métriques relatives à son état, lesquelles sont ensuite intégrées dans le système de gestion de la maintenance (GMAO). Une fois que les seuils définis dans le CMMS sont atteints, la maintenance conditionnelle peut être automatisée, générant ainsi automatiquement un ordre de travail.
L’utilisation de ce type de maintenance permet de surveiller en permanence l’usure de l’actif et d’éviter les maintenances superflues qui ne feraient qu’augmenter les coûts de maintenance, ou de regrouper plusieurs interventions utiles lors des activités de maintenance, réduisant ainsi les temps d’arrêt et la fréquence des pannes.
Exemple de maintenance basée sur les conditions
Un exemple courant de maintenance conditionnelle peut être trouvé dans l’entretien des véhicules : le changement des pneus ou la vidange d’huile sont des exemples classiques de maintenance conditionnelle, car leur contrôle est basé sur le kilométrage et l’état actuel de l’actif. En résumé, la maintenance conditionnelle est effectuée uniquement lorsque l’état d’un actif atteint certaines conditions, définies à l’avance par l’organisation ou l’équipe de maintenance.
Contenu de l'article
- Maintenance Préventive
- Qu’est-ce que la maintenance préventive ?
- Définition de la maintenance préventive
- Objectifs de la maintenance préventive
- Types de maintenance préventive
- Maintenance préventive conditionnelle ou Condition-based maintenance
- Exemple de maintenance basée sur les conditions
- Maintenance Préventive Systématique
- Exemple de maintenance Systématique
- Maintenance Préventive Prédictive
- Exemple de Maintenance Prédictive
- Maintenance centrée sur la Fiabilité (Reliability-Centered Maintenance)
- Différence entre maintenance préventive et systématique (programmée)
- Différence entre maintenance préventive et corrective
- Avantages de la maintenance préventive
- Les inconvénients de la maintenance préventive
- Pourquoi faire de la maintenance préventive ?
- Comment planifier la maintenance préventive
- Comment automatiser la maintenance préventive avec la GMAO
Découvrez la GMAO mainsim en direct.
Réservez une démonstration pour découvrir comment fonctionne la GMAO grâce à une démonstration personnalisée.
Maintenance Préventive Systématique
La maintenance préventive systématique (ou maintenance périodique) est un type de maintenance basé sur des cycles d’utilisation prédéterminés. Cette forme de maintenance est programmée selon un calendrier établi dans un plan de maintenance temporel. Contrairement à la maintenance conditionnelle, qui dépend de l’état de l’équipement, la maintenance systématique se concentre sur le temps d’utilisation d’une machine ou d’un équipement, le nombre de cycles ou la distance parcourue.
En résumé, il n’y a pas de grandes différences entre la maintenance préventive systématique et la maintenance programmée, car toutes deux sont basées sur des interventions planifiées en fonction du temps, contrairement à la maintenance conditionnelle qui est déclenchée par l’état de l’actif.
Cependant, la maintenance systématique peut engendrer des coûts élevés à long terme. En raison de son calendrier fixe, elle peut parfois être superflue, entraînant des interruptions non nécessaires et une utilisation inefficace des ressources techniques. Si elle n’est pas bien ajustée, cette approche peut gaspiller du temps et des ressources en ne répondant pas aux besoins réels de l’équipement.
Exemple de maintenance programmée
Un exemple simple mais efficace est celui des extincteurs dans une installation, qui doivent être inspectés à intervalles réguliers pour se conformer aux exigences légales. Le remplacement de la courroie de moteur d’un véhicule en est un autre exemple, où une condition spécifique (le kilométrage) est utilisée pour anticiper une défaillance potentielle.
Maintenance Préventive Prédictive
La maintenance prédictive est le dernier arrivé chronologiquement, développé en conséquence des progrès technologiques réalisés ces dernières années. Il s’agit d’un type particulier de maintenance préventive qui intervient après l’identification et la mesure d’un ou plusieurs paramètres à l’aide de capteurs appliqués aux équipements ou aux installations. En utilisant le traitement de ces paramètres et des données acquises, un logiciel de GMAO est capable de construire des modèles appropriés pour prédire le temps écoulé entre la mesure et l’occurrence d’une panne.
