AMDEC : Le guide complet de l’analyse des modes de défaillance, des effets et de la criticité
AMDEC est l’acronyme français d’Analyse des Modes de Défaillance (AMD), de leurs Effets (E) et de leur Criticité (C).
Connue en anglais sous le sigle FMEA (Failure Modes and Effects Analysis), est une méthode d’analyse qui permet aux entreprises de déterminer l’impact que pourraient avoir les défaillances potentielles sur un système, un produit ou un processus, et d’évaluer les risques dans le but d’identifier des actions correctives ou préventives à mettre en œuvre.
L’analyse AMDEC, ainsi que ses variantes, comme PAMDEC ou DAMDEC, que nous aborderons dans cet article, sont largement utilisées dans des secteurs tels que l’automobile, l’aéronautique et l’industrie électrique. Toutefois, cette méthode trouve également son utilité dans d’autres domaines, comme le facility management ou le secteur de la santé.
Dans cet article, nous vous expliquerons ce qu’est l’analyse et la méthode AMDEC, comment mener une analyse FMEA/AMDEC étape par étape, puis nous examinerons les erreurs les plus courantes tout en vous offrant des conseils pratiques pour optimiser l’utilisation de la méthodologie AMDEC au sein de votre entreprise.
Qu’est-ce que l’analyse AMDEC : Définition
L’AMDEC (en anglais FMEA ou FMECA) est une méthodologie systématique utilisée pour identifier et évaluer les modes de défaillance d’un produit ou d’un processus, en analysant leurs conséquences et en cherchant à atténuer les risques associés.
L’acronyme AMDEC signifie en français Analyse des Modes de Défaillance, des Effets et de la Criticité.
En d’autres termes, l’AMDEC est une méthode d’analyse systématique des défaillances visant à comprendre leurs effets, à évaluer les risques et les conséquences, afin de mettre en œuvre des actions correctives, d’amélioration ou de mitigation pour renforcer la fiabilité des actifs et des processus, et réduire les risques ou les effets négatifs générés par une non-conformité.
Aperçu historique : l’origine de la méthode FMEA
Le terme FMEA a été créé aux États-Unis par l’entreprise McDonnell Douglas au milieu des années 1960. À l’époque, le processus FMEA consistait à dresser une liste des composants d’un actif ou d’un produit, à recueillir des informations sur les modes de défaillance, leur fréquence et leurs conséquences.
Rapidement, la NASA a adopté ce même système pour évaluer l’efficacité de ses systèmes. La méthode s’est ensuite étendue aux secteurs automobile et aéronautique, devenant un outil clé pour l’analyse des défaillances. Elle a ensuite été utilisée dans des domaines variés, allant de la fabrication industrielle au facility management ou encore à la santé, où le FMEA est aujourd’hui fréquemment employé pour évaluer les effets et les risques pour les patients.
FMEA, FMECA, AMDEC : Quelles sont les différences ?
Très souvent, en anglais, il existe une certaine confusion entre FMEA et FMECA. Ce que nous avons déjà expliqué à propos de la première, tandis que la FMECA peut être considérée à juste titre comme une évolution de la FMEA. En effet, la FMECA va un pas plus loin dans l’analyse, en intégrant un outil permettant d’associer à chaque mode de défaillance un niveau de criticité, à l’aide du Risk Priority Number (RPN).
Concrètement, cette extension nous permet de classer la criticité d’un actif ou d’un risque.
En réalité, l’AMDEC prévoit déjà l’utilisation de la matrice de risque (le Risk Priority Number, en français Numéro de Priorité de Risque, ou NPR), concrétisée par la dernière lettre de l’acronyme, la lettre C qui signifie criticité. Ainsi, il serait plus juste de dire que l’analyse AMDEC n’est pas tant l’équivalent de la FMEA que de la FMECA. Mais cela reste une question de terminologie qui n’a pas une grande importance ici.
Contenu de l'article
- Qu’est-ce que l’analyse AMDEC : Définition
- Aperçu historique : l’origine de la méthode FMEA
- FMEA, FMECA, AMDEC : Quelles sont les différences ?
- Types d’analyses AMDEC
- Quels sont les avantages pour les entreprises d’adopter la méthode AMDEC ?
- Un exemple pratique : Guide d’utilisation du modèle AMDEC pour la maintenance et la gestion des risques.
- Phase 1. Définir le « Quoi? » : Analyse initiale
- Phase 2. Assemblage de l’équipe interfonctionnelle
- Phase 3. Identification des modes de défaillance
- Phase 4. Analyse des effets
- Phase 5. Évaluation des risques : Gravité, Probabilité et Détectabilité
- Indice de Priorité de Risque (IPR) : Qu’est-ce que c’est, à quoi ça sert et comment utiliser la matrice IPR dans l’analyse AMDEC
- Comment utilise-t-on le calcul de l’IPR ?
- Quel est l’objectif de l’Indice de Priorité de Risque (IPR) ?
- Comment calculer l’IPR (Indice de Priorité de Risque) dans l’analyse AMDEC
- Phase 6. Identifier les actions correctives et réduire les risques
- Phase 7. Suivi et révision
- Quels sont les principaux obstacles à l’adoption de l’AMDEC ?
- Les erreurs les plus courantes dans l’utilisation du modèle AMDEC
- Stratégies pour rendre l’analyse AMDEC plus objective
- Applications pratiques de l’analyse AMDEC dans différents secteurs
- Le rôle de la GMAO dans l’analyse AMDEC
- Inconvénients et limites des modèles AMDEC
Découvrez la GMAO mainsim en direct.
