Maintenance Conditionnelle
Dans le paysage industriel actuel, de plus en plus complexe et automatisé, les ingénieurs de maintenance peuvent utiliser différentes méthodologies de maintenance (chacune ayant ses propres avantages et inconvénients) pour gérer la maintenance industrielle afin de garantir l’efficacité opérationnelle et la compétitivité.
Dans ce contexte, il est essentiel de comprendre les différents types de maintenance – corrective, prédictive, préventive basée sur l’état et systématique – pour choisir le meilleur modèle pour votre entreprise.
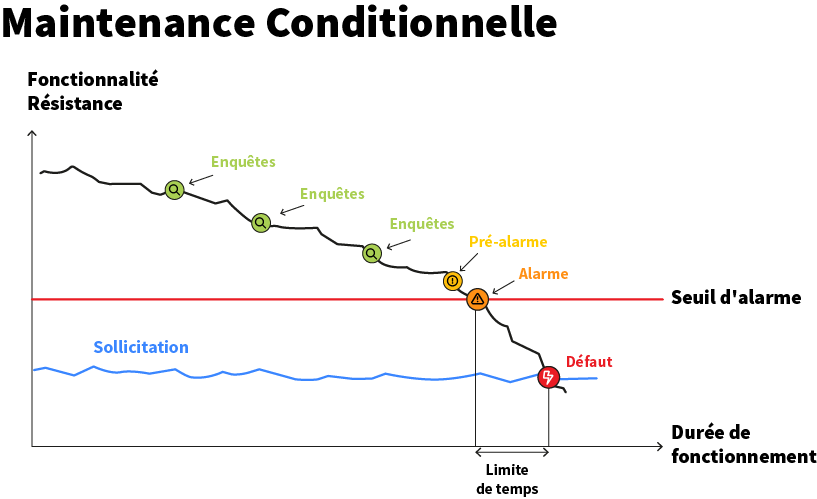
La maintenance conditionelle (également connue sous le nom de maintenance préventive conditionnelle ou maintenance on-condition) repose sur la capacité de prédire et de prévenir les défaillances à partir de données réelles sur les actifs, plutôt que de s’appuyer uniquement sur des délais prédéterminés, et constitue l’une des méthodologies les plus avancées et les plus stratégiques dans le domaine de la gestion de la maintenance industrielle.
Cette approche repose sur la surveillance continue des conditions de fonctionnement des actifs, l’objectif étant de n’intervenir que lorsqu’un actif atteint un certain état ou une certaine condition (d’où le terme « sur condition »), ce qui permet d’éviter les coûts inutiles et de maximiser l’efficacité en termes de temps.
Contrairement à la maintenance préventive, qui implique des interventions programmées à intervalles fixes ou planifiés, la maintenance conditionelle utilise les données collectées en temps réel pour prédire et prévenir les défaillances. Cette approche réduit le risque de temps d’arrêt imprévus et permet d’optimiser l’utilisation des ressources. Dans les prochains chapitres, nous verrons ce qu’est la maintenance préventive conditionnelle et comment elle fonctionne, mais si vous le souhaitez, vous pouvez voir un résumé de l’article dans la vidéo ci-dessous.
Qu’est-ce que la maintenance conditionnelle ?
La maintenance conditionnelle est une stratégie selon laquelle les travaux de maintenance ne sont effectués que lorsque les indicateurs d’état des machines indiquent qu’un certain état a été atteint et qu’il pourrait entraîner une anomalie ou une défaillance. En pratique, elle repose sur un système de surveillance continue qui collecte des données à partir de capteurs installés sur les actifs afin de détecter tout changement dans les paramètres de fonctionnement, tels que les vibrations, la température ou les niveaux de bruit.
La maintenance préventive conditionnelle est une méthode qui s’appuie sur l’analyse constante des performances des machines pour décider du moment de l’intervention. Elle diffère de la maintenance préventive, qui est programmée à intervalles fixes, indépendamment de l’état réel de l’actif.
Par exemple, le remplacement d’un roulement n’est effectué que lorsque les données de vibration indiquent une usure, plutôt qu’à des intervalles de temps fixes.
Voyez-vous des similitudes avec un autre type de maintenance ? Nous y reviendrons dans le prochain chapitre.
Différences entre la maintenance conditionnelle et la maintenance prédictive
Telle que nous l’avons définie, la maintenance conditionelle semble très similaire à la maintenance prédictive, mais il existe en réalité des différences substantielles.
