Indicateurs de maintenance
Les indicateurs et KPI de maintenance sont des outils essentiels pour surveiller et améliorer l’efficacité des processus de maintenance au sein d’une entreprise. Ils permettent de mesurer la performance, d’identifier les points faibles et de prendre des décisions éclairées pour optimiser l’utilisation des ressources.
En fin de compte, des indicateurs bien choisis peuvent conduire à une réduction significative des coûts et à une amélioration de la disponibilité des équipements.
Cet article vise à fournir une compréhension complète des différents types de indicateurs maintenance, à expliquer comment les choisir en fonction des besoins de l’entreprise et à détailler les méthodes de mise en œuvre efficaces. Nous explorerons également des études de cas pratiques pour illustrer l’impact positif de ces indicateurs sur la gestion des équipements.
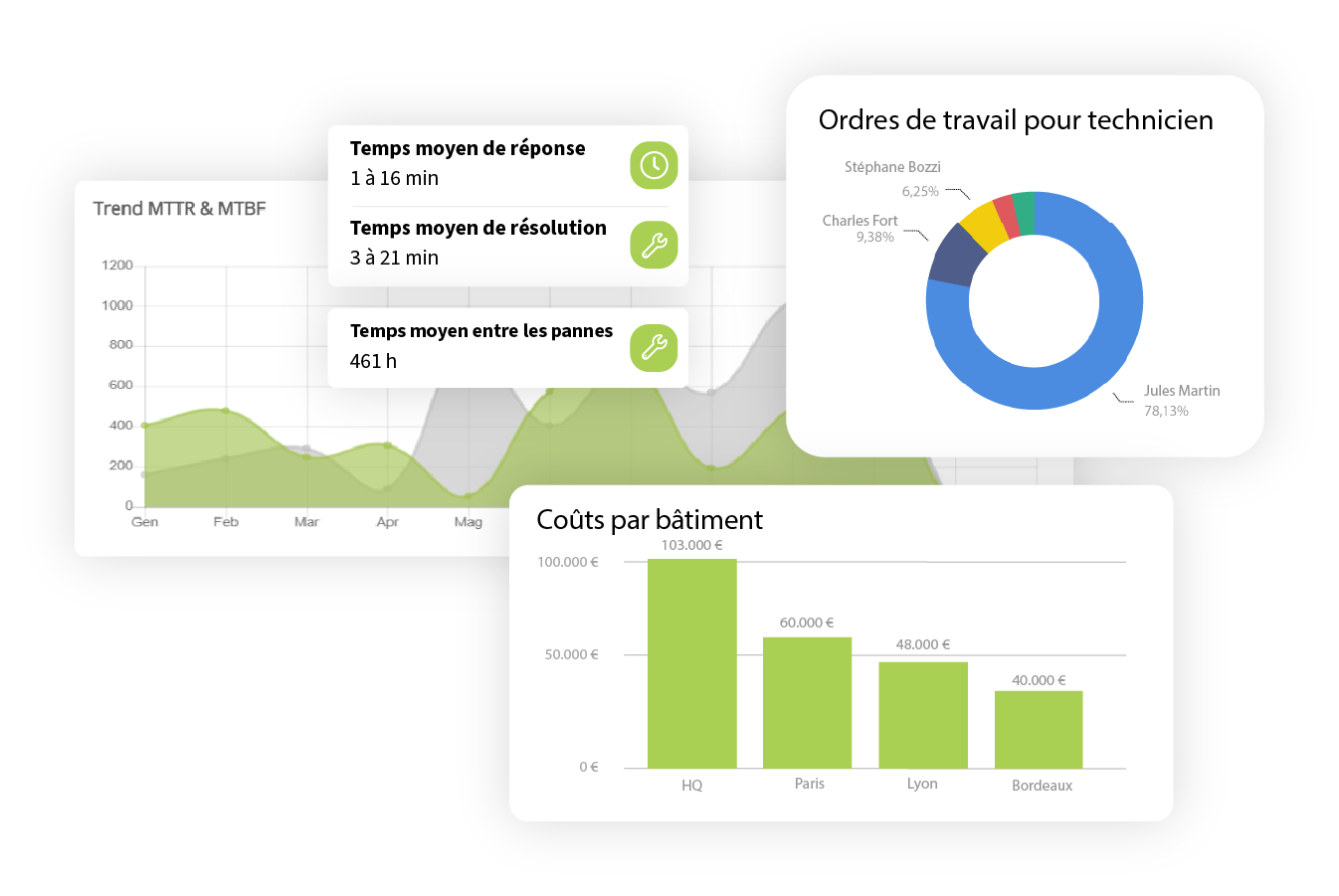
C’est quoi un indicateur de maintenance ?
Définition et rôles des indicateurs de maintenance
Un indicateur maintenance est une mesure quantitative utilisée pour évaluer l’efficacité des activités de maintenance.
Ils jouent un rôle crucial dans la surveillance des performances des équipements, l’optimisation des ressources allouées à la maintenance et la mise en place de stratégies d’amélioration continue.
Ces indicateurs permettent de détecter les anomalies, de planifier les interventions de manière proactive et d’assurer la fiabilité des équipements.
Les différences entre métriques et KPI
Il est important de distinguer entre les métriques et les KPI (Key Performance Indicators).
Les métriques sont des mesures quantitatives qui fournissent des données brutes sur les opérations de maintenance, tandis que les KPI maintenance sont des indicateurs clés de maintenance (ou ICP) qui évaluent la performance par rapport à des objectifs spécifiques.