Réservez une démonstration pour découvrir comment fonctionne la GMAO grâce à une démonstration personnalisée.
Types d’analyses AMDEC
Avant d’aborder le sujet, permettez-moi de vous donner un aperçu des petites différences que l’on rencontre dans les différentes typologies d’analyses AMDEC. Bien entendu, les choses varient en fonction du domaine d’application ou du type d’étude que l’on souhaite réaliser, que l’on utilise l’AMDEC pour un processus, un produit, etc.
Voici un rapide récapitulatif des différences :
- AMDEC-C de Conception (en anglais : DFMEA – Design FMEA) Utilisée lors de la phase de conception et de développement, l’AMDEC de Conception permet d’analyser les défaillances potentielles d’un produit afin de résoudre les problèmes avant la production.
- AMDEC-P de Processus (en anglais : PFMEA – Process FMEA) L’AMDEC de Processus se concentre sur les processus de production et d’assemblage, en identifiant les erreurs potentielles pouvant survenir pendant le processus de fabrication. Ces erreurs et défaillances concernent le processus lui-même plutôt que les actifs comme les équipements ou les lignes de production. C’est la principale différence entre AMDEC-P et AMDEC-M.
‘AMDEC de produit (en englais : Product FMEA), permet de vérifier la viabilité d’un produit développé par rapport aux exigences du client ou de l’application ;
- AMDEC-M – Moyen (en anglais : MFMEA ou EFMEA)
Largement utilisée dans l’industrie et la fabrication, où la fiabilité des équipements et des moyens est cruciale pour la continuité des opérations et la qualité du produit final, l’AMDEC-M se concentre sur l’analyse des défaillances potentielles des machines et équipements de production, en étudiant comment ces défaillances peuvent affecter la qualité du produit, les temps d’arrêt des machines et la sécurité. - AMDEC-S de Sécurité (en anglais : SFMEA)
Il s’agit d’une méthodologie AMDEC spécifique pour analyser les modes de défaillance ayant un impact direct sur la sécurité, souvent utilisée dans les industries automobile, aéronautique, ferroviaire et dans le secteur de la santé. - AMDEC-SRV de Service (en anglais : Service FMEA)
La méthode AMDEC appliquée aux services permet d’évaluer les problèmes potentiels qui pourraient compromettre la qualité d’un service fourni à un client. Ce n’est certainement pas l’une des plus utilisées. - AMDEC-L de Logicielle (en anglais : SW-FMEA)
Il s’agit de la même méthode AMDEC appliquée à l’ingénierie logicielle pour identifier des problèmes, des bogues et des défaillances, en prenant en compte des aspects tels que le code, les données, l’interface graphique, etc.
Quels sont les avantages pour les entreprises d’adopter la méthode AMDEC ?
L’adoption de ce modèle d’analyse offre aux entreprises une opportunité importante pour améliorer les processus et la qualité de leurs produits. Voici les principaux bénéfices :
- Identification proactive des risques : L’AMDEC permet d’identifier et de cartographier les risques, aidant ainsi les responsables HSE à mettre en place toutes les mesures nécessaires pour les réduire et standardiser les processus.
- Amélioration de la qualité : Grâce à l’analyse systématique des processus et des produits, l’AMDEC de processus aide les responsables à améliorer la qualité des produits en réduisant le nombre de défauts et de non-conformités.
- Amélioration de la fiabilité des actifs : La méthode AMDEC, associée aux moyens de production, permet aux responsables de la maintenance de se concentrer sur la fiabilité des actifs, en amenant l’analyse des défaillances et la gestion des priorités à un nouveau niveau.
- Réduction des coûts : Prévenir les défaillances et les non-conformités aide les entreprises à réduire les coûts associés aux réparations, aux rebuts et aux rappels de produits, ayant un impact positif sur les coûts de maintenance et les services après-vente.
- Amélioration de la qualité des données : La qualité des données est un aspect central de toute analyse AMDEC réussie. Améliorer la qualité des données à la disposition de l’équipe et de leurs superviseurs permet de prendre de meilleures décisions.
- Collaboration interfonctionnelle : Ce point est souvent sous-estimé, mais il est essentiel pour une bonne utilisation de l’analyse AMDEC. L’FMEA favorise le travail d’équipe entre différentes fonctions de l’entreprise, facilitant la communication et l’échange d’idées pour résoudre les problèmes plus efficacement.
- Soutien à la maintenance préventive : En identifiant les points critiques dans les processus, l’AMDEC Moyen permet d’optimiser les plans de maintenance préventive ou d’améliorer les stratégies de maintenance conditionnelle, réduisant ainsi les temps d’arrêt et améliorant l’efficacité opérationnelle.
- Traçabilité du processus : Enregistrer les actions entreprises ou les modifications apportées à un processus permet de maintenir à jour une base de données d’informations cruciale lors des audits clients ou des audits de certification.
- Promotion de l’amélioration continue : L’approche proactive de l’FMEA encourage les entreprises à poursuivre une amélioration continue, stimulant l’innovation dans les processus et les produits.
Un exemple pratique : Guide d’utilisation du modèle AMDEC pour la maintenance et la gestion des risques.
Quelles sont les étapes clés pour appliquer un modèle AMDEC ?