Parmi tous les types de maintenance, la maintenance prédictive est considérée comme la plus sophistiquée mais nécessite également un effort considérable pour son implémentation. Il est important de noter que l’introduction d’une stratégie de maintenance prédictive est particulièrement adaptée (en termes de résultats, d’effort et de types d’actifs) pour les entreprises et les secteurs fortement industriels, visant à maximiser l’efficacité et à gérer des actifs critiques, coûteux et sensibles.
Exemple de Maintenance Prédictive
Un exemple courant d’utilisation de la maintenance prédictive se trouve dans le secteur manufacturier, notamment dans l’industrie automobile. Dans ce contexte, des équipements critiques de la chaîne de production, tels que les robots de soudage et les machines-outils CNC, sont équipés de capteurs qui surveillent en temps réel des paramètres opérationnels tels que les vibrations et la température. Les données collectées sont analysées par un logiciel utilisant des algorithmes d’apprentissage automatique pour détecter les anomalies indiquant des défaillances potentielles futures. Lorsqu’un problème est identifié, les techniciens de maintenance sont alertés et peuvent intervenir avant qu’une panne ne se produise, en remplaçant par exemple des roulements usés dans les robots de soudage.
Maintenance centrée sur la Fiabilité (Reliability-Centered Maintenance)
La maintenance centrée sur la Fiabilité, plus communément connue sous le nom de Reliability-Centered Maintenance (RCM), est une stratégie de maintenance avancée qui, au lieu de disperser les ressources de manière indiscriminée sur tous les actifs, se concentre sur les ressources les plus critiques et leur fiabilité.
Certains actifs particulièrement critiques peuvent nécessiter un investissement pour surveiller en continu leurs performances à l’aide de technologies IoT et de stratégies de maintenance prédictive, tandis que pour d’autres, une approche basée sur la simple lecture périodique des compteurs, une stratégie basée sur les conditions ou un programme d’inspections régulières peut être plus efficace du point de vue des coûts. Pour d’autres encore, laisser simplement les choses se dérouler pourrait s’avérer être le meilleur choix.
Différence entre maintenance préventive et systématique (programmée)
Après avoir discuté des différentes politiques de maintenance préventive, il est important d’explorer la différence entre la maintenance préventive et la maintenance programmée. Souvent, tant dans le domaine académique que dans celui des entreprises, ces termes sont utilisés de manière interchangeable, en parlant de maintenance préventive programmée. Bien qu’il y ait des similitudes, il est utile de distinguer les deux.
La maintenance préventive repose sur un programme d’interventions planifiées visant à prévenir les pannes et les dysfonctionnements. Ce programme détermine quand effectuer des inspections ou des interventions directes, souvent à intervalles périodiques comme hebdomadaires, mensuels ou annuels. L’objectif est de maintenir les équipements dans des conditions optimales et de prévenir les pannes imprévues.
La maintenance programmée, quant à elle, concerne spécifiquement l’organisation temporelle des interventions. Une activité de maintenance programmée est inscrite dans un calendrier et doit être réalisée avant une date précise. Par exemple, une inspection périodique des équipements de lutte contre l’incendie devient une activité de maintenance programmée une fois planifiée et ajoutée comme ordre de travail.
Différence entre maintenance préventive et corrective
Comprendre la distinction entre la maintenance préventive et corrective est essentiel pour gérer efficacement la maintenance des équipements. Ces deux approches présentent des caractéristiques distinctives qui influencent considérablement l’efficacité opérationnelle et les coûts pour l’entreprise.
La maintenance corrective, souvent appelée maintenance réactive, intervient lorsque qu’une panne s’est déjà produite. Ce type d’intervention est nécessaire pour rétablir le fonctionnement d’une machine ou d’un composant après sa défaillance. La nature de la maintenance corrective implique que l’intervention se fait en réponse à un problème déjà survenu, causant souvent des interruptions non planifiées dans la production et des pertes économiques potentielles dues aux temps d’arrêt.
En revanche, la maintenance préventive se concentre sur l’anticipation et la prévention des pannes avant qu’elles ne se produisent. Cette approche proactive prévoit des interventions régulières, telles que des inspections et des maintenances périodiques, visant à maintenir les équipements dans des conditions optimales. L’objectif principal est de réduire le risque de pannes imprévues, de minimiser les temps d’arrêt et d’améliorer la longévité des équipements.