Les KPI sont généralement dérivés des métriques et sont utilisés pour piloter des améliorations stratégiques.
Principaux Indicateurs de Maintenance
MTBF (Mean Time Between Failures)
Le MTBF, ou temps moyen entre les pannes, est un indicateur maintenance clé de la fiabilité des équipements. Il représente le temps moyen de fonctionnement d’un équipement avant qu’une panne ne survienne.
Le MTBF est crucial pour la planification de la maintenance préventive, car un MTBF élevé indique une plus grande fiabilité de l’équipement.
Comment calculer le MTBF
Le MTBF est calculé en divisant le temps total de fonctionnement d’un équipement par le nombre de pannes survenues pendant cette période.
MTBF= Temps total de fonctionnement ÷ Nombres de pannes
Utilité du MTBF
Un MTBF élevé permet de prévoir les interventions de maintenance et de réduire les interruptions non planifiées, améliorant ainsi la productivité et réduisant les coûts de maintenance.
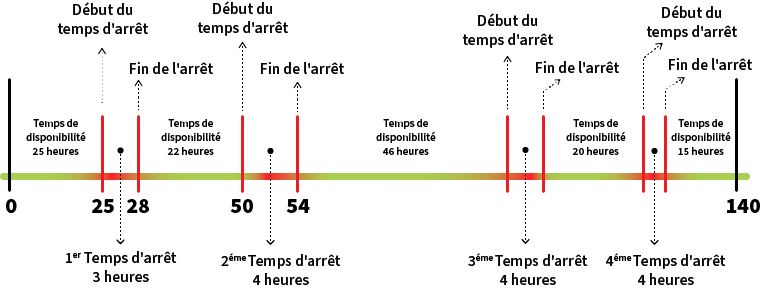
Comment améliorer le MTBF
Améliorer le MTBF est l’un des objectifs les plus courants dans le domaine de la production. Suivre l’indice KPI maintenance relatif au temps moyen entre les pannes permet de planifier nos activités de manière plus précise.
La première étape pour améliorer le MTBF est de s’assurer que les données sont enregistrées de la manière la plus précise possible. À cet égard, la disponibilité de la GMAO (Gestion de la Maintenance Assistée par Ordinateur) joue un rôle fondamental.
La deuxième étape consiste à investir du temps et des ressources dans des audits et des contrôles préventifs, afin de maintenir vos équipements en bon état en appliquant des logiques d’amélioration continue et de TPM (Maintenance Productive Totale).
MTTR (Mean Time to Repair)
Le MTTR, ou temps moyen de réparation, mesure le temps moyen nécessaire pour réparer un équipement après une panne. Cet indicateur maintenance est essentiel pour évaluer l’efficacité des processus de réparation et identifier les domaines où des améliorations peuvent être apportées.
Comment calculer le MTTR
Le MTTR est calculé en divisant le temps total passé à réparer les équipements par le nombre de réparations effectuées.
MTTR= Temps totale de réparation ÷ Nombre de réparations
Utilité du MTTR
Un MTTR faible indique que les réparations sont effectuées rapidement, minimisant ainsi les temps d’arrêt et améliorant la disponibilité des équipements.
Contenu de l'article
- C’est quoi un indicateur de maintenance ?
- Les différences entre métriques et KPI
- Principaux Indicateurs de Maintenance
- MTBF (Mean Time Between Failures)
- MTTR (Mean Time to Repair)
- Différence entre MTTR et Wrench Time
- MTTF (Mean Time to Failure)
- Taux de Disponibilité (Availability Rate)
- Taux de Rendement Global (Overall Equipment Effectiveness, OEE)
- Indicateurs de Coûts de maintenance
- Indicateurs de Qualité de la maintenance
- Métriques et Indicateurs liés à la Gestion des Services
- Métriques et Indicateurs de Maintenance liés à la Gestion des Actifs
- Métriques et Indicateurs de Maintenance liés au Contrôle des Coûts
- Guide des Métriques et Indicateurs de Maintenance
- Comment choisir les Indicateurs de Maintenance
- Mise en Œuvre des Indicateurs de Maintenance
Découvrez la GMAO mainsim en direct.
Réservez une démonstration pour découvrir comment fonctionne la GMAO grâce à une démonstration personnalisée.
Comment améliorer l’indicateur de maintenance MTTR
La meilleure méthode pour réduire le MTTR est sans aucun doute l’analyse des causes profondes des pannes. En surveillant attentivement les données de chaque actif, il est en effet possible d’identifier les causes potentielles de pannes à l’avance.
Avec un logiciel de gestion de maintenance moderne (GMAO), il est possible d’analyser en détail les causes des pannes fréquentes grâce à l’analyse des causes racines (Root Cause Analysis).
Une autre méthode tout aussi efficace pour réduire cet indicateur est la maintenance préventive, permettant de détecter les problèmes éventuels avant qu’ils ne se transforment en pannes plus graves. Cette approche proactive envers vos actifs se reflète positivement sur la valeur du MTTR.
Différence entre MTTR et Wrench Time
MTTR (Mean Time to Repair) et Wrench Time sont deux indicateurs de maintenance différents utilisés pour évaluer l’efficacité de la maintenance.
