Qu’est-ce que le taux de panne : définition, formule et pourquoi est-il important ?
Le taux de panne (ou taux de défaillance) est à juste titre l’un des principaux indicateurs de la maintenance. Il offre une estimation en pourcentage du rapport entre le nombre de pannes auquel un actif, un système ou un composant est soumis pendant une période de temps déterminée.
Mais le taux de panne est-il vraiment l’indicateur de maintenance qui nous convient ? Et pourquoi de nombreux responsables de maintenance préfèrent-ils se concentrer sur un KPI très similaire, mais qui en pratique est son inverse ?
Définition du taux de panne
Le taux de panne (ou taux de défaillance; en anglais : Failure Rate) est un paramètre fondamental dans l’ingénierie de la maintenance. Il est défini comme le rapport entre le nombre d’éléments défaillants et le nombre total d’éléments contrôlés au cours d’un intervalle de temps spécifique.
Taux de panne ou Taux de défaillance?
Clarifions une chose tout de suite : y a-t-il une différence entre taux de panne et taux de défaillance ?
Réponse courte : Non.
Cependant, il m’est arrivé de discuter avec des personnes qui considèrent ces deux termes légèrement différents.
Taux de panne :
Le taux de panne se réfère généralement au nombre de pannes qui se produisent sur une période donnée, en fonction du nombre d’objets ou de systèmes surveillés. Il est souvent utilisé pour décrire le taux de pannes dans un contexte pratique et immédiat, comme dans les machines ou les véhicules, et peut être exprimé en pourcentage ou en fréquence (par exemple, nombre de pannes pour 1 000 heures de fonctionnement).
Taux de défaillance :
Le taux de défaillance est un terme plus technique qui se réfère généralement à la probabilité qu’un système ou un composant ne fonctionne pas correctement sur une période donnée. Ce taux est souvent utilisé en ingénierie ou dans les analyses statistiques et est particulièrement utile dans les modèles de fiabilité. Le taux de défaillance est souvent exprimé comme la probabilité de panne par unité de temps et est utilisé dans des contextes plus théoriques ou modélisés.
Comment calculer le taux de panne ? Formule
Le taux de défaillance est défini comme le rapport entre le nombre d’éléments défaillants après un temps ttt et le nombre d’éléments contrôlés. Le taux de panne moyen est l’intégrale normalisée du taux de panne (ou de défaillance) instantané sur un intervalle de temps donné.
Il se calcule avec la formule suivante :
Contenu de l'article
- Définition du taux de panne
- Taux de panne ou Taux de défaillance?
- Comment calculer le taux de panne ? Formule
- Taux de panne vs MTBF : En quoi le taux de défaillance diffère-t-il du Temps Moyen Entre Les Pannes (MTBF) ?
- À quoi sert le taux de défaillance ?
- Applications pratiques du taux de défaillance
- Taux de panne et courbes de panne : analyse des performances et de la fiabilité des actifs
- Principaux modèles de comportement des actifs par rapport au taux de panne
- Autres modèles de défaillances
- Quels sont les facteurs qui influencent le taux de panne ?
- Comment améliorer le taux de défaillance
- Réglementation et normes internationales pour le taux de panne
- Application pratique du taux de panne
- Outils supplémentaires pour l’analyse des pannes : aller au-delà du taux de panne
Découvrez la GMAO mainsim en direct.
Réservez une démonstration pour découvrir comment fonctionne la GMAO grâce à une démonstration personnalisée.
Taux de panne = Nombre de pannes / Temps considéré
Dit de manière un peu plus rigoureuse, le taux de panne se calcule avec la formule mathématique :
λ(t) = dNg / Nv ⋅ dt
où :
- dNg est le nombre de pannes ou de défaillances qui se produisent dans un court intervalle de temps dt,
- Nv est le nombre d’éléments encore fonctionnels au temps t.
Taux de panne vs MTBF : En quoi le taux de défaillance diffère-t-il du Temps Moyen Entre Les Pannes (MTBF) ?