Un bon équilibre entre la maintenance préventive et corrective présente des avantages à court et à long terme en adoptant des pratiques plus proactives.
Les avantages de l’utilisation de la maintenance préventive par rapport à la maintenance corrective incluent :
- Coûts inférieurs
- Amélioration des biens et des équipements (moins de pannes)
- Planification anticipée de la maintenance préventive selon un calendrier contrôlable
- Les techniciens passent moins de temps lorsqu’il ne s’agit pas d’une situation d’urgence (corrective)
- Prévision des pièces de rechange nécessaires plutôt que de se retrouver potentiellement sans ou en avoir besoin soudainement.
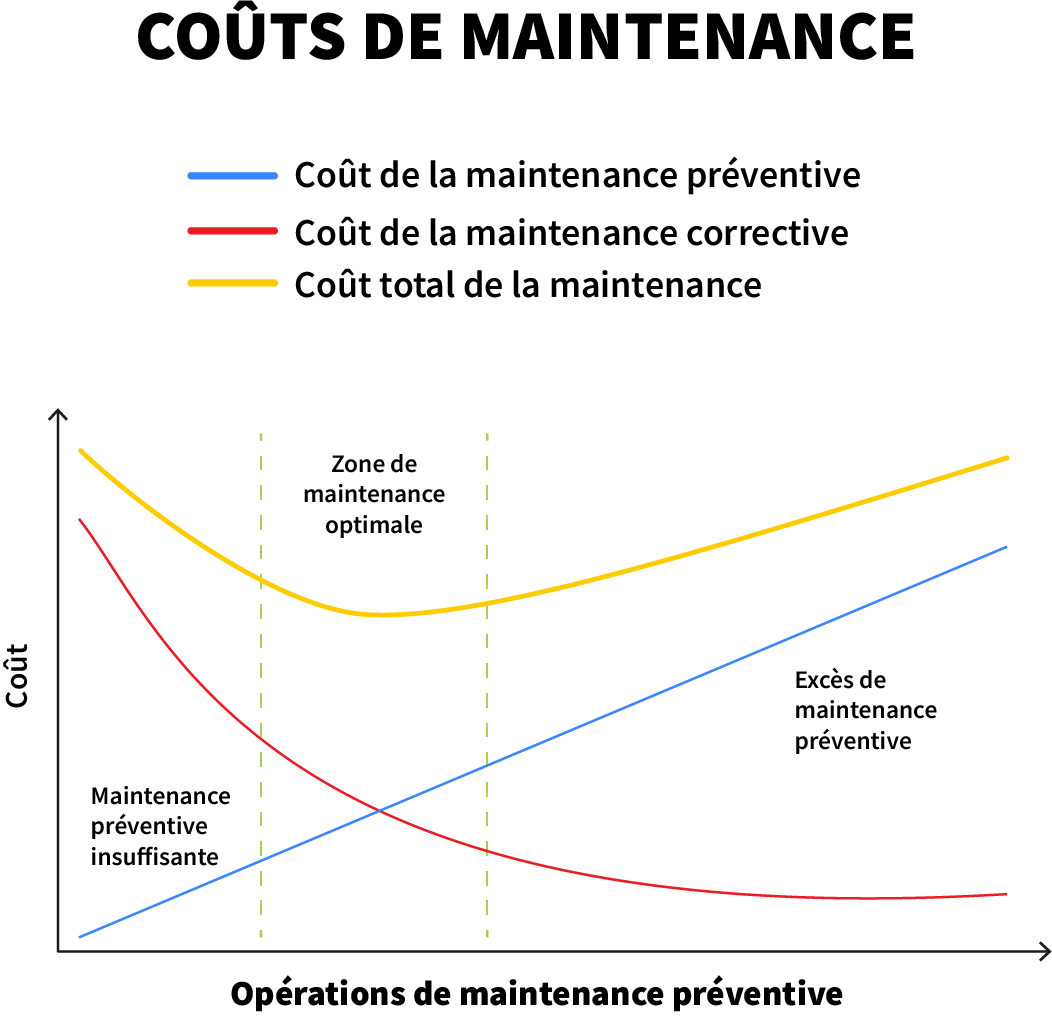
Maintenance préventive ou corrective : laquelle choisir ?