- MTTR (Mean Time to Repair) : Il s’agit du temps moyen nécessaire pour réparer une panne ou une anomalie, à partir du moment où elle se produit jusqu’à ce que le système soit à nouveau opérationnel. C’est une mesure de l’efficacité de la résolution des problèmes.
- Wrench time : Cela indique le temps réel que les techniciens passent à travailler physiquement sur l’équipement pendant une maintenance ou une réparation, en excluant les temps d’attente, de déplacement, de préparation, etc. C’est une mesure de la productivité sur le terrain.
En résumé, le MTTR mesure l’efficacité globale de la réparation, tandis que le wrench time mesure le temps de travail pratique réel lors de la réparation.
MTTF (Mean Time to Failure)
Le MTTF, ou temps moyen avant défaillance, est utilisé pour évaluer la durée moyenne de bon fonctionnement d’un équipement non réparable avant qu’une panne ne survienne. Il est particulièrement utile pour les composants qui ne peuvent pas être réparés et doivent être remplacés après une panne.
Comment calculer le MTTF
Le MTTF est calculé de manière similaire au MTBF, en divisant le temps total de fonctionnement par le nombre de défaillances.
MTTF= Temps total de fonctionnement ÷ Nombre de défiallance
Utilité du MTTF
Un MTTF élevé permet de prévoir les remplacements de composants et d’optimiser la gestion des stocks de pièces de rechange.
Taux de Disponibilité (Availability Rate)
Le taux de disponibilité mesure le pourcentage de temps pendant lequel un équipement est opérationnel et disponible pour la production.
C’est un indicateur clé de maintenance pour garantir que les équipements sont prêts à être utilisés lorsqu’ils sont nécessaires.
Comment calculer le taux de disponibilité
Le taux de disponibilité est calculé en divisant le temps de fonctionnement par le temps total (temps de fonctionnement plus temps d’arrêt) et en multipliant par 100 pour obtenir un pourcentage.
Taux de disponibilité = (Temps de fonctionnement ÷ Temps total )×100
Utilité du taux de disponibilité
Un taux de disponibilité élevé signifie que les équipements sont rarement hors service, ce qui améliore l’efficacité opérationnelle et réduit les pertes de production.
Taux de Rendement Global (Overall Equipment Effectiveness, OEE)
Le taux de rendement global (OEE) est un indicateur maintenance complet qui mesure l’efficacité des équipements en prenant en compte trois facteurs : la disponibilité, la performance et la qualité.
L’OEE est un outil puissant pour identifier les domaines d’amélioration et optimiser l’utilisation des équipements.
Comment calculer le OEE
L’OEE est calculé en multipliant les trois composantes : disponibilité, performance et qualité.
OEE= Disponibilité × Performance × Qualité
Chaque composante est elle-même un pourcentage calculé comme suit :
- Disponibilité : Temps de fonctionnement ÷ Temps total ×100
- Performance : Vitesse Réelle ÷ Vitesse Theorique ×100
- Qualité : Qualité : Unitée conforme ÷ unitée total produit ×100
Utilité de l’OEE
Un OEE élevé indique que les équipements fonctionnent à leur pleine capacité, avec peu de temps d’arrêt, à une vitesse optimale et produisant des produits de haute qualité.
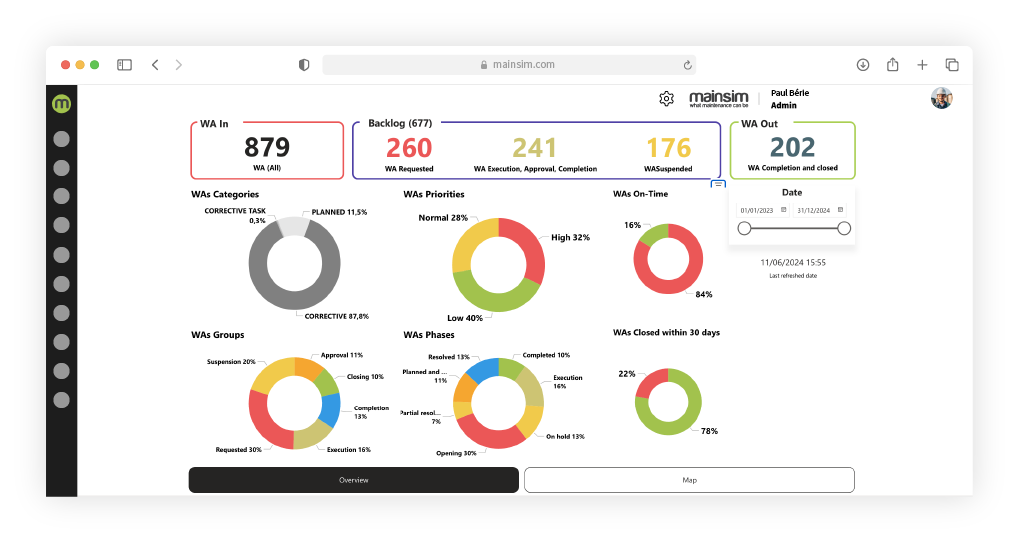
Autres metriques et indicateurs de maintenance importants
En plus des indicateurs principaux, mais il existe plusieurs autres indicateurs de maintenance importants :
- Taux de défaillance : Mesure la fréquence des pannes d’un équipement.
- Taux de maintenance planifiée : Évalue le pourcentage des interventions de maintenance qui sont planifiées par rapport aux interventions non planifiées.