Le terme taux de défaillance (ou Taux de Panne) est souvent lié à celui du MTBF (Mean Time Between Failures), c’est-à-dire le temps moyen entre les pannes.
En effet, le taux de défaillance est un indicateur de maintenance qui mesure la fréquence à laquelle un composant ou un système tombe en panne, en exprimant le résultat en pourcentage (%), tandis que le MTBF exprime le temps moyen qui s’écoule entre une défaillance et une autre.
En réalité, ces deux métriques de maintenance sont similaires, car elles sont l’une l’inverse de l’autre. En effet :
- MTBF : Temps moyen qui s’écoule entre une défaillance et une autre.
- Taux de Panne : Nombre de fois qu’un composant ou un système tombe en panne pendant une période de temps donnée.
En approfondissant, nous remarquons que ces deux indicateurs sont pratiquement l’opposé l’un de l’autre, au sens propre du terme :
- Taux de Panne : Nombre total de défaillances / Temps total de fonctionnement
- MTBF : Temps total de fonctionnement / Nombre de deˊfaillances
À quoi sert le taux de défaillance ?
L’analyse du taux de défaillance est un indicateur essentiel pour améliorer la fiabilité et la qualité des produits ou des actifs d’une entreprise.
L’identification et l’analyse du taux de défaillance poursuivent des objectifs cruciaux pour l’amélioration des processus de maintenance :
- Fiabilité : le taux de défaillance permet de calculer la fiabilité globale d’un système. Associé au suivi du MTBF (Mean Time Between Failures), ces deux indicateurs permettent de mettre en évidence la fréquence des pannes et le temps moyen entre celles-ci, nous offrant ainsi une estimation efficace de la fiabilité de nos actifs.
- Maintenance : le suivi d’indicateurs comme le taux de défaillance et le MTBF aide les responsables à planifier la maintenance préventive et à améliorer les plans de maintenance, ce qui réduit les coûts opérationnels et améliore l’efficacité des actifs.
- Sécurité : l’analyse du taux de défaillance a également des implications importantes en matière de HSE (Hygiène, Sécurité, Environnement). En particulier, elle contribue à l’évaluation correcte des risques associés aux défaillances, permettant des interventions rapides pour garantir la sécurité opérationnelle.
Applications pratiques du taux de défaillance
Le taux de défaillance est utilisé dans divers domaines, notamment :
- Conception et maintenance : il aide les ingénieurs et les techniciens à concevoir des systèmes plus fiables et à planifier des stratégies de maintenance préventive.
- Analyse des risques : il est essentiel pour les analyses de risques dans les secteurs industriels, où les défaillances peuvent entraîner des conséquences graves en matière de sécurité.
- Évaluation des performances : il permet aux entreprises de surveiller les performances de leurs installations et d’améliorer l’efficacité opérationnelle.
Taux de panne et courbes de panne : analyse des performances et de la fiabilité des actifs
Lorsqu’on analyse les performances des actifs, il est important de souligner que le taux de défaillance n’est presque jamais constant dans le temps.
Si l’on veut identifier un comportement typique des équipements et des systèmes, ce qui décrit le mieux un taux de défaillance classique est la “courbe en baignoire”.