L’implémentation efficace de l’AMDEC nécessite des compétences, de la formation, de l’engagement en termes de temps et de ressources, ainsi que la capacité de surmonter les difficultés que tout le monde rencontre, plus ou moins, lors de la collecte des données. Vous êtes déjà découragé ?
Voici donc un guide en 7 étapes pour vous aider à vous orienter dans cette complexité (et quelques petits trucs appris sur le terrain).
Phase 1. Définir le « Quoi? » : Analyse initiale
La première étape consiste à bien définir l’étendue de l’analyse. Identifiez clairement quel est le système, le produit, le processus ou même la ligne de production sur lequel vous souhaitez concentrer votre action.
Commencez par une approche ciblée et limitée pour garantir que vous pourrez élargir votre analyse à mesure que vous gagnez en expérience et en ressources.
Au cours de cette phase initiale, réalisez une analyse AS-IS (tel quel) du produit ou du processus. Des outils tels que le diagramme de flux (flow chart), le QFD (Quality Function Deployment), les arbres de défaillance ou le VRP (Variety Reduction Program) peuvent vous être très utiles. De plus, obtenez des schémas d’implantation, comme un éclaté de l’équipement ou des manuels du fabricant.
Faites une liste de tous les composants impliqués, que ce soit sous forme de tableau Excel ou d’un autre format. N’hésitez pas à organiser des séances de brainstorming avec l’ensemble du personnel pour collecter toutes les idées et informations disponibles. Cela favorisera l’identification des risques potentiels tout en exploitant les connaissances et l’expérience de tous les acteurs impliqués.
Phase 2. Assemblage de l’équipe interfonctionnelle
Si je devais te dire comment appliquer un modèle AMDEC en entreprise, je te répondrais « pas tout seul ».
Dès le début, commence à impliquer le personnel et identifie les personnes clés dans les différents équipes et départements qui peuvent contribuer au projet ou en bénéficier. Par exemple, si tu souhaites appliquer un modèle AMDEC à la maintenance, implique également l’équipe des opérations, la production et le responsable qualité. Plus tôt tu impliques ces acteurs, plus tôt tu pourras les intégrer au projet.
L’AMDEC, ou FMEA, est avant tout un travail d’équipe. Une collaboration étroite entre les différents départements permet non seulement d’identifier plus précisément les risques et défaillances, mais aussi de trouver des solutions plus efficaces. En incluant différentes perspectives, l’analyse devient plus complète et plus efficace, ce qui conduit à de meilleures décisions pour l’entreprise.
Phase 3. Identification des modes de défaillance
Nous entrons maintenant dans les phases opérationnelles avec l’analyse des modes de défaillance. Dans un AMDEC de maintenance, il est essentiel de cartographier tous les modes de défaillance possibles d’un équipement, c’est-à-dire les façons dont une machine ou un appareil peut se casser ou ne pas fonctionner correctement.
Effectuer une analyse sérieuse des modes de défaillance (en anglais, Failure Mode Analysis) représente un effort considérable pour de nombreuses entreprises. Celles qui disposent déjà d’un outil plus avancé qu’un simple (mais complexe) fichier Excel, comme une GMAO (Gestion de la Maintenance Assistée par Ordinateur) ou un autre logiciel de maintenance, peuvent profiter de cette occasion pour aller plus loin, en utilisant ces données pour étendre l’analyse à l’RCA (Root Cause Analysis – Analyse des causes profondes), en explorant plus en détail les causes de la défaillance.
Est-ce une bonne idée ? La réponse est oui, mais seulement si nous sommes capables de standardiser le processus d’entrée des données et d’automatiser leur mise à jour. Sinon, si vous devez entrer toutes les données manuellement, je vous recommande de reporter l’analyse des causes profondes (RCA) à plus tard, en vous concentrant d’abord sur les actifs les plus critiques. Le risque serait d’être littéralement submergé par les données.
D’autre part, l’analyse des causes de défaillance représente une ressource précieuse lors de la planification, aidant les responsables à élaborer des plans de maintenance plus précis et à se concentrer sur la fiabilité des actifs.
Quelques conseils pour identifier les modes de défaillance dans l’analyse AMDEC :
Lorsque vous réalisez une AMDEC sur des équipements physiques comme par exemple une installation ou un véhicule, les modes de défaillance deviennent plus spécifiques. Regroupez les modes de défaillance en catégories allant de la simple erreur qui n’affecte pas les fonctions de l’équipement, jusqu’à la défaillance totale (temps d’arrêt). Ces catégories concerneront l’effet du défaillance sur le processus ou le produit, et cela nous sera utile plus tard, lorsque nous devrons établir les niveaux de criticité.
Prenons l’exemple d’une pompe centrifuge. Parmi les modes de défaillance, je noterai sans doute des défaillances hydrauliques, mécaniques, des problèmes de corrosion, etc. Divisez les causes de défaillance en grandes catégories, puis placez-y les causes spécifiques. Voici ci-dessous un exemple de tableau des causes de défaillance classées par catégories.
Conception/Construction/Production
- Erreur de conception
- Erreur de fabrication
- Erreur de construction/installation
- Erreur de modification de la conception
Opérations/Erreur humaine
- Action accidentelle
- Procédure inadéquate/erronée
- Non-exécution de la procédure
- Manque ou absence de formation
- Maintenance inadéquate
Composant externe
- Systèmes de support
- Connexions
Environnement extérieur
- Feu/fumée
- Humidité
- Haute/basse température
- Champ électromagnétique
- Radiation
- Bio-organismes
- Contamination/poussière/saleté
Composant interne
- Usure normale
- Défaillance prématurée
- Environnement interne
Phase 4. Analyse des effets
Nous disposons enfin d’un arbre des défaillances et les processus sont tracés. Nous avons collecté les premières données à analyser, ce qui nous permet de poursuivre l’AMDEC en identifiant les effets. Pour chaque mode de défaillance isolé, il s’agit maintenant de déterminer quels effets il génère sur le processus.