À ce stade, nous pouvons examiner avec plus de clarté quand il est préférable d’opter pour une stratégie de maintenance plutôt qu’une autre.
En général, une stratégie de type préventif est préférable à une stratégie corrective, mais ce n’est pas toujours le cas. Une politique de maintenance préventive est certainement souhaitable lorsqu’il s’agit de gérer des installations très coûteuses et complexes, où un simple composant peut entraîner des arrêts machines imprévus et compromettre la production.
Dans le domaine des installations, cette stratégie trouve également sa justification en relation avec de nombreux actifs. Pensons encore une fois au respect des normes de conformité des équipements de lutte contre l’incendie et à la nécessité de programmer ces inspections. De plus, une telle politique est fortement recommandée dans la gestion de flotte.
En revanche, lorsqu’il s’agit de gérer des actifs de faible valeur, avec des cycles de vie courts, ou des installations très simples avec des composants qui n’affectent pas leur utilisation, ou qui sont faciles et économiquement avantageux à réparer, une stratégie préventive pourrait simplement entraîner une augmentation des coûts de maintenance sans que ses avantages ne deviennent évidents et tangibles.
Pour ces raisons, la meilleure stratégie à adopter est souvent un hybride des deux, adaptant ses politiques au type d’actif concerné et les menant simultanément en parallèle.
Avantages de la maintenance préventive
La maintenance préventive est souvent perçue comme un coût additionnel difficile à justifier. Pourtant, un seul arrêt machine imprévu ou un incident évitable suffit à démontrer l’importance d’adapter ses politiques de maintenance. De plus, si elle est accompagnée de l’implémentation et de l’utilisation d’un logiciel de Gestion de la Maintenance Assistée par Ordinateur (GMAO), les résultats qui peuvent être obtenus sont véritablement remarquables.
- Accroître la productivité
La maintenance préventive (MP) non seulement garantit que les machines fonctionnent à des niveaux de performance optimaux, mais elle contribue également à augmenter la productivité. Une planification régulière de la maintenance préventive réduit la nécessité de réparations réactives ou d’urgence, permettant ainsi au personnel de maintenance de se concentrer sur les activités quotidiennes plutôt que sur les temps d’arrêt non planifiés.
Un programme de MP bien exécuté peut réduire jusqu’à 50-60 % des interventions d’urgence. Cependant, les équipes de maintenance doivent disposer des outils et des ressources nécessaires pour exécuter avec succès les plans de maintenance préventive ; ceci est rendu plus efficace grâce à des données précises sur les machines, une planification adéquate et la disponibilité des pièces de rechange appropriées.
Avec les bonnes ressources, la maintenance préventive peut aider les entreprises à atteindre le niveau de productivité souhaité.
- Minimiser les temps d’arrêt des installations
La maintenance préventive est un atout précieux pour les entreprises car elle aide à minimiser les temps d’arrêt associés aux interventions de réparation. Lorsqu’elle est effectuée régulièrement, elle contribue à réduire le risque d’inefficacités et de pannes d’équipement pouvant entraîner des interruptions coûteuses des opérations ou de la production. Cela permet aux entreprises de maximiser leurs actifs critiques et d’économiser du temps en évitant des réparations réactives et coûteuses.
De plus, la maintenance préventive prolonge la durée de vie d’une installation, en garantissant qu’elle reste dans des conditions optimales. Cela améliore non seulement les performances, mais limite également les heures de fonctionnement perdues pour le dépannage et les réparations, ce qui engendrerait des coûts supplémentaires.
- Réduction des coûts
Si vous choisissez de mettre en œuvre des programmes de maintenance préventive, vous découvrirez qu’ils peuvent entraîner des économies considérables pour les organisations en termes de réduction de divers coûts. Ces coûts comprennent les coûts de main-d’œuvre et de réparation, les coûts liés à l’indisponibilité des pièces de rechange lorsque des réparations deviennent nécessaires, ce qui entraînera une augmentation de la productivité liée à la fiabilité de l’installation ou des actifs.
Au lieu d’attendre et de faire face à une panne non planifiée, la maintenance préventive nécessite une approche proactive qui maintient les machines dans des conditions optimales, réduisant ainsi les temps d’arrêt non planifiés. En effet, un programme de maintenance préventive bien structuré peut aider les organisations à réduire les coûts opérationnels de 11 %.