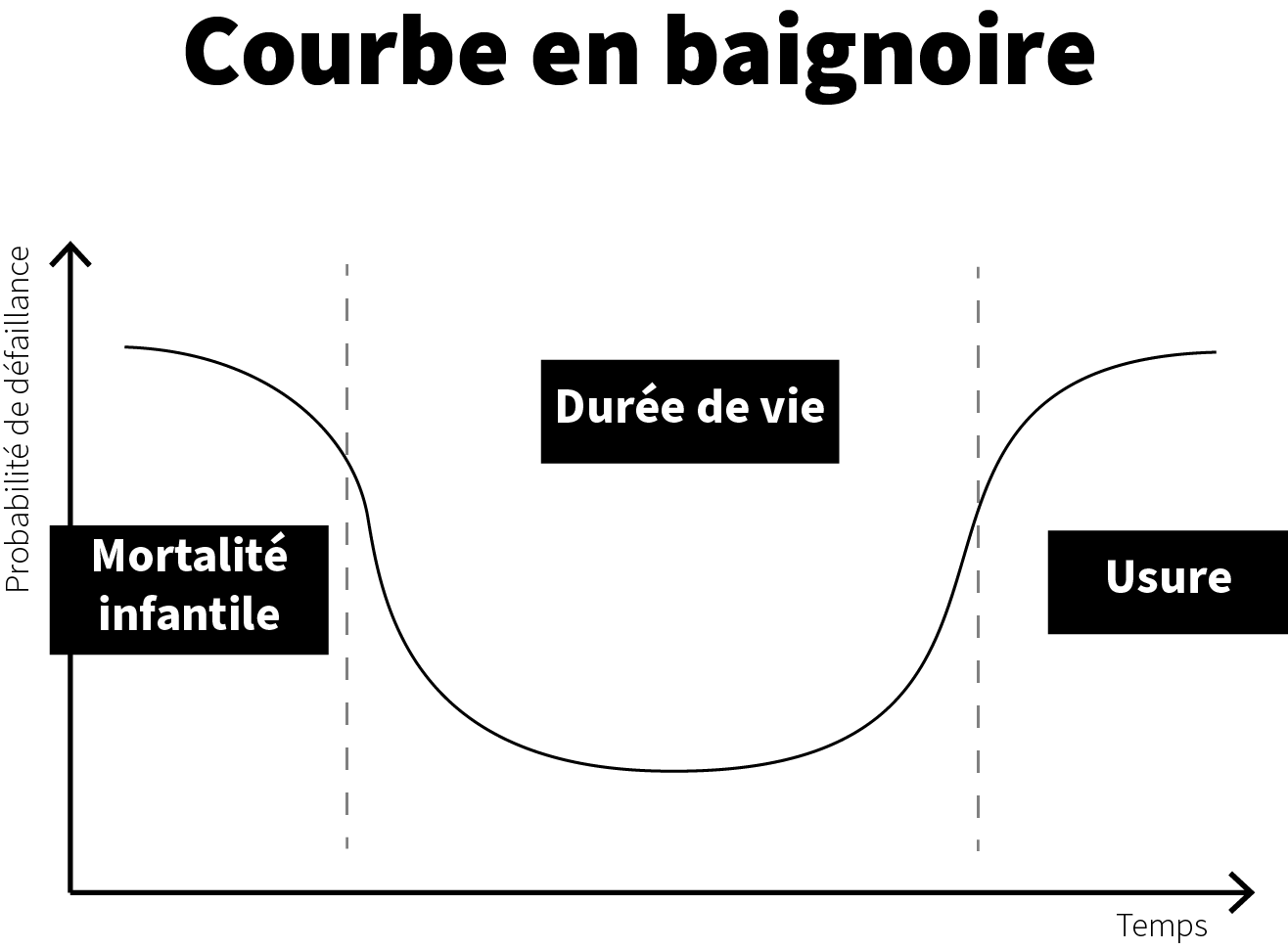
Fig.1 La courbe classique de défaillance en forme de baignoire
Principaux modèles de comportement des actifs par rapport au taux de panne :
Courbe en baignoire
Nommée ainsi en raison de sa forme (Fig.1), la courbe en baignoire est le modèle principal décrivant le comportement des actifs en matière de défaillances. Elle peut être divisée en 3 phases :
- Phase 1 – Mortalité infantile (défaillances précoces) : C’est la phase initiale, caractérisée par la mise en service de la machine ou du système, durant laquelle il existe une plus forte probabilité de défaillances. La courbe diminue rapidement en raison du remplacement des composants défectueux ou de la correction d’erreurs mineures.