Voici une liste des effets les plus couramment rencontrés, que ce soit dans l’AMDEC de processus ou celle de maintenance :
- Aucun effet
- Impact environnemental
- Arrêt machine
- Blocage
- Perte d’automatisation
- Cycles de production plus longs que ceux nominalement prévus (perte de quantité)
- Difficultés de redémarrage après un arrêt dû, par exemple, à une intervention technique
- Production de matériaux non conformes (perte de qualité)
- Consommation excessive de matériaux
- Consommation excessive d’électricité
- Sécurité
Pour poursuivre avec notre exemple d’AMDEC appliqué à une pompe centrifuge, une défaillance pourrait avoir un effet localisé, limité à un seul composant. Ou bien, elle pourrait avoir un impact sérieux sur le système de refroidissement auquel elle appartient. À son tour, un système de refroidissement défaillant pourrait entraîner des conséquences sur les niveaux de production, voire un arrêt complet des opérations.
Lors de l’analyse des effets, il est probable que vous finissiez par revoir la cartographie des défaillances, car vous réaliserez que certaines défaillances peuvent avoir un impact significatif sur d’autres. Une fois cette étape terminée, vous serez prêt à aborder la phase suivante de votre analyse FMEA : l’évaluation des risques.
Phase 5. Évaluation des risques : Gravité, Probabilité et Détectabilité
Nous avons cartographié les modes de défaillance ainsi que leurs effets sur le processus. Notre tableau AMDEC commence à se remplir.
Il est désormais nécessaire de construire une stratégie pour gérer chaque scénario possible décrit dans notre analyse. Si vous avez bien travaillé, votre tableau AMDEC contiendra probablement une longue liste de défaillances potentielles.
L’étape suivante consiste à évaluer le risque associé à chacune d’entre elles et à les classer en fonction de leur gravité. Cela permet d’obtenir une vision aussi objective que possible des interventions nécessitant une priorité immédiate.
Heureusement, un outil spécifique est conçu pour nous aider dans cette analyse : le Indice de Priorité de Risque (IPR) ou en englais, Risk Priority Number (RPN).
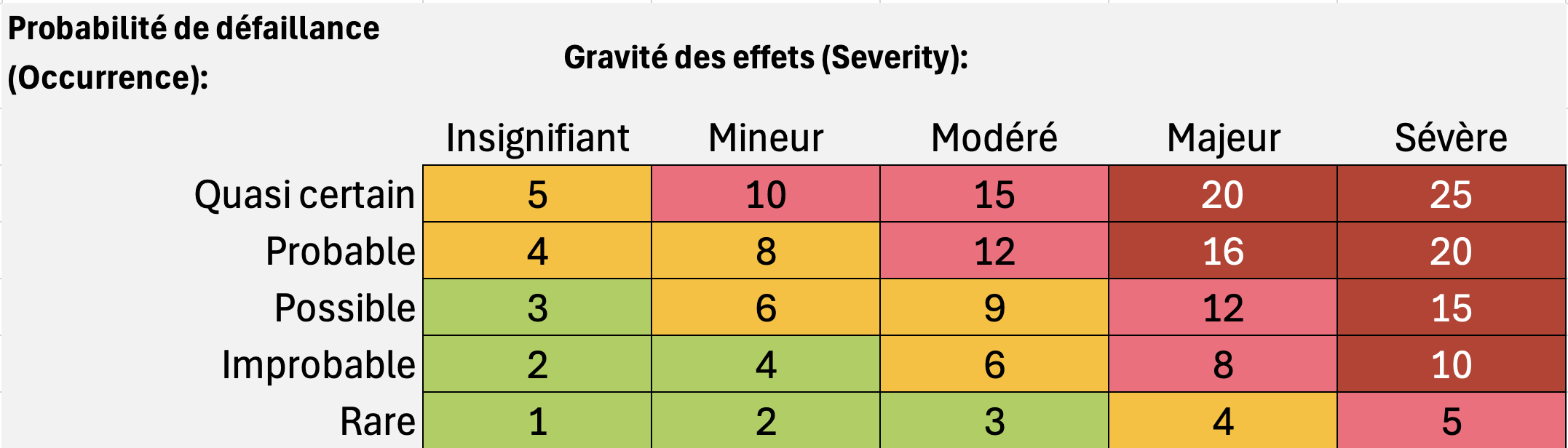
Indice de Priorité de Risque (IPR) : Qu’est-ce que c’est, à quoi ça sert et comment utiliser la matrice IPR dans l’analyse AMDEC
L’Indice de Priorité de Risque (IPR) est un outil clé dans l’analyse AMDEC (Analyse des Modes de Défaillance, de leurs Effets et de leur Criticité). Il permet d’évaluer et de prioriser les risques associés à chaque mode de défaillance en se basant sur des critères bien définis.
Dans les analyses FMEA en anglais, il est appelé Risk Priority Number (RPN) et cela pourrait générer un peu de confusion : mais IPR et RPN sont la même chose.