- Coût de maintenance par unité de production : Analyse le coût de la maintenance par unité de produit fabriqué, permettant de mieux contrôler les dépenses de maintenance.
Indicateurs de Coûts de maintenance
Les coûts de maintenance sont un aspect critique de la gestion des opérations. Les indicateurs de coûts aident à surveiller et à contrôler les dépenses liées à la maintenance.
Quelques exemples incluent :
- Coût de maintenance total : Somme des coûts directs et indirects associés aux activités de maintenance.
- Coût de maintenance par unité produite : Coût de la maintenance divisé par le nombre d’unités produites sur une période donnée.
- Coût de maintenance par type d’intervention : Analyse des coûts en fonction des types d’interventions (préventive, corrective, etc.).
Indicateurs de Qualité de la maintenance
La qualité des interventions de maintenance a un impact direct sur la performance des équipements.
Les indicateurs de qualité incluent :
- Taux de réussite des interventions : Pourcentage des interventions de maintenance qui résolvent le problème sans besoin d’une intervention supplémentaire.
- Taux de réintervention : Pourcentage des interventions nécessitant une nouvelle intervention dans un délai défini.
- Satisfaction des clients internes : Mesure de la satisfaction des départements utilisateurs des équipements maintenus.
Métriques et Indicateurs de maintenance liés à la Gestion des Services
Les indicateurs et les métriques liés à la gestion des services sont des indicateurs particulièrement adaptés au secteur du Facility Management et du Global Service, mais ils peuvent également être appliqués dans des environnements industriels où l’on souhaite mesurer la performance du service de maintenance.
Grâce à ce groupe de KPIs, le responsable de la maintenance pourra répondre aux questions suivantes :
- Quelle est la performance du système de gestion des demandes d’intervention ?
- Quelle est la performance du processus de gestion des interventions programmées ?
- Combien et quels ordres de travail sont restés incomplets ?
Quel est le temps écoulé entre la survenance d’une panne et sa signalisation ? - Le processus de gestion présente-t-il des goulets d’étranglement ?
- Quels sont les indicateurs de maintenance relatifs à la gestion des services ?
KPI de Maintenance liés à la Gestion des Services :
- % d’Ordres de Travail (OT) correctifs clôturés dans un délai défini
- % d’Ordres de Travail (OT) planifiés clôturés dans un délai défini
- Backlog de maintenance (nombre d’Ordres de Travail en retard)
- Tendances des Ordres de Travail créés : maintenance corrective vs maintenance planifiée
- Ordres de Travail répartis par groupe
- Ordres de Travail répartis par catégorie
% des Ordres de Travail Correctifs et Planifiés clôturés dans la période définie
La rapidité dans la résolution des anomalies par le biais de maintenances correctives ou planifiées représente un indicateurs fréquemment utilisé par les gestionnaires de services généraux pour évaluer la conformité de l’équipe de maintenance et des fournisseurs par rapport aux ordres de travail émis.
Ces deux KPI sont exprimés en pourcentage, donc plus le résultat est proche de 100 %, plus le système est performant dans la gestion des anomalies.
Pour surveiller ce KPI maintenance, il est nécessaire de définir une période de référence (par exemple, un mois), à partir de laquelle il est possible de calculer le pourcentage de demandes de maintenance corrective/préventive clôturées dans la période indiquée.
Exemple de suivi
Vous pourriez fixer comme objectif de clôturer 85 % des ordres de travail correctifs dans un délai de 30 jours.
Si, à la fin du mois, vous obtenez une valeur de 70 %, cela signifie que seulement 70 % des ordres de travail ont effectivement été clôturés dans le délai imparti.
Cela indique la nécessité d’examiner de plus près les causes de ce retard, qu’il s’agisse de la quantité de ressources allouées ou de goulots d’étranglement dans le processus de maintenance.
Conseil rapide
Ce type d’analyse est automatiquement réalisé par un système de la GMAO (Gestion de Maintenance Assistée par Ordinateur), grâce à des tableaux de bord et des graphiques en camembert qui facilitent le suivi de ce indicateur de maintenance.
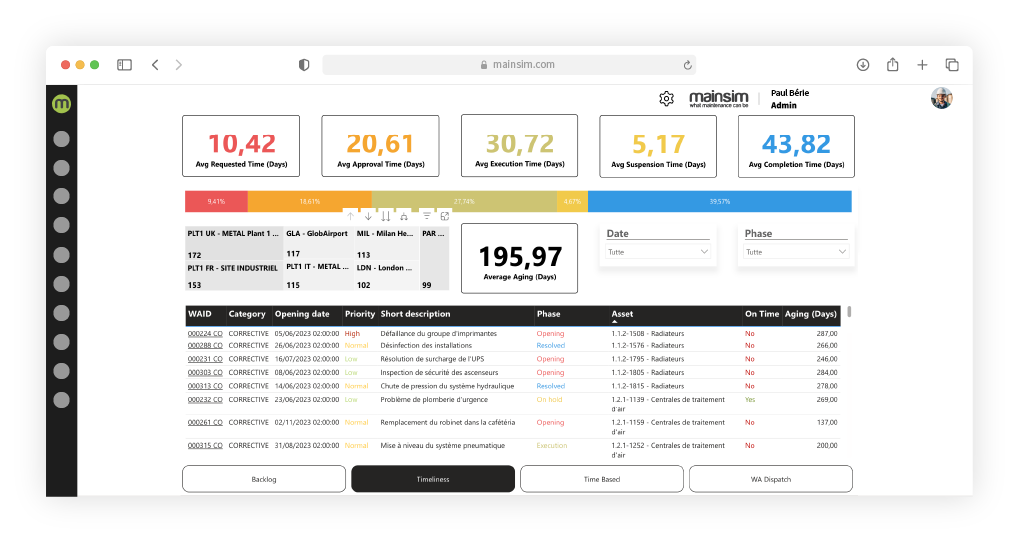
Backlog de maintenance
Pour assurer une gestion performante des ordres de travail, dans une perspective d’amélioration continue, il est nécessaire d’avoir une vision précise du travail en retard et de savoir à quel moment le processus de maintenance n’a pas réussi à traiter les ordres de travail.