- Phase 2 – Vie utile (défaillances constantes) : Durant cette période, le taux de défaillance se stabilise et reste relativement constant.
- Phase 3 – Phase finale (défaillances dues à l’usure) : À l’approche de la fin du cycle de vie utile, le taux de défaillance augmente rapidement en raison de l’usure et du vieillissement des composants.
Autres modèles de défaillances
Il existe également de nombreux autres modèles de défaillances, liés à l’âge ou aléatoires, décrits par d’autres courbes et modèles de distribution des pannes.
Voici quelques-unes des courbes de défaillance les plus renommées :
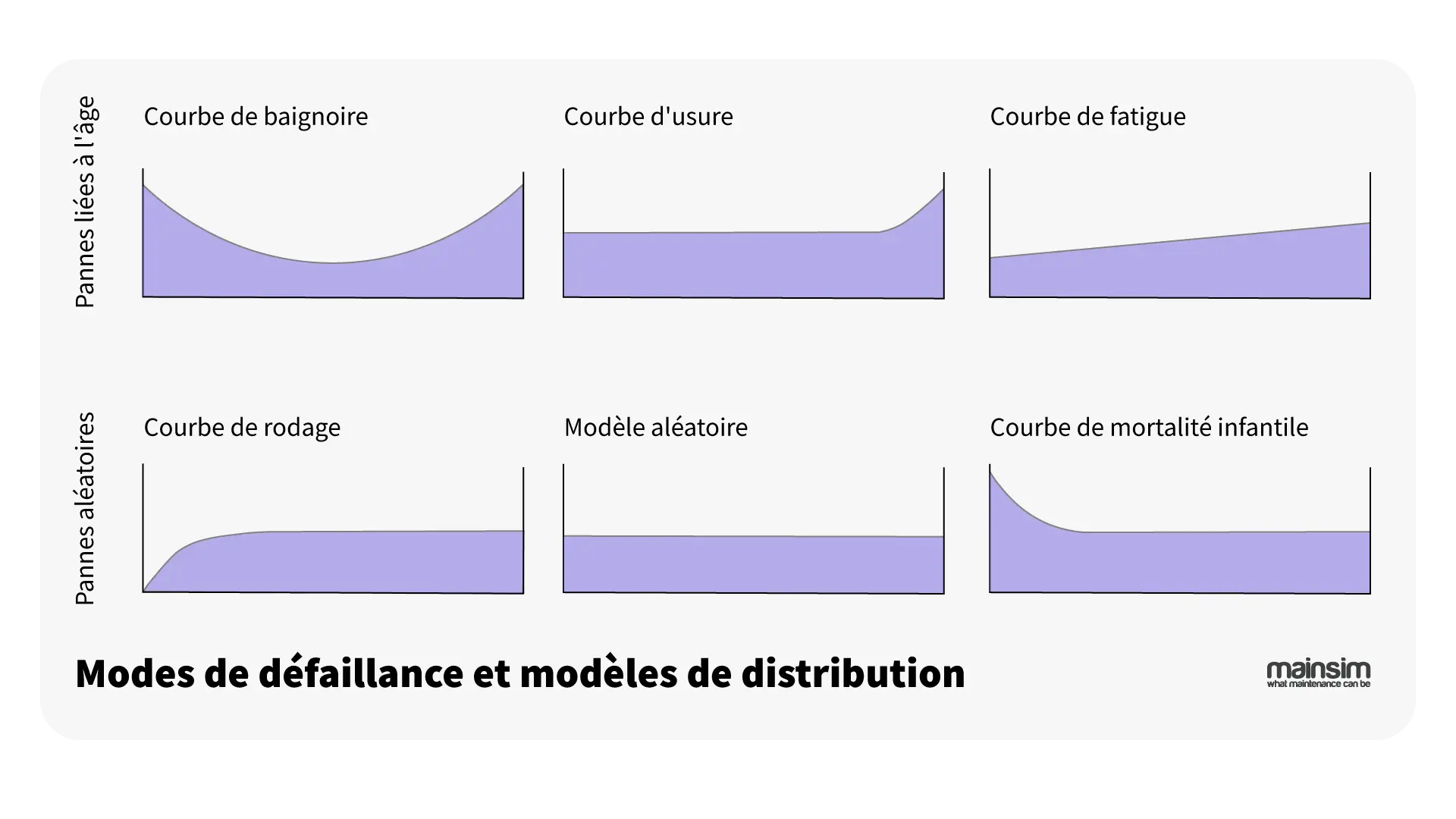
Dans l’infographie ci-dessous, je propose une analyse des patterns de défaillance en relation avec les principaux standards internationaux.