La maintenance prédictive utilise des techniques et des algorithmes avancés d’apprentissage automatique pour prédire les défaillances futures en analysant les tendances des données historiques et actuelles. Par exemple, dans une usine de production automatisée, les capteurs de maintenance prédictive peuvent avertir qu’un moteur a 90 % de chances de tomber en panne dans les trois mois, ce qui permet aux responsables de programmer son remplacement. La maintenance préventive conditionnelle, quant à elle, réagit aux changements des paramètres de fonctionnement des actifs en temps réel, ce qui permet de ne prendre des mesures que lorsque les données indiquent une détérioration imminente.
Différences entre la maintenance conditionelle et les autres types de maintenance
- Maintenance préventive systématique : implique une maintenance programmée à intervalles réguliers, quel que soit l’état du système. Un exemple typique est la vidange d’huile à intervalles fixes. Cette stratégie peut être inefficace car elle implique des interventions même lorsqu’elles ne sont pas nécessaires.
- Maintenance prédictive : similaire à la maintenance conditionnelle, elle utilise une analyse avancée, telle que l’intelligence artificielle, pour prédire les défaillances futures sur la base de tendances et de modèles historiques. L’objectif est d’anticiper davantage les problèmes.
- Maintenance réactive : une action n’est entreprise qu’après l’apparition d’une défaillance. Ce type de maintenance implique des coûts élevés en raison des arrêts soudains et des réparations urgentes.
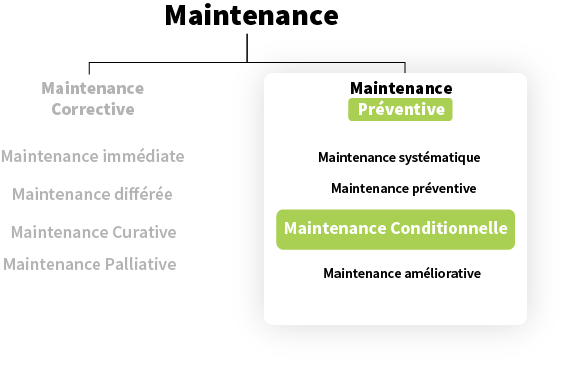
Quels sont les avantages de la maintenance préventive conditionnelle
L’utilisation de capteurs et d’outils d’analyse pour la maintenance conditionelle permet d’éviter les réparations inutiles et de réduire considérablement les temps d’arrêt, ce qui accroît l’efficacité opérationnelle. Dans l’industrie manufacturière, par exemple, cette approche permet de ne planifier les arrêts que lorsqu’ils sont réellement nécessaires, évitant ainsi les arrêts de production inutiles.
L’adoption d’une stratégie de maintenance préventive conditionnelle présente de nombreux avantages :
- Réduction des temps d’arrêt imprévus : grâce à la surveillance continue, les problèmes peuvent être détectés et résolus avant qu’ils ne se transforment en pannes majeures.
- Augmentation de la durée de vie des équipements : en n’intervenant que lorsque c’est nécessaire, le risque d’usure prématurée due à des interventions de maintenance inutiles est réduit.
- Optimisation des coûts d’exploitation : en évitant les interventions inutiles, les coûts de main-d’œuvre et de remplacement des composants sont réduits
- Amélioration de la gestion des ressources : la programmation des interventions basée sur des données réelles permet de planifier avec précision la disponibilité des ressources humaines et matérielles.
Limites et défis de la maintenance préventive conditionnelle
Malgré ses nombreux avantages, la mise en œuvre de la maintenance conditionnelle présente également certains défis :
- Coûts initiaux élevés : l’installation de capteurs et de systèmes de surveillance peut impliquer un investissement important, en particulier pour les entreprises disposant d’une flotte importante.
- Gestion des données : le traitement et l’analyse de grands volumes de données collectées par les capteurs nécessitent des systèmes informatiques avancés et des compétences spécifiques.
- Formation du personnel : le personnel technique doit être formé pour interpréter correctement les données et agir en conséquence.
Pour surmonter ces difficultés, de nombreuses entreprises choisissent d’adopter une approche progressive, en commençant par la surveillance des machines les plus critiques, puis en étendant la couverture à d’autres installations.
Comment mettre en œuvre un plan de maintenance conditionnelle efficace
Pour mettre en œuvre efficacement une stratégie de maintenance conditionnelle, et son plan de maintenance associé il convient de suivre quelques étapes clés :
- Évaluation initiale de l’équipement : identifier les machines critiques et déterminer les paramètres à surveiller (par exemple, les vibrations, la température, la pression).
- Sélection des capteurs et des systèmes de surveillance : sélectionner les capteurs appropriés et les intégrer à un système GMAO (gestion de la maintenance assistée par ordinateur) pour collecter et analyser les données
- Formation du personnel : il est essentiel que les techniciens soient correctement formés pour comprendre et interpréter les données collectées et pour mettre en œuvre les actions correctives nécessaires.