Comment utilise-t-on le calcul de l’IPR ?
Le calcul de l’IPR est très simple. Il suffit de multiplier trois facteurs pour obtenir un indice qui prend en compte les aspects suivants :
- Probabilité (Occurrence)
- Détectabilité (Detection)
- Gravité (Severity)
Quel est l’objectif de l’Indice de Priorité de Risque (IPR) ?
L’IPR est le produit des 3 aspects mentionnés ci-dessus. Il va de soi que plus notre IPR est élevé, plus le risque généré par la défaillance est élevé, et donc plus la priorité d’adopter des actions spécifiques pour atténuer ses effets et conséquences est grande. L’objectif est de créer une échelle de priorités peuplée de numéros indices.
1. Probabilité de défaillance (Occurrence)
Sans surprise, la probabilité de défaillance (dans l’FMEA en englais, on parle de Occurrence) indique la probabilité qu’un équipement, un composant ou un système tombe en panne, générant ainsi un résultat négatif. Notre objectif ici est d’attribuer un numéro indice à cette probabilité.
Évidemment, un score plus élevé signifie que l’événement est plus susceptible de se produire. À l’inverse, une valeur basse indique un défaut ou un risque très rare.
Lorsque nous évaluons les probabilités de défaillance, nous devons prendre en compte plusieurs facteurs, comme la vétusté de l’équipement ou d’éventuelles fluctuations saisonnières.
Cela complique légèrement les choses, car il faudrait également suivre un score de fiabilité de l’actif et l’inclure dans le calcul final, ce qui signifie que nous aurions encore plus de données à mettre à jour. Ce n’est pas vraiment une bonne idée si vous n’avez pas de logiciel GMAO à votre disposition.
Les données historiques sont cruciales dans ce cas. À ce titre, un logiciel GMAO peut devenir un centre d’information d’une valeur inestimable, tout comme une culture des données considérée comme un actif de l’entreprise. Bien sûr, l’expérience des responsables de la maintenance ou de la production représente également une source précieuse, mais nous devons aussi être vigilants à l’objectivité des données : un ingénieur de maintenance et un technicien de production pourraient avoir des opinions divergentes sur les probabilités de défaillance.
Si nous avons quelques données, certains indicateurs de maintenance peuvent être utiles. Je parle de :
- Failure Rate ou taux de panne.
- MTBF (Mean Time Between Failures), le temps moyen entre les pannes
Le premier indique le rapport entre le nombre de défaillances et le temps total d’utilisation d’une machine. Il est exprimé en pourcentage et nous aide à identifier les actifs ayant les meilleures et les pires performances.
Le second représente le temps moyen entre chaque panne, c’est-à-dire combien d’heures de fonctionnement s’écoulent avant qu’un problème n’apparaisse.
Si vous utilisez un logiciel GMAO ou un système EAM, vous disposez probablement déjà de ces deux indicateurs.
Lors des analyses AMDEC, on utilise généralement une échelle de 1 à 10 pour coder la probabilité, répartie comme suit :
- 1 : Événement extrêmement improbable
- 2 à 4 : L’événement peut se produire dans certains cas, mais la probabilité est très faible
- 5 à 7 : L’événement peut se produire occasionnellement
- 8 à 9 : Il existe une forte probabilité que l’événement se produise
- 10 : L’événement est pratiquement inévitable
Il est essentiel d’être le plus objectif possible dans vos évaluations et de partager avec le reste de l’équipe des lignes directrices claires pour la saisie des données dans le tableau.
2. Détectabilité de la défaillance (Detection)
La deuxième valeur dont nous avons besoin pour calculer l’indice de risque est la détectabilité de la défaillance, indiquée dans l’AMDEC par la lettre D (en englais pour Detection). Il s’agit d’évaluer notre capacité à diagnostiquer un problème avant qu’il ne génère des effets négatifs sur le reste du processus ou du système.
Comme pour la probabilité, nous pouvons également utiliser une échelle de 1 à 10 pour la détectabilité. L’important est que plus la valeur est élevée, plus nous nous rapprochons de 10, plus il est probable que l’événement ne soit pas détecté. Ainsi :
- 1 = L’événement est sûrement détecté
- 10 = Il est pratiquement impossible de détecter le problème
Notre objectif est donc de maintenir cet indice aussi bas que possible. Pour réduire l’indice de détectabilité de la défaillance ou du risque, les entreprises peuvent utiliser des capteurs de contrôle appliqués aux actifs, des relevés de compteurs, des caméras, réaliser des inspections régulières, etc.
Cependant, la question à laquelle nous voulons répondre est : Est-ce que cela en vaut la peine ? C’est pourquoi nous mettons en relation la Detection avec les deux autres facteurs. Le prochain est la gravité.
3. Gravité de la défaillance (Severity)
Nous arrivons maintenant au dernier facteur nécessaire au calcul de l’indice de risque : la Severity, ou gravité des effets générés par une défaillance. Dans cette analyse, nous cherchons à qualifier la gravité d’un événement (ou d’une série d’événements en chaîne), en partant toujours de nos modes de défaillance (failure mode). Nous pouvons utiliser la même échelle de 1 à 10, où 1 indique une gravité nulle et 10 un danger mortel.
Comment calculer l’IPR (Indice de Priorité de Risque) dans l’analyse AMDEC
Nous avons vu ce qu’est l’IPR (ou RPN), l’indice de priorité du risque, Un indicateur. Il ne nous reste plus qu’à le calculer, et c’est très simple.