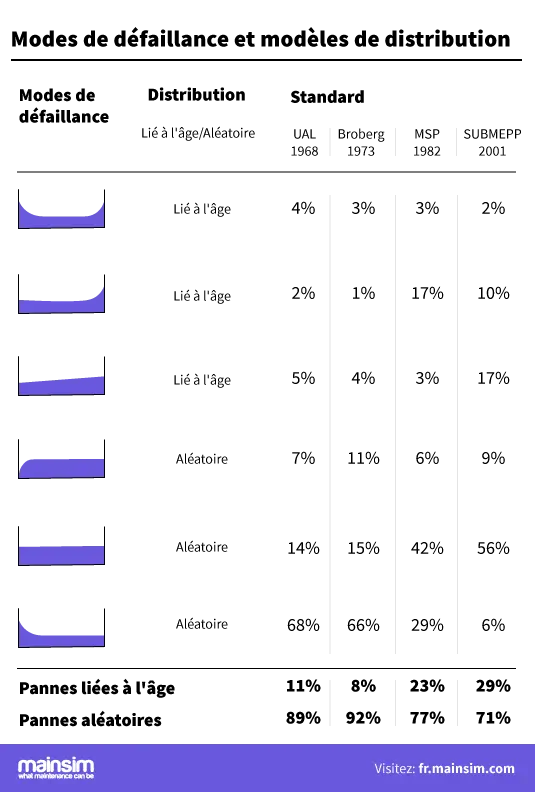
Quels sont les facteurs qui influencent le taux de panne ?
Le taux de défaillance, ou failure rate, est influencé par une série de facteurs qui peuvent être regroupés en 5 catégories principales :
- Qualité des composants
- Processus de production
- Conditions environnementales
- Charges mécaniques
- Usure et vieillissement
Comprendre ces facteurs permet aux entreprises de mettre en œuvre des stratégies adéquates visant à améliorer la fiabilité des produits ou des machines, réduisant ainsi les coûts associés aux défaillances et les risques connexes.
En analysant les données relatives au taux de panne, ainsi que les autres indicateurs de maintenance, les entreprises peuvent mettre en place des mesures proactives (notamment des plans de maintenance) pour optimiser les performances et améliorer la fiabilité des ressources.
Voici une liste plus détaillée des facteurs qui peuvent influencer le taux de panne :
- Qualité des composants : L’utilisation de matériaux et de composants de haute qualité est essentielle au bon fonctionnement d’un actif. Des composants de mauvaise qualité peuvent entraîner des pannes plus fréquentes et nuire négativement à la durée de vie de l’actif.
- Processus de production : Des processus de production adéquats, tels que le rodage ou le contrôle qualité, peuvent réduire les pannes et les défauts initiaux caractérisant la dite mortalité infantile.
- Conditions environnementales : Les conditions dans lesquelles un actif opère ont un effet important sur sa fiabilité. La température, l’humidité, les vibrations ou la présence d’agents corrosifs peuvent influencer de manière significative le taux de défaillance, accélérant l’usure et le vieillissement des composants.