Si une demande d’intervention est introduite dans le processus mais n’est pas prise en charge, il est essentiel d’en avoir connaissance, car avec le temps, la panne signalée pourrait entraîner d’autres problèmes. De plus, ce KPI peut mettre en lumière d’éventuels problèmes d’allocation des ressources.
Il va sans dire que tous les ordres de travail et les demandes d’intervention n’ont pas la même importance ou ne sont pas également urgents. Faire la distinction sans outil peut être compliqué. Une GMAO permet de classer les ordres de travail par niveau de priorité, par exemple en fonction de la criticité de l’actif.
Cela étant dit, il est normal d’avoir un certain nombre d’ordres de travail en retard. L’objectif du suivi de ce KPI est de maintenir ce nombre à un niveau acceptable, gérable par l’équipe de techniciens disponibles. De plus, il peut être utile de déterminer quelle partie de ces ordres de travail en retard concerne la maintenance préventive et laquelle concerne la maintenance corrective.
Conseil rapide
La GMAO vous permet de garder un œil sur les ordres de travail non traités, grâce à un graphique en camembert placé sur le tableau de bord principal de la GMAO. Le système peut également afficher la liste par ancienneté et priorité décroissantes, en mettant en évidence les ordres de travail les plus anciens avec la plus haute priorité.
Tendance des Ordres de Travail créés
En visualisant l’évolution des ordres de travail dans le temps, il est possible d’identifier les périodes critiques où se produisent habituellement le plus d’anomalies. Analyser la tendance des ordres de travail créés, en comparant les correctifs aux planifiés, est utile pour optimiser l’utilisation des ressources et comprendre si notre plan de maintenance préventive fonctionne ou s’il doit être révisé.
World Class Standard
Le standard de classe mondiale fixe comme objectif optimal d’atteindre 90 % d’ordres de travail préventifs par rapport aux correctifs.
Ordres de Travail par groupe et catégorie
Répartition par phases opérationnelles et types d’interventions
Répartir les ordres de travail par groupe (phases de travail) et par catégorie (types de maintenance) est une méthode simple pour identifier les éventuelles critiques et les goulots d’étranglement.
Le suivi de ces KPI doit se faire en temps réel, assurez-vous donc d’avoir la technologie adéquate pour le faire.
Un GMAO contient ces informations pour chaque ordre de travail individuel, permettant de déterminer en un coup d’œil quelles phases opérationnelles nécessitent plus de temps ou l’impact de certains types d’intervention sur le total.
Répartition par Responsable, Fournisseur, Demandeur
De la même manière que pour la répartition par actif, il peut être utile d’analyser la répartition des ordres de travail en fonction des acteurs impliqués dans le processus de maintenance : l’activité d’un technicien interne, l’intervention d’un éventuel fournisseur externe ou la personne ayant demandé un service ou signalé une panne.
Pourcentage de Maintenance Planifiée
Le Pourcentage de Maintenance Planifiée (PMP) est un indicateur précieux pour suivre l’intégrité d’un programme de maintenance préventive et identifier les opportunités de réduire les actions correctives. Cette métrique mesure la quantité d’heures (exprimée en %) consacrées à la maintenance planifiée par rapport au total des interventions réalisées. La maintenance planifiée ne comprend pas celle programmée en réponse à une panne déjà survenue.
Comment le calculer :
PMP = Heures dédiées à la maintenance planifiée / Heures de maintenance totales x 100
Couverture de la Maintenance Planifiée
La maintenance programmée est la pierre angulaire d’un plan de maintenance solide. Pour réduire et prévenir les pannes, il est essentiel de surveiller la couverture des maintenances programmées effectuées par rapport à la planification prévue et de superviser la répartition de la planification future.
Métriques et Indicateurs de Maintenance liés à la Gestion des Actifs
Le deuxième groupe, Gestion des Actifs, se réfère à des métriques et KPI dont l’objectif principal est de surveiller des valeurs spécifiques à l’ingénierie de la maintenance.
Ces indicateurs permettent d’élever la maintenance à un niveau de connaissance et de professionnalisme supérieur, souvent utilisés dans les secteurs industriel et manufacturier où il est nécessaire de surveiller des machines et des équipements.
Grâce à ces indicateurs maintenance, vous pourrez répondre aux questions suivantes :
- Quel est le temps écoulé entre deux anomalies consécutives sur le même actif (MTBF) ?
- Quel est le temps moyen nécessaire pour résoudre une anomalie sur un actif spécifique (MTTR) ?
- Quels sont les actifs ayant présenté le plus d’anomalies (Top Worst Assets) ?
- Quel est le temps de chaque réparation individuelle (MRT – Wrench Time) ?