Voici la formule pour calculer l’IPR :
IPR = P x D x S
Où, bien sûr,
- P signifie Probabilité (Occurrence),
- D signifie Detection (Détectabilité),
- S signifie Severity (Gravité).
Une fois que nous aurons attribué à chacun de ces facteurs son indice de 1 à 10, nous serons prêts pour le calcul.
Si tu penses que jusqu’ici tout a été facile, tu peux aller plus loin, par exemple en associant à tout cela une série de mesures visant à réduire l’impact des risques, en calculant à son tour le facteur de pondération. À ce stade, je dirais que tu es devenu un expert et prêt pour l’étape suivante.
Phase 6. Identifier les actions correctives et réduire les risques
À ce stade, nous avons rempli toutes les cases de notre tableau AMDEC ou de notre feuille Excel. Il ne reste plus qu’à identifier et planifier les actions correctives (ou préventives, si nécessaire) pour atténuer les risques associés aux modes de défaillance et d’erreur les plus critiques.
Dans une AMDEC de conception, ces actions pourraient inclure des modifications du design du produit, tandis que dans une AMDEC de processus, des améliorations des processus ou l’implémentation de contrôles supplémentaires pourraient être envisagées.
Comme mentionné dans le paragraphe précédent, nous pourrions même aller jusqu’à évaluer les actions d’amélioration comme des facteurs dans le calcul global, en créant un score de pondération qui nous permette d’évaluer l’efficacité des actions entreprises. Cependant, cette étape n’est pas strictement une procédure d’analyse FMEA et doit être considérée comme une opération supplémentaire.
Si vous utilisez une GMAO avec des fonctionnalités modernes, comme mainsim, quelque chose de similaire peut être trouvé dans le module de gestion des risques. En effet, dans ces colonnes, sont indiquées les prescriptions et les actions destinées à réduire les risques (comme le port de certains EPI ou l’obtention d’une certification), chacune ayant un poids dans l’identification des facteurs de risque après la mise en œuvre des mesures de mitigation.
Phase 7. Suivi et révision
Après la mise en œuvre, le travail n’est évidemment pas terminé. Une fois arrivé à cette étape du processus de mise en œuvre correcte d’une analyse AMDEC, le rôle des données devrait être désormais clairement compris.
Si tout s’est bien passé, votre organisation devrait avoir une vision plus claire des processus, et les avantages d’une culture vertueuse basée sur une approche rigoureuse des données devraient être tout aussi évidents.
À ce niveau, il est important de continuer à surveiller l’efficacité et de répéter le processus chaque fois qu’une nouvelle information ou un nouveau problème survient. En effet, une analyse FMEA bien réalisée génère plus de valeur à ce stade, lorsque nous avons déjà consolidé nos données, et continuons à alimenter nos rapports avec de nouvelles preuves et des points critiques.
Quels sont les principaux obstacles à l’adoption de l’AMDEC ?
Nous avons vu en détail comment effectuer une analyse AMDEC et quels sont les 7 étapes clés. Est-ce suffisant pour réussir avec ce modèle ?
Bien sûr, vous devrez faire face à certains obstacles. Ne vous inquiétez pas, dans ce chapitre, nous allons voir ensemble comment aborder les plus courants.
- Résistance au changement : De nombreux employés (et même les managers) peuvent être réticents à modifier des pratiques et des processus qui se sont consolidés au fil du temps. La résistance au changement est l’un des défis les plus fréquents, surtout lorsque la culture de l’entreprise n’est pas orientée vers les données. Essayez d’impliquer le personnel dès le début et assurez-vous que tout le monde adhère au projet en mettant en avant les avantages.
- Manque de formation et de compétences : D’accord, mettre en œuvre efficacement un modèle AMDEC nécessite un minimum de compétences en gestion de projet. L’absence de formation adéquate peut limiter la capacité de l’équipe à réaliser des analyses aussi approfondies et à interpréter correctement les résultats.
- Temps et ressources allouées : Dans un monde où tout le monde est toujours pressé et où le backlog de maintenance augmente constamment, allouer du temps et des ressources pour une analyse aussi approfondie est une décision qui doit être prise à l’avance. Bien sûr, les bénéfices sont un argument important pour expliquer l’importance de ce travail.
- Difficulté de collecte des données : Une analyse FMEA n’est pas pour tout le monde. Beaucoup dépend du degré de maturité de votre entreprise ou de votre département. Si vous gérez encore la maintenance avec papier et crayon ou par oral, il est évident que vous pourriez rencontrer quelques problèmes difficiles à résoudre. Vous devez vous assurer que votre équipe est prête à relever ce défi, et peut-être envisager l’implémentation d’un logiciel de gestion de la maintenance. Rappelez-vous : sans données fiables, l’analyse sera beaucoup moins efficace, au point de devenir inutile.
- Complexité du processus : La méthodologie AMDEC peut sembler assez complexe, avec de nombreuses étapes et des détails à prendre en compte. Commencez petit. Concentrez-vous au début sur quelques actifs clés, ou même sur un seul processus ou produit. Gardez les choses simples, expérimentez, puis étendez le processus au reste de l’organisation.
- Mauvaise collaboration interfonctionnelle : Il devrait maintenant être clair pour vous que la méthodologie AMDEC nécessite l’implication de différentes fonctions au sein de l’entreprise. Le manque de collaboration entre les départements peut entraver le processus et réduire l’efficacité de l’analyse.