- Conception du produit : Les erreurs de conception affectent la robustesse ou la capacité à résister aux contraintes mécaniques ou électriques, par exemple. Un design inadéquat peut entraîner une exposition accrue de l’actif à des défaillances fréquentes et répétitives.
- Modèles d’utilisation : La manière et l’intensité avec lesquelles une machine est utilisée déterminent son taux de défaillance. Une utilisation intensive ou non conforme aux spécifications techniques peut augmenter considérablement le taux de défaillance.
- Maintenance inadéquate : Les inspections régulières, le suivi et la maintenance préventive, même de petite envergure comme la lubrification d’un engrenage, ont souvent un impact décisif sur le taux de défaillance d’un actif et sur la capacité de l’équipe de maintenance à anticiper des pannes imprévues.
- Usure et vieillissement : Les matériaux soumis à des charges répétées peuvent subir des phénomènes de fatigue, d’usure et de vieillissement, ce qui conduit à des ruptures, des défaillances et des arrêts imprévus. Cela correspond à la dernière phase du cycle de vie d’un actif.
Comment améliorer le taux de défaillance :
Que peuvent faire les entreprises et les équipes de maintenance pour améliorer le taux de panne, c’est-à-dire réduire le pourcentage de pannes d’un actif ?
Pour réduire le taux de défaillance, il est essentiel d’adopter certaines meilleures pratiques et stratégies efficaces :
- Maintenance préventive : Mettre en place un programme sérieux de maintenance (même basé sur le temps) aide les responsables de la maintenance à identifier et résoudre les problèmes avant qu’ils ne deviennent critiques.
- AMDEC et RCA (Root Cause Analysis) : Utiliser des techniques comme l’AMDEC (en englais FMEA) pour identifier et analyser les points de défaillance individuels et la Root Cause Analysis (Analyse des causes racines) pour optimiser les plans de maintenance en fonction des résultats obtenus.
- Maintenance conditionnelle et maintenance prédictive : Ces deux stratégies, maintenance conditionelle et la prédictive, visent à intervenir sur un actif avant qu’une panne ne se produise, en basant la décision sur des données, telles que des relevés sur le terrain (par exemple, la lecture d’un compteur) ou des capteurs IoT appliqués aux actifs.
- Formation continue du personnel : Éduquer l’équipe sur les risques et les procédures pour gérer les pannes de manière efficace et instaurer une culture vertueuse de la maintenance peut avoir des effets importants sur la réduction des taux de panne et sur la fiabilité des actifs.
- Inspections : Appliquer des méthodologies comme le RBI (Risk-Based Inspection) pour programmer les inspections en fonction du risque et améliorer la fiabilité des composants ou des actifs réduit le risque de pannes imprévues.
Réglementation et normes internationales pour le taux de panne
En France, le taux de défaillance et, de manière générale, les paramètres liés à la fiabilité, tels que le MTBF (Mean Time Between Failures) ou le MTTR (Mean Time To Repair), sont traités dans des normes techniques faisant référence aux normes internationales et européennes. Bien que ces normes ne soient pas spécifiquement françaises, elles sont adoptées en France par des organismes comme l’AFNOR (Association Française de Normalisation).
Voici quelques normes principales qui traitent du taux de défaillance et des sujets connexes :
IEC 61508 – Sécurité fonctionnelle : Il s’agit d’une norme fondamentale pour la sécurité fonctionnelle des systèmes électroniques et électriques, couvrant des concepts tels que le taux de défaillance, la fiabilité et la probabilité de défaillances dangereuses.
NF ISO 31000 Gestion des risques : Cette norme établit les lignes directrices générales pour la gestion des risques, y compris la fiabilité des systèmes et la gestion des défaillances. Bien qu’elle ne traite pas spécifiquement du taux de défaillance, elle fournit un cadre pour aborder les risques associés à la maintenance et aux systèmes complexes.
Dans des secteurs spécifiques comme celui de l’aérospatial/militaire ou du pétrole/gaz, le taux de défaillance est souvent régulé par des normes spécifiques, telles que :
- STANAG 4107 : Norme de l’OTAN pour la gestion de la qualité, incluant des critères de fiabilité des ressources.