- Optimisation des interventions : une fois les signes de dégradation identifiés, planifier les interventions de maintenance de manière à minimiser l’impact sur la production, en optimisant éventuellement les activités en combinant des activités de maintenance préventive conditionnelle avec des activités préventives systématiques.
Exemples de maintenance conditionnelle
La maintenance conditionelle est très similaire au mécanisme de fonctionnement des feux de détresse d’une voiture. Un exemple efficace serait le voyant qui nous indique quand changer l’huile.
Par le biais de la maintenance préventive, sans donc surveiller l’état de notre réservoir, nous risquerions de changer l’huile avant qu’elle ne soit complètement épuisée. Dans ce cas, nous nous protégerions d’une panne très grave, mais en même temps nous serions obligés de remplacer l’huile prématurément, ce qui aurait pour conséquence de ne pas optimiser les coûts.
Au contraire, lorsque le voyant d’huile est allumé, nous savons exactement quand il est temps d’intervenir. Cette information nous permet donc de prendre une décision éclairée concernant la maintenance de notre voiture.
Un autre exemple pourrait être la surveillance de la pression d’une pompe à eau. Lorsque l’eau y circule, elle produit une certaine pression, mais toute fluctuation peut provoquer des pannes inattendues. En surveillant la pression indiquée par le manomètre fixé à la pompe, nous pouvons savoir quand cette condition se produit, ce qui nous permet d’intervenir à temps avant qu’il ne soit trop tard.
Maintenance conditionnelle dans le secteur manufacturier
Dans l’industrie manufacturière, la maintenance conditionnelle est utilisée pour surveiller les machines complexes telles que les presses, les tours et les robots d’assemblage. Grâce aux capteurs installés, toute anomalie de vibration ou de température des composants critiques peut être détectée en temps réel. Un exemple pratique est la surveillance des chaînes de production automobile, où les temps d’arrêt imprévus peuvent entraîner des retards importants et des pertes économiques.
Maintenance conditionnelle dans la gestion de flotte et les transports
Dans le secteur de la gestion de flotte, les véhicules sont équipés de capteurs qui surveillent la pression des pneus, le niveau d’huile et l’état du moteur. Lorsque les capteurs détectent que l’un de ces paramètres n’est pas conforme aux normes, la flotte peut être entretenue uniquement dans les véhicules qui le nécessitent, ce qui permet de gagner du temps et d’économiser des ressources.
Gérer la maintenance conditionnelle avec la GMAO
La mise en œuvre d’un système de Gestion de la Maintenance Assistée par Ordinateur (GMAO) est fondamentale pour une gestion réussie de la maintenance conditionnelle. Ce type de système permet non seulement de suivre l’état de santé des actifs en temps réel, mais aussi d’automatiser les alertes d’intervention lorsque certaines anomalies surviennent dans les paramètres de fonctionnement, comme les vibrations ou la surchauffe.
Un exemple concret de l’utilisation de la GMAO dans l’environnement industriel est son application dans les usines, où les activités de maintenance doivent être coordonnées efficacement pour assurer un fonctionnement continu et minimiser les temps d’arrêt. Dans ce cas, la GMAO est capable de collecter des données à partir de capteurs installés sur les actifs et d’alerter les opérateurs lorsque certains seuils critiques sont dépassés.
Mais elle ne se contente pas de générer des alarmes : la GMAO peut également optimiser la prise de décision et la gestion des ressources, en permettant de ne programmer les interventions de maintenance que lorsqu’elles sont vraiment nécessaires et en gérant efficacement la logistique des pièces détachées. Cette approche a été mise en œuvre avec succès dans la gestion des flottes, améliorant la continuité opérationnelle et réduisant le gaspillage lié aux interventions inutiles.
Outre ces avantages, une GMAO efficace peut également soutenir la planification stratégique de la maintenance en enregistrant et en analysant les données historiques relatives aux performances des actifs afin d’identifier les schémas récurrents et d’améliorer la capacité prédictive de l’ensemble du système.
Conclusions
Une stratégie de maintenance préventive conditionnelle ne doit pas nécessairement être considérée comme une alternative à d’autres formes de maintenance préventive telles que la maintenance programmée ou prédictive. Au contraire, elle représente souvent une valeur ajoutée, surtout lorsqu’elle est appliquée à des actifs ou à des installations stratégiques dont le simple suivi de certains paramètres peut générer des économies considérables et une optimisation de l’allocation des ressources qui peuvent être affectées à des actions préventives sur d’autres actifs qui nécessitent des approches différentes.
Contenu de l'article
- Qu’est-ce que la maintenance conditionnelle ?