Faire face à ces obstacles (et ne pas simplement fermer les yeux en prétendant qu’ils n’existent pas) est crucial pour maximiser les avantages de l’AMDEC et garantir que cela devienne un outil efficace pour la gestion des risques et l’amélioration continue de votre entreprise.
Les erreurs les plus courantes dans l’utilisation du modèle AMDEC.
En plus des difficultés que nous avons déjà abordées, il est important de prêter attention à ne pas commettre des erreurs qui pourraient nous éloigner de notre objectif. Voici une liste des erreurs que je rencontre fréquemment dans les entreprises :
- Définition insuffisante du périmètre opérationnel : C’est l’erreur commise dès le départ. Il est essentiel de définir très clairement quel actif ou processus vous souhaitez surveiller. Encore une fois, commencez petit, puis élargissez progressivement.
- Sous-découpage : C’est une erreur dans laquelle pratiquement tout le monde tombe, et elle est presque inévitable. On ne peut pas prévoir tous les scénarios dès le départ. Au fur et à mesure de votre analyse AMDEC, vous vous rendrez compte que de nouvelles modes de défaillance et leurs implications apparaîtront. Il n’est pas nécessaire d’avoir tout défini dès le début, mais il faut veiller à mettre à jour les modes de défaillance de manière continue.
- Évaluation subjective des scores : Attribuer des scores de gravité, de probabilité et de détectabilité de manière subjective et non standardisée peut entraîner une analyse AMDEC incohérente et fausser les résultats. La communication, une formation minimale et le partage de procédures standard avec tous les membres de l’équipe sont essentiels pour garantir une plus grande objectivité.
- Limiter l’attention aux risques critiques : Se concentrer uniquement sur certains modes de défaillance peut être une stratégie correcte, mais elle comporte des limites. Il est important d’élargir progressivement les cas à étudier et de ne pas se limiter à un nombre restreint de risques.
- Manque de mises à jour périodiques : Un tableau AMDEC datant de 5 ou 10 ans n’a plus aucune valeur, sauf en termes de comparaison ou de référence initiale. Les modifications des processus ou même le simple remplacement d’une machine peuvent entraîner une perte rapide de pertinence de l’analyse initiale.
- Sous-estimer la détectabilité : Il n’y a pas grand-chose à dire à ce sujet. Parmi tous les facteurs d’analyse, la détectabilité est souvent celle qui est traitée en dernier. En effet, il est facile de surestimer les capacités de l’équipe et de créer un faux sentiment de sécurité concernant notre capacité à identifier les problèmes avant qu’ils ne causent des dommages importants. Parfois, il peut s’écouler plusieurs jours avant que l’on se rende compte de l’usure de quelques roulements.
Stratégies pour rendre l’analyse AMDEC plus objective
La subjectivité est de loin le principal problème et la « peau de banane » sur laquelle la plupart des équipes glissent. La subjectivité dans l’évaluation de la gravité, de la probabilité et de la détectabilité lors d’une analyse AMDEC peut entraîner des erreurs et des incohérences.
Heureusement, il existe quelques conseils et stratégies pour en réduire l’impact. Voici quelques-unes des plus efficaces, selon mon expérience:
- Utilisation de tableaux de référence standard : Mettre en place des tableaux de référence pour l’évaluation de la gravité, de la probabilité et de la détectabilité peut fournir des critères objectifs pour l’attribution des scores. Ces tableaux devraient être basés sur des expériences précédentes, des meilleures pratiques sectorielles ou sur celles suggérées par les normes SAE (Society of Automotive Engineers).
- Formation et sensibilisation : Utiliser une échelle de 1 à 5 plutôt que de 1 à 10 pourrait poser quelques problèmes. Selon mon expérience, l’échelle la plus efficace est celle de 1 à 10, car elle permet d’obtenir une meilleure marge de tolérance en cas d’évaluations erronées. De plus, fournir une légende peut aider le personnel sur le terrain à respecter les valeurs attribuées. Ne sous-estimez pas non plus les discussions de groupe ou les séances de brainstorming pour recueillir les avis des différents membres de l’équipe. Définissez clairement les tableaux et les échelles de notation pour chaque paramètre et assurez-vous qu’ils restent cohérents.
- Utilisation d’outils et de logiciels AMDEC ou similaires : Avoir mis en place un logiciel pour l’analyse AMDEC ou utiliser d’autres systèmes d’information tels qu’une GMAO (Gestion de Maintenance Assistée par Ordinateur) représente certainement un « nice-to-have ». Mais vous pouvez aussi faire appel à des outils complémentaires. Parmi les plus utiles figurent les diagrammes d’Ishikawa (ou diagrammes en arêtes de poisson), l’analyse des arbres de défaillance (Fault Tree Analysis), les outils d’analyse cause-effet et les matrices de probabilité. Ceux-ci sont fréquemment utilisés en combinaison avec la FMEA pour une gestion des risques plus efficace.
Adopter des normes internationales pour réduire la subjectivité lors de l’analyse AMDEC
Pour réduire la subjectivité dans l’analyse FMEA ou AMDEC, il peut être judicieux de se référer à des normes internationales, qui offrent des lignes directrices claires et des pratiques consolidées.