- ISO 14620-1 : Régule les systèmes spatiaux et inclut des mesures de fiabilité.
- ISO 14224 : Adoptee également en France, cette norme concerne la collecte et l’analyse des données de fiabilité et de maintenance dans l’industrie pétrolière et gazière, incluant des paramètres comme le taux de défaillance et l’analyse statistique des défaillances.
De plus, il existe des normes spécifiques de l’AFNOR qui complètent et intègrent les normes internationales, telles que :
- NF X 60-010 : Lignes directrices pour la fiabilité des systèmes.
- NF E-85-410 : Spécifications techniques pour la maintenance industrielle.
En France, ces normes sont applicables pour :
- Projets industriels : nécessitant le suivi du taux de défaillance et le calcul du MTBF pour les machines et systèmes.
- Audits de sécurité : pour l’évaluation des risques et de la fiabilité.
- Conformité réglementaire : des secteurs comme l’énergie, le transport ferroviaire et la production aérospatiale sont soumis à des obligations strictes en matière de fiabilité.
Application pratique du taux de panne :
Le taux de défaillance annualisé (AFR) trouve des applications pratiques dans divers contextes, notamment dans la production, en contribuant à améliorer la fiabilité des installations et des systèmes industriels. Voici quelques exemples par secteur :
- Manufacture et production : Le taux de panne est utilisé pour améliorer la qualité des produits et des actifs impliqués dans la production. Les responsables de la maintenance dans ce domaine se concentrent sur l’analyse des pannes pour identifier les défauts ou problèmes, dans le but d’optimiser les processus de production, de réduire les déchets et le nombre total de pannes.
- Secteur aéronautique : Dans ce secteur, la fiabilité est cruciale. Le taux de défaillance aide à évaluer la probabilité de pannes des composants clés, permettant ainsi une conception plus robuste et une maintenance ciblée pour garantir la sécurité.
- Ingénierie clinique : Dans ce secteur, les ingénieurs biomédicaux et les responsables de la maintenance doivent respecter les obligations réglementaires en matière d’inspections et d’étalonnages, et utilisent le taux de panne pour avoir une vue d’ensemble et comparative de l’état de fiabilité de leurs dispositifs et équipements.
- Transports : Le taux de défaillance est utilisé pour optimiser la sécurité et les performances des véhicules, avions et trains. Dans ce secteur, les ingénieurs de la maintenance utilisent le taux de défaillance en complément d’autres métriques, KPI et outils d’évaluation tels que l’MTBF, l’Analyse des causes racines (RCA) ou les modèles FMEA et FMECA.
- Énergie, Oil & Gas : Dans ces secteurs, les équipes de maintenance effectuent des contrôles réguliers sur l’état des installations et des systèmes, par exemple en lisant les compteurs, et utilisent le taux de défaillance comme KPI pour optimiser la maintenance préventive et conditionnelle.
Outils supplémentaires pour l’analyse des pannes : aller au-delà du taux de panne
Le taux de panne est un indicateur important de maintenance, mais il n’est pas le seul. Comme souvent avec les données, elles prennent tout leur sens lorsqu’elles sont mises en relation entre elles. La maintenance n’est pas faite pour les cœurs faibles !
Voici quelques outils fréquemment utilisés dans l’analyse des pannes en complément du taux de défaillance :
- Root Cause Analysis (RCA – Analyse des causes de défaillance) : En plus des diagrammes de causes et effets (type diagramme en arêtes de poisson) ou de l’analyse des 5 pourquoi, il existe des logiciels spécifiquement dédiés à l’analyse des causes racines (RCA). En réalité, cette fonctionnalité est désormais souvent intégrée dans les logiciels de GMAO (Gestion de Maintenance Assistée par Ordinateur), qui sont des outils pour la gestion de la maintenance et des actifs. Ces systèmes simplifient la collecte et l’analyse des données, facilitent le partage des informations entre les membres de l’équipe et aident les responsables de la maintenance à prendre des décisions éclairées.