- Différences entre la maintenance conditionnelle et la maintenance prédictive
- Différences entre la maintenance conditionnelle et les autres types de maintenance
- Quels sont les avantages de la maintenance préventive conditionnelle
- Limites et défis de la maintenance conditionnelle
- Comment mettre en œuvre un plan de maintenance conditionnelle efficace
- Exemples de maintenance conditionnelle
- Maintenance conditionnelle dans le secteur manufacturier
- Maintenance conditionnelle dans la gestion de flotte et les transports
- Gérer la maintenance conditionnelle avec la GMAO
Découvrez la GMAO mainsim en direct.
Réservez une démonstration pour découvrir comment fonctionne la GMAO grâce à une démonstration personnalisée.
F.A.Q.
Qu'est-ce que la maintenance préventive conditionnelle ?
La maintenance préventive conditionelle est une approche qui consiste à programmer des actions de maintenance en fonction de l’analyse de l’état réel de l’équipement. Contrairement à la maintenance préventive systématique, qui est basée sur des intervalles de temps prédéfinis, la maintenance conditionnelle utilise des indicateurs de performance et des données de capteurs pour déterminer quand intervenir.
Quelle est la différence entre la maintenance préventive systématique et la maintenance conditionnelle ?
- Maintenance préventive systématique : elle repose sur des contrôles et des interventions programmés à intervalles réguliers. Par exemple, le remplacement des filtres à air des systèmes de refroidissement des transformateurs tous les six mois, quel que soit leur état.
- Maintenance préventive conditionnelle : elle n’est effectuée que lorsque les données recueillies indiquent un risque de défaillance. Par exemple, un générateur éolien peut être entretenu uniquement lorsque les vibrations dépassent un certain seuil, ce qui signale un éventuel problème de roulement.
Pourquoi faire de la maintenance préventive conditionnelle ?
La maintenance conditionnelle est adoptée pour plusieurs raisons qui la rendent particulièrement efficace dans l’industrie de production à haute technicité et dans le secteur des transports (gestion de flotte) :
- Optimisation de la production : en évitant les défaillances soudaines des transformateurs ou des turbines, les temps d’arrêt sont réduits et la production continue d’énergie est assurée.
- Réduction des coûts : En n’intervenant que lorsque les capteurs détectent des conditions critiques, on évite les interventions programmées et coûteuses sur des installations qui n’en ont pas besoin.
- Sécurité accrue : l’identification précoce des problèmes permet de réduire le risque d’explosions ou de défaillances critiques susceptibles de mettre en péril la sécurité des opérateurs et l’environnement.
Quels sont les inconvénients de la maintenance conditionelle ?
Malgré ses nombreux avantages, l’adoption de la maintenance conditionnelle se heurte à certains obstacles :
- Coûts initiaux élevés : l’installation de capteurs sophistiqués sur des équipements tels que les turbines et les transformateurs peut s’avérer très coûteuse.
- Gestion complexe des données : des systèmes avancés de traitement des données des capteurs et d’analyse prédictive sont nécessaires.
- Fiabilité des capteurs : la précision des capteurs est cruciale ; un capteur défectueux peut provoquer de fausses alarmes ou ne pas signaler les problèmes réels, ce qui compromet l’efficacité de la maintenance.
Comment planifier la maintenance préventive conditionnelle ?
La planification de la maintenance préventive conditionnelle dans le secteur de l’énergie peut suivre les étapes suivantes :
- Identification des équipements critiques : se concentrer sur les composants critiques tels que les turbines, les transformateurs et les générateurs, qui nécessitent une surveillance continue
- Mise en œuvre de capteurs avancés : Utiliser des capteurs pour surveiller des paramètres tels que la température, la pression et le niveau d’huile dans les transformateurs ou les éoliennes.
- Analyse des données : Collecte et analyse des données à l’aide de systèmes de surveillance avancés. Par exemple, si la température d’un transformateur dépasse des limites prédéterminées, le système peut alerter les techniciens d’une défaillance potentielle.
- Définition de seuils d’intervention : établir des limites au-delà desquelles des mesures doivent être prises. Par exemple, si le niveau d’humidité de l’huile isolante d’un transformateur dépasse une certaine valeur, cela peut indiquer la présence d’un problème d’isolation.
Quels sont les paramètres contrôlés dans le cadre de la maintenance conditionnelle ?
Les paramètres les plus couramment contrôlés dans le cadre de la maintenance conditionnelle sont les suivants :
- Les vibrations : Une augmentation des vibrations peut indiquer une usure ou des problèmes mécaniques.
- Température : des températures excessives peuvent être le signe d’un fonctionnement inefficace ou de composants défectueux.
- Pression : des variations de la pression de fonctionnement peuvent indiquer une fuite ou une défaillance imminente.
• • Bruit : les capteurs d’analyse des décibels peuvent indiquer la détérioration de certains composants et signaler une défaillance imminente.
Rejoindre les experts
Ou découvrez le mainim GMAO avec la playlist vidéo.