- Promotion de la sécurité
La maintenance préventive est un avantage pour la sécurité des installations. Un GMAO aide à garantir que tous les actifs sont surveillés et reçoivent la maintenance nécessaire pour fonctionner au mieux, minimisant ainsi le risque d’incidents ou d’accidents dus à un dysfonctionnement des équipements.
Non seulement ils peuvent alerter les techniciens de maintenance des problèmes potentiels avant qu’ils ne se produisent, mais un bon GMAO dispose de fonctions supplémentaires intégrées telles que l’enregistrement des mesures de maintenance, les certifications du personnel et le contrôle d’accès, qui peuvent être utiles pour compléter les pratiques de vérification et assurer la conformité réglementaire, contribuant également à simplifier les audits de sécurité.
En réduisant drastiquement les conditions opérationnelles potentiellement non sécurisées, la mise en œuvre d’une MP proactive peut rendre un lieu de travail beaucoup plus sûr pour les employés et les clients.
- Augmentation de la satisfaction client
La maintenance préventive est une stratégie efficace pour toute entreprise car elle permet de maintenir le fonctionnement optimal des équipements, contribuant ainsi à accroître la satisfaction client. L’entretien régulier et les inspections des machines aident à identifier tout problème potentiel avant qu’il ne survienne, réduisant ainsi la probabilité de pannes et garantissant une ligne de production régulière.
En réduisant les retards, les désagréments pour les clients sont minimisés : un avantage inestimable lorsqu’il s’agit de maintenir la réputation d’une entreprise et la satisfaction des clients. Si l’on ajoute à cela la fiabilité et la qualité de la production, la maintenance préventive peut se révéler être un grand avantage pour les organisations à long terme.
Les inconvénients de la maintenance préventive
Bien que la maintenance préventive présente des avantages tels que la capacité à maintenir les équipements en fonctionnement constant, augmentant ainsi la productivité et l’efficacité opérationnelle, il est également important de considérer les inconvénients associés à ce type de maintenance. Le remplacement d’un composant d’un équipement basé uniquement sur une période fixe, comme c’est le cas avec la maintenance programmée, peut à long terme entraîner une augmentation globale des coûts de maintenance en raison du remplacement de composants qui pourraient encore fonctionner pendant une période prolongée.
Un autre inconvénient de la maintenance préventive réside dans sa planification même : la mise en œuvre efficace de programmes de maintenance préventive nécessite une allocation importante de temps et de ressources, ainsi qu’une planification précise pour éviter que la stratégie choisie ne soit inefficace ou même contre-productive.
Pourquoi faire de la maintenance préventive ?
Outre le fait qu’implémenter un plan de maintenance préventive peut prévenir les arrêts de production et l’augmentation conséquente des coûts, il existe d’autres avantages spécifiques à considérer :
- La maintenance préventive réduit les temps d’arrêt et les interruptions des activités dues à des pannes imprévues des équipements ;
- La maintenance préventive augmente la durée de vie des équipements, ce qui permet d’économiser de l’argent à long terme ;
- La maintenance préventive réduit considérablement les risques pour la sécurité des employés et des clients, réduisant ainsi les coûts liés aux actions légales et aux compensations des travailleurs ;
- La maintenance préventive permet d’optimiser les ressources et de gérer la charge de travail de manière plus efficace ;
- La maintenance préventive rend les équipements et installations plus fiables ;
- La maintenance préventive rend les installations et les équipements plus efficaces, assurant une production continue et un retour sur investissement élevé.
Ce ne sont là que quelques-uns des avantages spécifiques d’une maintenance préventive régulière. Il est cependant important de comprendre que l’implémentation d’un plan de maintenance préventive n’est pas toujours adaptée à toutes les situations. Décider quand et comment adopter une stratégie de maintenance préventive dépend de nombreux facteurs ; les ignorer pourrait conduire à des résultats opposés à ceux souhaités.
Comment planifier la maintenance préventive
À ce stade, nous avons compris que la maintenance s’applique à tous les équipements et machines nécessitant une certitude absolue et une continuité de service, leur bon fonctionnement étant indispensable dans la chaîne de production. Il est donc plus économique et efficace de consacrer du temps, des ressources et des pièces de rechange au remplacement des pièces qui ne sont pas encore complètement usées, plutôt que d’attendre l’apparition d’une panne pouvant causer des dommages, des pertes de production importantes et une perte économique.