KPI de Maintenance liés à la Gestion des Actifs :
- Mean Time Between Failures (MTBF)
- Mean Time To Repair (MTTR)
- Mean Time To Failure (MTTF)
- Mean Repair Time (MRT)
- Mean Time Between Maintenance (MTBM)
- Nombre Total d’Arrêts de Machine
- Top Worst Assets (Pires actifs en termes de performance)
- Temps moyen de détection (MDT)
- Temps de réponse moyen (MRET)
- Temps de fonctionnement moyen (MOT)
- Analyse des causes profondes (RCA)
Temps de réparation (ou Wrench Time)
Souvent considéré comme une métrique ou un KPI mineur, peu significatif dans l’évaluation des processus de maintenance, le temps de réparation (en anglais Wrench Time) peut en réalité fournir des informations cruciales pour identifier les goulots d’étranglement et améliorer le flux de travail.
Conseil rapide :
Avec mainsim, il est possible de suivre ce temps de réparation de deux manières différentes :
- Par le biais d’une compilation manuscrite du champ Temps de réparation.
- En utilisant l’application mobile avec le bouton Rec&Stop
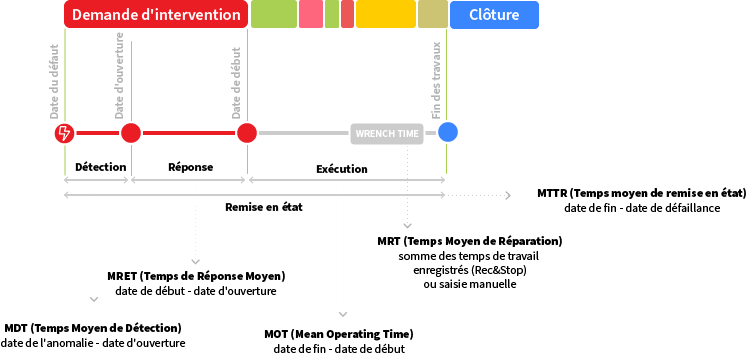
Nombre de pannes
Surveiller le nombre de pannes ou d’arrêts de machine représente souvent l’étape initiale dans la gestion et l’analyse des KPI en gestion des actifs. Ces arrêts peuvent résulter soit d’une maintenance non planifiée, comme une panne d’équipement ou la rupture d’un composant nécessitant l’arrêt de la machine pour réparation, soit d’arrêts planifiés, qui correspondent généralement à une activité de maintenance préventive.
Ce indicateur est très utile pour identifier les actifs qui impactent le plus les processus de production et de maintenance. En repérant ces actifs, il est possible d’investiguer les causes principales des pannes pour déterminer, par exemple, s’il existe des défauts inhérents à un actif spécifique, tels que des erreurs de conception.
Comment suivre le nombre d’arrêts de machine ?
Avoir une idée précise de la disponibilité de vos actifs signifie disposer d’un outil de diagnostic et d’un indicateur de performance pertinent, tant pour la maintenance que pour la production. Par exemple, un taux élevé d’arrêts pourrait indiquer que le plan de maintenance préventive choisi ne fonctionne pas comme prévu ou que quelque chose ne va pas dans le processus de production.
Avec la GMAO, vous pouvez approfondir l’analyse en vous concentrant sur des zones spécifiques, comme une ligne de production particulière ou un actif unique, pour comprendre quels composants ont causé la panne et analyser de manière détaillée les problèmes rencontrés et leurs effets.
Top worst asset
Les plus mauvais actifs
Un logiciel de GMAO vous permet de consulter à tout moment la liste des biens qui ont connu le plus de défaillances sur une période donnée, afin de vous aider à identifier immédiatement les biens qui doivent faire l’objet de votre attention, par exemple en mettant en œuvre ou en affinant des politiques de maintenance planifiée ciblées en fonction des causes profondes des problèmes rencontrés.
Métriques et Indicateurs de Maintenance liés au Contrôle des Coûts
Le troisième groupe, Contrôle des Coûts, se réfère à des métriques et KPI dont l’objectif est de définir les coûts liés à la maintenance.
Les coûts peuvent être influencés par le type de maintenance effectuée, l’utilisation de ressources internes ou externes (fournisseurs, entreprises de services) et les matériaux employés.
L’analyse de ces KPI permet de répondre aux questions suivantes :
Quel est le coût de la maintenance, pendant une période donnée, pour un actif spécifique ?
Quelle part de la main-d’œuvre représente le coût total de la maintenance ?
Quelle part des coûts des matériaux de rechange représente le coût total ?