Voici quelques-unes des principales normes internationales qui peuvent vous aider dans le processus AMDEC :
- IEC 60812 : Cette norme internationale fournit des indications détaillées sur la manière de réaliser une analyse AMDEC. En particulier, la section 4 de l’IEC 60812 propose des lignes directrices pratiques et des recommandations pour effectuer l’analyse de manière efficace, abordant des questions telles que la composition de l’équipe, la documentation et l’utilisation du jugement des experts. L’adoption de cette norme permet de garantir que les analyses AMDEC sont réalisées de manière cohérente et selon des procédures reconnues.
- ISO/TS 16949 : Cette spécification technique, développée par l’International Automotive Task Force (IATF), intègre les exigences de l’ISO 9001 avec les besoins spécifiques du secteur automobile. Elle exige l’utilisation de techniques d’analyse des risques, y compris l’FMEA, pour améliorer la qualité et réduire les défauts dans les processus de production. L’intégration de ces exigences aide à standardiser les évaluations et à réduire la subjectivité.
- AIAG FMEA Manual : Il s’agit du manuel FMEA de l’Automotive Industry Action Group (AIAG), qui fournit un cadre détaillé pour la mise en œuvre de l’FMEA dans le secteur automobile, y compris l’utilisation du RPN dans l’analyse FMECA.
Que dit l’IEC 60812 ?
L’une des contributions centrales de cette norme concerne la gestion de la documentation (et, coïncidence, ce sera également la première chose qu’un organisme de certification vous demandera).
L’IEC 60812 propose une approche systématique et structurée pour réaliser une analyse AMDEC, garantissant que chaque étape soit bien documentée, en maintenant un format uniforme qui facilite la compréhension et l’utilisation des informations collectées.
D’ailleurs, les échelles mentionnées dans cet article sont les mêmes que celles suggérées par l’IEC 60812, qui recommande également de maintenir une documentation à jour comprenant les décisions prises, les scores attribués et les actions planifiées.
Applications pratiques de l’analyse AMDEC dans différents secteurs
Les modèles AMDEC (Analyse des modes de défaillance, de leurs effets et de leurs criticités) sont aujourd’hui appliqués et déclinés dans divers secteurs. Voici quelques exemples d’application de l’AMDEC dans certains de ces secteurs :
Secteur automobile : l’AMDEC est utilisée à la fois lors de la phase de conception et de production. Les entreprises du secteur automobile l’utilisent pour garantir que les véhicules respectent les normes de sécurité et de qualité, réduisant ainsi le risque de réclamations.
Secteur aéronautique : dans ce secteur, l’AMDEC est employée pour évaluer les risques associés aux systèmes de vol et aux composants critiques. Son application contribue à garantir la sécurité des vols et à standardiser les processus.
Secteur de la santé : parfois appliquée également à la gestion des équipements, tels que les dispositifs médicaux, mais plus souvent dans la gestion du risque clinique, elle est utilisée dans les hôpitaux et les centres de recherche pour identifier les erreurs potentielles, comme l’administration de médicaments incorrects ou l’évaluation des procédures chirurgicales (HFMEA).
Secteur manufacturier : les entreprises manufacturières utilisent l’AMDEC pour analyser les processus de production et optimiser les processus de maintenance (AMDEC de Moyen), identifiant les points critiques qui pourraient entraîner des pannes ou des inefficacités, assurant ainsi une meilleure fiabilité des produits et une réduction des coûts opérationnels.
Secteur logistique : dans ce secteur, l’AMDEC est appliquée aux processus afin de surveiller et prévoir les erreurs dans la chaîne d’approvisionnement.
Le rôle de la GMAO dans l’analyse AMDEC
Lorsqu’on choisit de s’engager dans un parcours tel que celui de l’analyse AMDEC/FMEA, il faut aussi être réaliste : votre organisation fonctionne-t-elle encore avec papier et crayon, ou par le biais du bouche-à-oreille ?
Dans ce cas, vous aurez beaucoup de mal à assembler les pièces d’information nécessaires.
Cependant, cela représente aussi un bon argument en faveur de la standardisation des processus.
Mon conseil sans détour ? Envisagez au moins de passer aux feuilles Excel, sinon vous risquez d’annuler tous vos efforts. Vous devriez probablement vous concentrer sur la résolution d’un problème à la fois, et celui de la numérisation des processus devrait être une priorité.
Dans ce sens, un logiciel de GMAO peut apporter une contribution énorme.
Grâce à des fonctionnalités telles que l’application mobile, l’accès rapide aux informations, le suivi des données et la mise à jour automatique des rapports, il permet de fluidifier le flux de travail et l’analyse dans son ensemble.
Les procédures standard assurent également une meilleure qualité des données.
Par exemple, les logiciels de GMAO permettent au personnel technique de compléter sur le terrain les analyses des causes de défaillance à l’aide de modèles standard, de connecter ces données à l’actif spécifique et de mettre à jour en temps réel vos rapports.
Ou encore, calculer automatiquement le IPR/RPN (Risk Priority Number) et la pondération des risques en fonction des précautions ou des procédures mises en place.
Inconvénients et limites des modèles AMDEC
La méthode AMDEC peut s’avérer assez longue et complexe. Bien sûr, ceux qui parviennent à numériser ces processus bénéficient d’un avantage considérable, mais cela nécessite tout de même une bonne organisation, l’implication de tous et une capacité d’analyse adéquate.
J’ajouterais également une observation importante. Plus on dispose de données au départ, mieux c’est. Dans certains cas, effectuer une AMDEC après que les défaillances se soient déjà produites est beaucoup moins utile, car généralement, il n’est pas possible de revoir beaucoup des options déjà choisies.