Par conséquent, ce type de maintenance est accompagné d’inspections régulières capables d’identifier précisément les parties nécessitant une intervention, repérant les signes précurseurs d’une possible détérioration ou d’une diminution des performances de l’installation ou de la machine.
De même, la mesure et l’enregistrement des paramètres techniques de l’installation ou de la machine, tels que la température, la consommation énergétique, la pression, le débit, les niveaux, etc., sont des éléments fondamentaux pour le développement d’un programme sérieux de maintenance préventive. Par conséquent, il est essentiel de prévoir une phase de surveillance continue et constante des performances.
À cet égard, disposer de toute la documentation et des données que nous pouvons recueillir est crucial pour rendre nos opérations de maintenance préventive aussi efficaces que possible et réduire les risques, qu’ils soient d’ordre économique ou de sécurité.
Comment créer un plan de maintenance préventive
Pour créer et mettre en place un plan de maintenance préventive, voici les étapes à considérer :
- Identifier les objectifs et les priorités
- Identifier les équipements critiques
- Identifier les défaillances récurrentes
- Utiliser un logiciel de maintenance préventive
- Former le personnel
- Appliquer la stratégie de maintenance préventive définie
- Analyser les résultats
- Ajuster le plan de maintenance selon les besoins
Maintenant, voyons en détail comment créer et optimiser pratiquement un plan de maintenance préventive.
Comment optimiser un plan de maintenance préventive
Dans toute industrie à forte intensité de ressources, une approche préventive de la maintenance est cruciale. La prévention exige un changement culturel important, l’abandon de la mentalité consistant à « réparer uniquement en cas de défaillance », qui n’est pas viable à long terme. Commencer progressivement fait partie du processus d’amélioration continue.
La norme World Class identifie un ratio cible de maintenance préventive de 90 % et de maintenance corrective de 10 %.
La première étape de l’optimisation d’un plan de maintenance préventive consiste certainement à identifier les objectifs de l’entreprise : que voulons-nous atteindre ? Quels résultats voulons-nous obtenir ? En combien de temps ?
La deuxième étape consiste à évaluer la situation actuelle. Cela peut se faire facilement en évaluant les actifs les plus critiques, les défauts les plus fréquents et les raisons pour lesquelles ils se produisent (nous nous référons à l’AMDEC et à l’analyse des causes profondes).
L’utilisation d’un système de GMAO à ce stade est certainement très utile, car il permet de saisir les actifs critiques et de programmer la maintenance préventive (MP) sur la base du calendrier, avec des instructions de base. La visibilité et la programmation de rappels pour ces activités faciliteront les progrès. Par la suite, cette approche peut être étendue à d’autres actifs, en améliorant continuellement les instructions d’utilisation. On peut alors intégrer les pièces nécessaires à la maintenance et envisager de mettre en œuvre des plans de maintenance programmée basés sur les heures de fonctionnement ou le comptage des cycles.
La maintenance conditionnelle, qui prend en compte des variables telles que la température, les vibrations et la pression, constitue un autre pas en avant. Au fil du temps, nous pouvons passer d’une approche réactive à une approche préventive et corrective, ce qui améliore considérablement l’efficacité opérationnelle.
Une fois que nous avons créé et optimisé notre plan de maintenance préventive, le travail ne doit pas s’arrêter là : pour comprendre si les stratégies que nous avons mises en œuvre apportent réellement les résultats souhaités, nous devons procéder à une analyse des résultats, qui nous dira si les activités du plan de maintenance préventive ont un effet positif. Par exemple, nous pourrions constater qu’un bien critique, même après une maintenance planifiée, continue de tomber en panne et de provoquer des retards de production, ou que les coûts des activités planifiées (prenons l’exemple du recours à du personnel externe) consomment le budget de maintenance plus que les activités de maintenance corrective.
En bref, comme l’a dit H. James Harrington : « La mesure est la première étape qui mène au contrôle et, en fin de compte, à l’amélioration. Si vous ne pouvez pas mesurer quelque chose, vous ne pouvez pas le comprendre. Si vous ne pouvez pas le comprendre, vous ne pouvez pas le contrôler. Si vous ne pouvez pas le contrôler, vous ne pouvez pas l’améliorer ».