KPI de Maintenance liés au Contrôle des Coûts :
- Coût total de la maintenance corrective
- Coût total de la maintenance planifiée
- Poids en % de la maintenance corrective par rapport à la maintenance planifiée
- Poids en % de l’utilisation de ressources externes par rapport aux ressources internes
- Coût de la main-d’œuvre
- Coût des matériaux
- Coût des biens et services
- Répartition des coûts par processus de maintenance et par actif
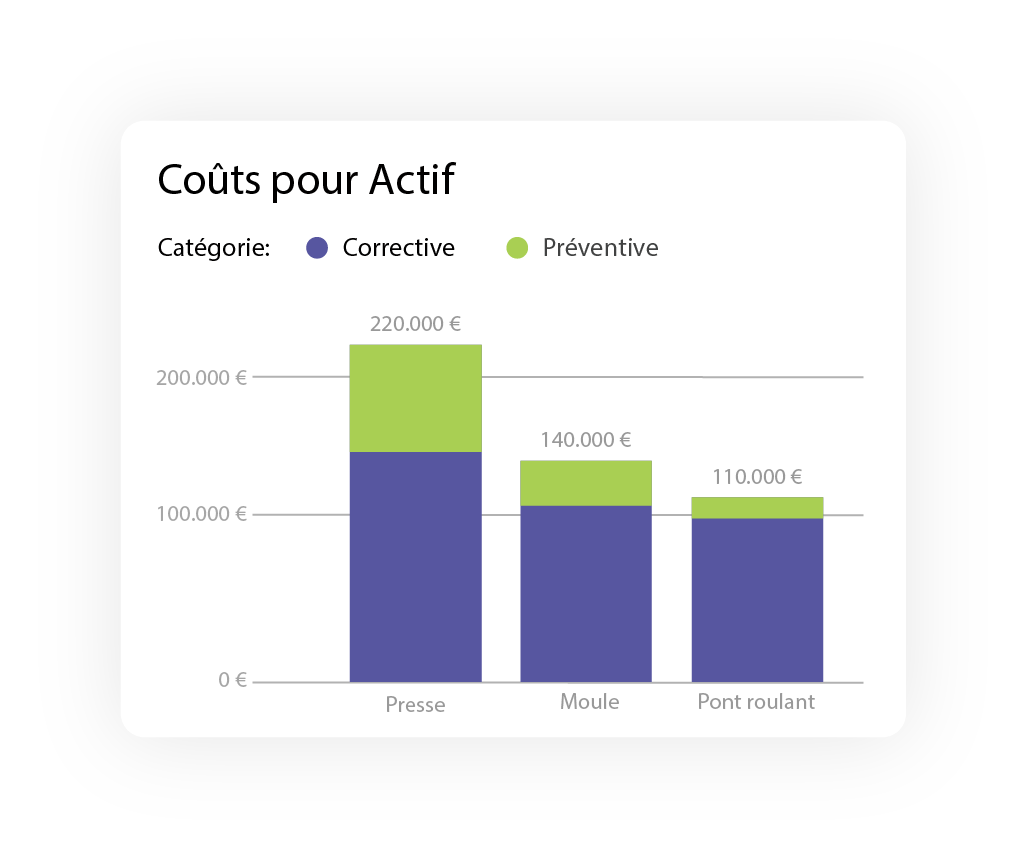
Coût total de la maintenance corrective
En plus des indicateurs relatifs aux services et à la maintenance, il est également important de pouvoir calculer les coûts et d’utiliser ces références comme KPI pour évaluer les performances des opérations de maintenance.
Ce KPI représente le coût total imputable uniquement aux interventions de maintenance corrective. Le coût doit prendre en compte les éléments associés à l’éventuelle utilisation de ressources externes (fournisseurs), calculés comme l’achat de services tiers, ou de ressources internes (utilisation d’heures de travail du personnel), ainsi que la consommation éventuelle de matériaux de rechange et d’autres dépenses.
Coût total de la maintenance préventive
L’analyse de ce KPI permet de surveiller le coût total imputable uniquement aux interventions de maintenance planifiée.
Comme pour le coût de la maintenance corrective, cet indicateur de performance doit également prendre en compte l’éventuelle utilisation de ressources internes et externes, de matériaux et d’autres dépenses.
Conseil rapide : Calculer manuellement toutes ces variables peut s’avérer coûteux en termes de temps et d’efforts, étant donné que plusieurs intervenants, y compris externes à l’entreprise, sont souvent impliqués. Un CMMS (système de gestion de la maintenance assistée par ordinateur) peut simplifier ce processus en automatisant le reporting et en impliquant tous les acteurs.
Poids en % de la maintenance corrective par rapport à la maintenance planifiée
Ce KPI sert à calculer le coût exprimé en % de la maintenance corrective par rapport à la maintenance planifiée.
L’objectif idéal serait d’annuler l’impact des pannes imprévues en augmentant l’effort consacré à la maintenance préventive. Par exemple, si 1 500 euros ont été dépensés pour la maintenance corrective (ex. heures de travail + matériaux) et 500 euros pour la maintenance planifiée (ex. heures de travail), le KPI serait : (1500/2000) * 100 = 75 %
L’objectif est de rapprocher ce KPI le plus possible de 0 %. Dans l’exemple ci-dessus, la maintenance corrective a représenté 75 % des coûts totaux, attribuables par exemple à la consommation de matériaux coûteux, qui, avec une bonne politique de maintenance préventive, n’auraient probablement pas été nécessaires.
Poids en % de l’utilisation des ressources internes par rapport aux ressources externes
Ce KPI consiste à calculer le poids exprimé en pourcentage de l’utilisation de la main-d’œuvre interne sur le total des dépenses de main-d’œuvre (main-d’œuvre interne + services tiers).
Grâce à ce paramètre, il est possible d’analyser et de décider si l’on doit privilégier l’externalisation des services ou l’utilisation de ressources internes à l’entreprise.
Coût total de la main-d’œuvre
Ce KPI permet d’analyser l’impact des ressources humaines impliquées dans le processus de maintenance, en termes de coût et d’heures de travail. Le CMMS mainsim met à disposition des indicateurs dédiés à la répartition temporelle ainsi qu’à la répartition par actif et par catégorie (type d’intervention).