- FMEA (Failure Modes and Effects Analysis) : En français AMDEC (Analyse des Modes de Défaillance, de leurs Effets et de leur Criticité), il s’agit d’une méthode systématique permettant d’identifier les modes de défaillance, d’analyser leurs effets et d’évaluer les risques potentiels. Cette approche permet de classer les pannes selon des critères tels que la gravité et la probabilité, ce qui aide à prioriser les actions correctives. C’est un outil classique utilisé par les équipes qui adoptent une approche de gestion de la fiabilité des actifs, et il est également intégré dans les logiciels GMAO modernes comme mainsim.
- Analyse de Weibull : Ici, nous entrons dans le domaine statistique. La distribution de Weibull est utilisée pour analyser les différents comportements de pannes et est particulièrement utile pour estimer des paramètres comme l’MTBF (Mean Time Between Failures) ou la fonction de fiabilité. Cet outil est souvent utilisé pour les analyses de durée de vie et la prédiction des pannes.
- Fault Tree Analysis (FTA – Analyse des arbres de défaillance) : L’FTA (Fault Tree Analysis) utilise une approche top-down (de haut en bas) pour explorer les causes des pannes à travers un diagramme en arbre. Cela permet une analyse approfondie des pannes pour des systèmes complexes, et est souvent inclus dans les rapports classiques de maintenance fournis par des systèmes GMAO ou EAM (Enterprise Asset Management).
- Simulation Monte Carlo : Il s’agit d’une technique statistique qui génère des échantillons aléatoires à partir de distributions de probabilité pour estimer des variables d’intérêt. Elle est utilisée pour analyser l’incertitude des données de défaillance et évaluer le risque associé à différents scénarios. Bien que cette technique soit puissante, elle nécessite une expertise technique avancée et est souvent utilisée par des ingénieurs spécialisés.
- Machine Learning et Intelligence Artificielle (IA) : Le machine learning et l’intelligence artificielle peuvent grandement améliorer la production de données qualitatives pertinentes. Les techniques de machine learning sont utilisées pour analyser de grands volumes de données de défaillance, identifier des schémas, des anomalies et des motifs spécifiques. Ces informations pourraient ne pas être évidentes avec les méthodes traditionnelles. L’IA peut, quant à elle, jouer un rôle crucial dans l’éducation aux données. Par exemple, mainsim intègre l’IA au sein de kla GMAO sous forme d’un Smart Assistant. Cet assistant est capable d’attirer l’attention de l’utilisateur sur des anomalies ou des variations significatives des métriques telles que l’MTBF, le taux de panne ou la répétition de types spécifiques de défaillances. Cela transforme radicalement l’approche des utilisateurs vis-à-vis des données, non seulement en réduisant le temps passé à les analyser, mais aussi en permettant une réaction plus rapide face aux problèmes.
En conclusion :
Le taux de panne est une métrique essentielle pour la maintenance, utilisée pour évaluer la fiabilité des composants et des systèmes. Son unité de mesure est le FIT (Failures per billion hours). La formule pour le calculer est l’exact opposé de celle utilisée pour calculer le MTBF (Mean Time Between Failures), c’est-à-dire le temps moyen entre deux défaillances consécutives. Ces deux mesures sont essentielles pour optimiser les opérations de maintenance, réduire les défaillances et améliorer les performances globales des équipements.
Cela pourrait également vous intéresser :
MTBF - Mean Time Between Failures
Qu’est-ce que c’est, comment le calculer et comment améliorer le temps moyen entre les pannes
Indicateurs de maintenance
Découvrez quels sont et comment calculer les principaux indicateurs et KPI de maintenance.
Rejoindre les experts
Ou découvrez le mainim GMAO avec la playlist vidéo.