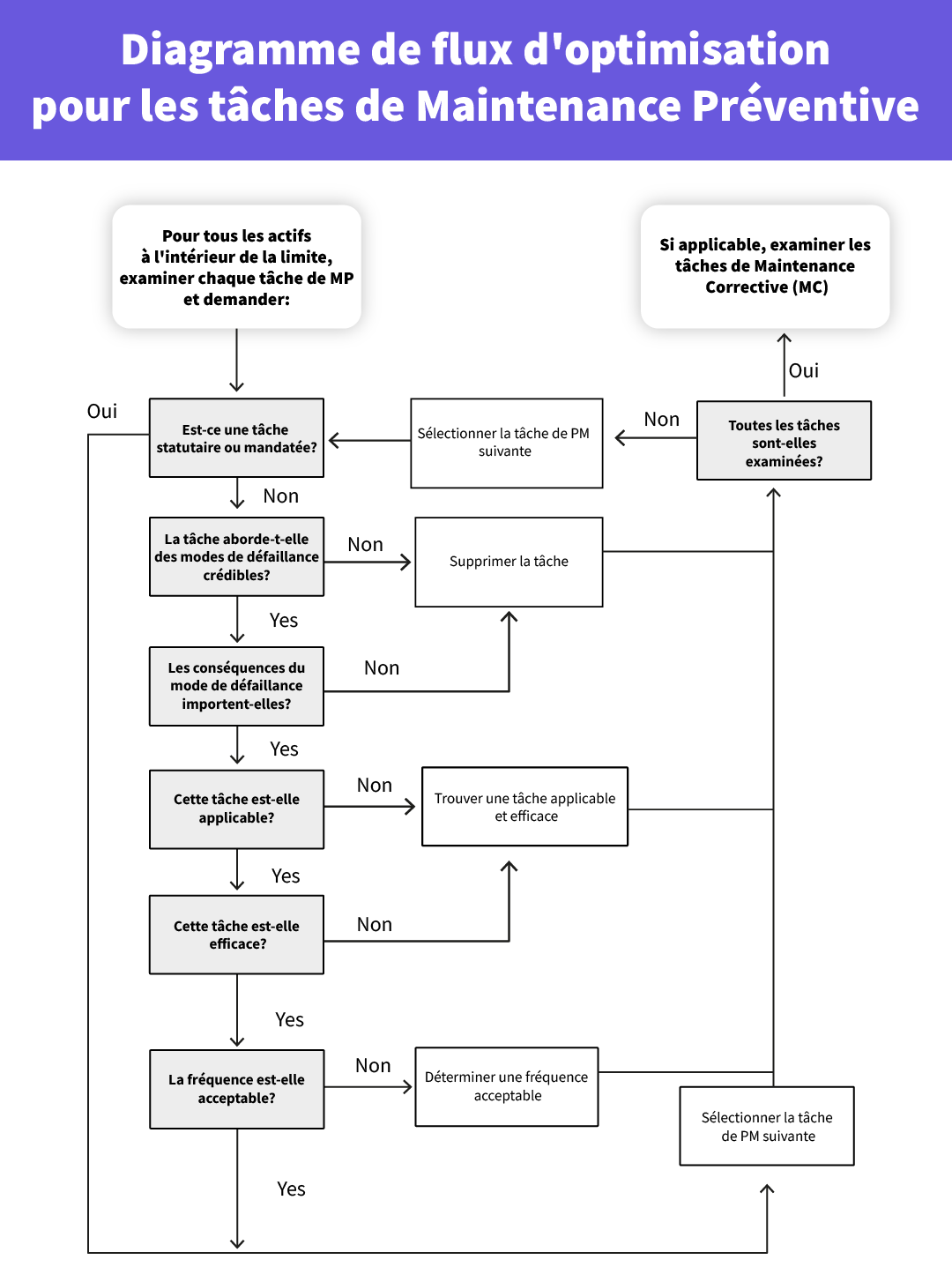
Comment automatiser la maintenance préventive avec la GMAO
Nous avons vu que la programmation et la planification de la maintenance préventive sont très délicates et que leurs résultats dépendent en grande partie de la mise en œuvre correcte des différents types de maintenance.