Coût total des matériaux
Ce KPI analyse l’utilisation des matériaux employés, en termes de coût et de quantité. Comme pour la main-d’œuvre, mainsim propose des indicateurs relatifs à la répartition temporelle, par actif et par catégorie.
Coût total des biens et services
Ce KPI mesure le coût total des biens et services fournis par des ressources externes à l’entreprise, c’est-à-dire des services achetés auprès de tiers. L’objet du regroupement est le fournisseur individuel.
Répartition des coûts par processus de maintenance et par hiérarchie des actifs
En plus des analyses détaillées pour chaque type de ressource, mainsim propose d’autres analyses globales, telles que la répartition des types de coûts pour chaque processus de maintenance, par hiérarchie des actifs et par répartition temporelle.
Guide des Métriques et Indicateurs de Maintenance
Maintenant que nous avons une vue d’ensemble plus précise de ce que nous pouvons mesurer en fonction de nos objectifs, il est temps d’explorer ces métriques et KPIs en détail. Ci-dessous, nous proposons une vue d’ensemble des principaux indicateurs, accompagnée des formules de calcul, des normes de classe mondiale, et de quelques conseils pour améliorer les résultats.
Bien entendu, chacune de ces métriques peut également être calculée manuellement, à condition de suivre correctement les processus et de disposer de données précises et fiables.
Si vous utilisez déjà une bonne GMAO (Système de Gestion de Maintenance Assistée par Ordinateur), il est probable que vous suivez déjà certaines de ces métriques et KPIs, qui, selon les objectifs choisis, sont automatiquement fournis par le système.
Comment choisir les KPI de Maintenance
Alignement avec les objectifs de l’entreprise
Pour choisir les bons indicateurs de maintenance, il est crucial de s’assurer qu’ils sont alignés avec les objectifs stratégiques de l’entreprise. Par exemple, si l’objectif principal est de réduire les coûts de production, les indicateurs de coûts et de performance seront prioritaires.
Revue des processus de maintenance existants
Avant de sélectionner les indicateurs, il est essentiel de comprendre les processus de maintenance actuels. Cette revue peut inclure une analyse des méthodes de travail, des ressources disponibles, et des résultats actuels. Les outils tels que les audits de maintenance et les analyses de flux de travail peuvent être utiles dans cette étape.
Implication des parties prenantes
L’implication des parties prenantes dans le processus de sélection des indicateurs est essentielle pour garantir leur pertinence et leur acceptation. Les parties prenantes peuvent inclure les équipes de maintenance, les opérateurs, les gestionnaires de production et les responsables financiers.
Utilisation de la méthode SMART
Les indicateurs de maintenance doivent être SMART (Specific, Measurable, Achievable, Relevant, Time-bound). Cette approche garantit que les indicateurs sont bien définis, mesurables, réalisables, pertinents par rapport aux objectifs de l’entreprise, et limités dans le temps pour permettre un suivi et une évaluation continus.
Mise en Œuvre des Indicateurs de Maintenance
Collecte des données
La collecte de données précises et fiables est la première étape de la mise en œuvre des indicateurs de maintenance. Les sources de données peuvent inclure les systèmes de gestion de la maintenance assistée par ordinateur (GMAO), les rapports d’intervention, les journaux de production et les inspections d’équipements.
Analyse et interprétation des données
Une fois les données collectées, elles doivent être analysées pour identifier les tendances, les anomalies et les opportunités d’amélioration. Des outils d’analyse de données, tels que les tableaux de bord et les logiciels d’analyse statistique, peuvent être utilisés pour faciliter cette étape.
Communication et formation
La communication des résultats des indicateurs de maintenance aux parties prenantes est essentielle pour garantir leur compréhension et leur engagement. De plus, des formations régulières doivent être organisées pour s’assurer que toutes les parties prenantes comprennent comment utiliser les indicateurs pour améliorer les processus de maintenance.
Ajustement et amélioration continue
Les indicateurs de maintenance ne sont pas figés et doivent être régulièrement révisés et ajustés en fonction des évolutions des processus de maintenance, des technologies et des objectifs de l’entreprise. L’amélioration continue repose sur l’analyse périodique des résultats et la mise en œuvre de mesures correctives pour optimiser les performances.
Conclusions
Les métriques et les indicateurs de maintenance nous permettent de mettre en lumière les processus de maintenance, rendant ainsi nos actions et la performance de nos actifs mesurables.
Il existe de nombreuses façons dont ces métriques peuvent nous aider à réduire le nombre d’arrêts de machine, améliorer l’allocation des ressources, réduire les coûts et augmenter l’efficacité au sein de notre entreprise.
Choisir les bonnes métriques est la première étape vers l’amélioration continue. En fonction de notre niveau de maturité, des outils à notre disposition et des objectifs que nous avons définis, nous pouvons nous concentrer sur les indicateurs pertinents, qu’ils soient liés au niveau de service, à nos actifs ou au contrôle des coûts.
Cependant, il est important de noter que pour surveiller correctement les métriques et les KPIs, un effort initial considérable est nécessaire pour garantir que les données que nous analysons soient entièrement fiables.
Disposer de une GMAO est certainement la voie la plus simple, mais certaines de ces métriques peuvent également être surveillées avec d’autres méthodes et outils. L’effort requis sera sans aucun doute plus important, mais les bénéfices seront les mêmes.
Rejoindre les experts
Ou découvrez le mainim GMAO avec la playlist vidéo.