Pour garantir la bonne exécution des activités, qu’elles soient préventives, planifiées ou prédictives, il va de soi qu’il est nécessaire de les automatiser d’une manière ou d’une autre, afin d’éviter que l’erreur humaine ne vienne compromettre les résultats de notre plan de maintenance.
Plus le plan de maintenance préventive (MP) sera automatisé, moins l’équipe aura de temps à consacrer aux tâches pratiques et plus les gestionnaires pourront se consacrer à l’analyse des résultats.
Cet objectif (une automatisation plus importante et de meilleure qualité alimentant un plan de maintenance préventive) est réalisable avec le bon plan d’action et un logiciel de maintenance préventive comme le système de gestion des actifs de l’entreprise (EAM) ou de gestion de la maintenance assistée par ordinateur (GMAO).
En effet, ces outils permettent d’automatiser la maintenance de plusieurs manières :
- Relevés, compteurs et calendriers La GMAO est essentielle pour gérer la maintenance programmée ou conditionnelle, permettant de modéliser les activités en fonction des processus et des meilleures pratiques de l’entreprise. Une GMAO automatisée aide à planifier les activités de maintenance basées sur des relevés et des compteurs.
- Workflow Manager Cet outil permet de personnaliser les flux de travail des ordres de travail selon leur type et les processus spécifiques. Il enregistre automatiquement le temps passé à chaque étape et automatise le processus pour une traçabilité parfaite, offrant une personnalisation quasi infinie pour s’adapter aux besoins de l’entreprise.
- Ordres de travail automatiques Les ordres de travail automatiques sont générés lorsqu’une condition ou un événement spécifique se produit, souvent via l’intégration avec des systèmes MES. Cela permet à la GMAO d’ouvrir automatiquement des ordres de travail en cas de problème, assignés à l’équipe ou au fournisseur concerné.
- Planification intelligente La replanification des procédures de maintenance est facilitée par la GMAO, alignant les ressources nécessaires comme le personnel, les pièces détachées et la documentation QHSE. Cela simplifie la création d’ordres de travail complets pour chaque procédure récurrente.
- Programmes de maintenance automatisés La GMAO automatise la génération d’ordres de travail répétitifs en fonction des cycles et fréquences définis, permettant de passer à une stratégie de maintenance conditionnelle. Elle crée automatiquement des ordres de travail basés sur les conditions des actifs.
- Programmation automatique La GMAO automatise la programmation des travaux de maintenance en générant des ordres de travail selon des délais spécifiques et des fréquences prédéfinies. Le système envoie des notifications au personnel concerné, simplifiant ainsi la gestion des activités de maintenance planifiée.
- Conformité réglementaire La GMAO suit les délais spécifiques de certaines activités de maintenance et envoie des alertes automatiques à l’approche d’une échéance. Avec l’Intelligence Artificielle, il est possible de créer des plans de maintenance complets respectant les règles de sécurité et de conformité.
- Listes de contrôle interactives Les techniciens peuvent utiliser des listes de contrôle interactives sur une application mobile pour suivre les instructions nécessaires. Cela simplifie et rationalise leur travail, en signalant automatiquement les résultats des tâches et en éliminant le temps de saisie des données.
- Modèles ou Templates Les modèles permettent de gagner du temps pour la création d’ordres de travail répétitifs. Ils sont utilisés pour la maintenance extraordinaire sans délai, en permettant de préparer, sauvegarder et réutiliser les ordres de travail complets avec toutes les informations nécessaires.
- Enregistrement automatique des données La GMAO élimine les inefficacités en enregistrant automatiquement les données des activités de maintenance. Les techniciens peuvent saisir les temps d’intervention, les matériaux utilisés et générer un rapport automatique de fin de tâche, réduisant ainsi le temps de reporting.
- Compte rendu automatique La GMAO simplifie le rapport final des interventions en fournissant les informations sur le temps de travail, les matériaux utilisés et les coûts en même temps que la clôture de l’opération.
- Rapports automatiques La GMAO collecte les données nécessaires pour surveiller les KPI et métriques de maintenance importantes comme le MTBF ou le MTTR. Cela permet de suivre en permanence les SLA sans avoir besoin de transférer manuellement les données vers des systèmes de business intelligence.
Rejoindre les experts
Ou découvrez le mainim GMAO avec la playlist vidéo.